Тақырыбы: ТЕХНОЛОГИЯЛЫҚ МАШИНАЛАРДЫ ЖӨНДЕУ
Мазмұны
1. Жабдықты пайдалану және техникалық қызмет көрсетуін ұйымдастыру ..........................
2. Жөндеу жұмыстарын ұыймдастыру және басқару ................................................................
3. Жабдықтардың тозуы ...............................................................................................................
4. Машина бөлшектерін қалпына келтіру ...................................................................................
5. Бейметалдан жасалған бөлшектерді жөндеу ..........................................................................
6. Машиналар мен жабдықтарда жөнделудің технологиялық процессі ..................................
7. Жабдық қаңқаларын жөндеу ....................................................................................................
8. Машиналар типтік түйіндерін жөндеу ....................................................................................
9. Машиналардың типтік түйіндерін жөндеу .............................................................................
10. Бағаналы аппараттарды жөндеу .............................................................................................
11. Жылуалмастырғыш аппараттарды жөндеу ...........................................................................
12. Ыдыстық аппараттарды жөндеу .............................................................................................
13. Сорапты-компрессорлық жабдықтарды жөндеу ...................................................................
14. Құбырлар мен арматураларды жөндеу ..................................................................................
Өнеркәсіп орындарынағы жөндеу шаруашылығының ұйымдастырылуы
Өнеркәсіптік орындарындағы жөндеу нысандары, бұл ғимараттар, үймереттер, технологиялық жабдықтар мен көлік құралдарының барлық түрлері. Бұл нысандардың пайдалану сенімділігі арттыруда, жөндеу қызметіне үлкен жауапкершілік жүктеледі.
Жөндеу-техникалық қызмет сапасын арттыру, бұл ұдайы жөндеу технологияларын жетілдіру, жөндеу персоналдарының квалификацияларын жоғарлатуды көздейді. Жөндеу жұмыстарының сапасы, көпшілігінде еңбекті механикаландыру қарқындылығына, қызметтерді орталықтандыру мен амандандырылу дәрежесіне байланысты болады. Бұл факторлар техника-экономикалық көрсеткіштердің артуына алып келеді, яғни өнімнің өзіндік құнының төмендеуі мен еңбек өнімділігінің артуына.
Жөндеу шаруашылығының орталықтандырылған жүйесінде кәсіпорынның негізгі қызметтерінің функцияларын дәйекті түрде пысықтап белгілеу қажет.
Бас механик қызметі технологиялық және механикалық жабдықтарды, сонымен қатар технологиялық үймереттерді, коммуникациялар, металлоконструкциялар мен эстакадаларды пайдалану және жөндеуді басқарады.
Бас энергетик қызметі міндетіне, электржабдықтардың, букмекерлік қондырғыладың, суқұбырлары мен канализациялық тораптардың, байланыс желілерінің қауіпсіз пайдалануы мен олардың жөнделуін қадағалау бойынша іс-шаралар кіреді.
Бас приборшы қызметі – бақылау-өлшеу және реттеу приборларын, белгі беру және блакировкалар құралдарын пайдалану және оларды жөндеуді қадағалау мәселелері кіреді.
Бас архитектордың қызметі өндірістік ғимараттар мен үймереттердің, технологиялық және энергетикалық жабдықтардың жылу изоляцияларының күйін қадағалау және оларды жөндеу болып табылады. Бұл қызмет өндірістік алаң ауданы 100 000 м2 асатын ірі кәсіпорындарда жеке қызмет ете алады, ал кері жағдайда бас механик құзырына жатады.
Бас механик кәсіпорынның бүкіл жөндеу шаруашылығын басқарады.
Жөндеу-құрылыстық және жөндеу-механиктік цехтар әкімшілік түрде зауыт директорына, ал техникалық – бас механикке бағынады. Бас механик бөлімі зауыт басқармасының құрамына кіреді және де құрамы төмендегідей функционалдық қызметтерді атқарады:
1. Кәсіпорындағы жабдықтардың күйін жүйелі қадағалау;
2. Бүкіл кәсіпорын бойынша жабдықтарды жөндеу доспарын түзу;
3. Жөндеу қызметі бойынша ұйымдастыру – техникалық іс-шараларды әзірлеу;
4. Жөндеу жұмыстарын орындаудағы жаңа жоғарғы өнімді технологиялық процесстерді енгізу;
5. Жөндеу жұмыстарын құнын бағалау;
6. Негізгі жабдықтардың орташа және күрделі жөндеулері жөнінде кварлтадық жинақтық есеп беру.
Бұл бөлім құрамына жоспарлы-сақтық жөндеу бюросы кіреді (ЖСЖ)
Конструкторлық бюро (БМБ КБ) жөндеу сызбаларын әзірлеуменен аспаптарды жобалауменен, сонымен қатар жөндеу жұмыстары механикаландыруменен және жабдықты модернизациялауменен айналысады.
Техникалық қадағалау бөлімі – жабдықтарды тексеру және сынау, олардың дұрыс пайдалануын, жөндеу жұмыстарының сапасын тексеруді, және де аппатың себептерін анықтауды орындайды. Яғни барлық жабдықтардың жұмысқа қабілетті күйде болуын қадағалайды.
Жөндеу-құрылыс цехы өндірістік және тұрмыс ғимараттарын жөндеу, сондай-ақ жаңа үймереттерді салуменен айналысады. Шағын кәсіпорындарда ЖҚЦ ЖМЦ құрамына кіреді.
ЖМЦ зауттың бүкіл жабдықтарының орталықты жөнделуін атқарады, және де жеке жөндеу жұмыстарын орындауға арналған бірнеше мамандандырылған учаскелерді қарастырады.
Әрбір технологиялық цехтарды цех механигі және оған құзырлы жөндеу бригадалары қарастырылады, және де бұл цехтағы технологиялық жабдықтардың жөнделуін қамтамасыз етеді.
Бас механик, приборшы, энергетик, архитектор бөлімдері қосалқы сипаттағы және де жөндеу-техникалық мақсаттағы өндірістік бөлімдер болып табылады да, жиі кәсіпорындарда орталықты басқару үшін техникалық директоры қызметі ұйымдастырылады. Бұл қызметтің басқару құрылымы төмендегідей.
Бұндай басқару барысында кейбір қызметтерді тәуелділігі өзгереді. Жөндеу өндірістік басқарма құзырынан дедетоскопиялық зертханасы бар техқадағалау, мемкентехқадағалау секторлары, ЖКБ жеке бөлінген. Бұл бөлім құзырында ЖМЦ, ЖҚЦ, ЭЖЦ қалады.
Жөндеу қызметі ұйымдастырылу принципі бойынша орталықтық, бейорталықтық және аралас болуы мүмкін.
Орталықтық техқызмет көрсету және жөндеу жұйесінде бүкіл жабдықты жөндеу ЖМЦ күшіменен атқарылады. Химия зауыттарында жеңіл демонтаждалатын және жеңіл де демонтаждалмайтын жабдықтарды жөндеу ЖМЦ бригадаларыменен немесе мамандандырылған бригадаларменен жүзеге асырылады. Бұл бригадалар жеке технологиялық цехқа бекітіледі немесе барлық цехтарға қызмет көрсетуші сипатта болады. Сондай-ақ мұндай бригадалардан басқа слесарлар, пісірушілер, қазаншылар және такелаганиктерден тұратын кешенді жөндеу бригадалары ұйымдастырылады да олар күрделі технологиялық жабдықтарды жөндеуге мамандандырылады. (пештер, диірмендер, т.б.)
Жартылай орталықтандырылу жағдайында технологиялық цехтық жөндеу бригадалар техқызмет көрсетуменен айналысады да, ал барлық жөндеулер ЖМЦ күшіменен орындалады.
Бейорталықтың ТҚК және Ж жүйесінде жөндеудің барлық түрлері технологиялық цехтардың учаскелерінде орындалады.
Аралас ТҚК және Ж жүйесінде жөндеулерге ЖМЦ, және технологиялық цехтардың жөндеу бригадалары қарастырылады.
Бұл кезед ЖМЦ-да жабдықты күрделі жөндеу мен қосалқы бөлшектерді дайындау жұмыстары орындалады.
Жабдықтарды жөндеу өз бетінше өндіріс болмағандықтан, жөндеу жұмыстарын орталықтандыру экономикалық өтелімді шекте болуы тиіс. Яғни жөндеу жұмыстарын орындау барысындағы оперативтіліктің төмендеуі мен жөндеуде тұруының ұзақ болуынан орын алғын өндірістік шығындарды болдырмайтындай шекте. Толық орталықтандыру шағын цехтар үшін тиімді, ал орташа және ірі цехтар үшін ТҚК және Ж-дің аралас жүйесі тиімді.
Орталықтандырылу дәрежесі орталықтандырылу клэффициентімен анықталады Кц:
Кц – Р/Р0
Мұнда: Р – орталықтық жөндеу қызметінде қатысатын жұмысшы саны;
Р – кәсіпорынның жөндеу персоналдарының жалпы саны.
Жұмыстың ұйымдастырылуы бойынша жөндеулер келесідегідей топтастырылуы мүмкін:
- жұмыс орны бойынша – 1) машина орнатылған; 2) бүкіліменен машинаны ЖМЦ жөндеу; 3) машина қаңқасын орнатылу орнында, ал бөліктерін ЖМЦ-да жөндеу;
- жөндеу көлемі бойынша – 1) бөлшектік-тозған бөлшегін ауыстыру; 2) тораптық-жеке тораптарын ауыстыру; 3) машиналы-машинаны бүкілдей резервтік машинаменен ауыстыру;
- жұмыстың атқарылу уақыты бойынша – 1) бүкіл жылғы біркелкі таратылған; 2) технологиялық қондырғы жұмыс тоқтатылған мерзімге (тоқтатылғандағы жөндеу); 3) жылдың бір мезгіліне жоспарланған (наухандық жөндеу).
Жабдықты пайдалану және техникалық қызмет көрсетуін ұйымдастыру. Жабдықты пайдалану, пайдаланудың жалпы ережелері
Жабдықты пайдаланудың бүкіл мерзімінде оның сенімді және үздіксіз жұмысын қамтамасыз ететін техникалық іс-шаралар комплексін жұмысқа пайдалануды ұйымдастыру деп атаймыз. Бұл іс-шаралар техникалық қызмет көрсетудің барлық кезеңдерінде орындалады: тасымалдау мен қоймаларда сақталуынан оның тағайындалуы бойынша қолдануына дейін. Жабдықтың жарамдылығын қамтамасыз ету бойынша орындалатын жұмыстар профилатикалық жұмыстар және жөндеулер деп бөлінеді. Профилактикалық жұмыстар дегеніміз: техникалық күтім (қызмет) көрсету және бақылау жүргізу.
Жабдық күйіне жасалатын бақылау машинаның жұмыс параметрлерінің төл құжат деңгейіне сәйкестігін анықтаудан тұрады. Әдетте, жабдықтың өнімділігі мен өнім сапасы, ондағы діріл деңгейі мен бөгде шудың болмауын, температуралық параметрлерді, тұтынатын энергиянын шығынын және т.б. тексеріледі. Осы параметрлер бойынша диагностикалау әдісімен машинаның және аппараттың техникалық күйі жайында жеткілікті дәл мәлімет алуға болады. Бақылау мерзімділігін конструкторлар анықтайды да, бұл туралы мәліметтер жабдықтың техникалық құжаттарында келтіреді.
Техникалық қызмет көрсету бойынша орындалатын жұмыс көлемі және мерзімділігі техникалық құжаттармен анықталады. Егерде техникалық құжаттар жоқ болса, онда құрылымы ұқсас және бірдей жағдайда, жұмыс істейтін машинаның нормативті құжаттары жетекшілікке алынады. Техникалық күтім көрсету бойынша жұмыс құрамына мыналар кіреді: машинаны майлау; түйіндер мен бөлшектерін ретке келтіру; бекітпелерді қысып бекіту және басқада осыларға ұқсас операциялардан тұрады.
Жабдықты жұмыс қабілеттіліг мен техникалық ресурсын қалпына келтіру бойынша орындалатын операциялар комплексін жөндеу деп атаймыз.
Егерде тек қана жабдықтың жұмыс қабілеттілігін қалпына келтіру бойынша жұмыстар орындалатын болса, онда бұл жұмыстарды техникалық қызмет көрсету деп атайды. Техникалық қызмет көрсету мен жөндеуді жабдықты жұмыс қабілетті жағдайда ұстау үшін қажетті өзара байланысты шаралар комплексі ретінде қарастырады. Бұл екі ұғым іс-тәжрибеде қолданылып жүрген «Техникалық қызмет көрсету және жөндеу жүйесі» негізінде қолданылған. Бұл жүйенің көрсеткіштері өзін іс-тәжрибеде жақсы көрсете алды, сондықтан бұл бір тұтас мәселелер комплексін шешуге мүмкіндік береді. Сондай-ақ техникалық қызмет көрсету және жөндеуге кететін еңбек және уақыт шығынын анықтауға мүмкіндік береді. Және де көптеген жабдық түрі үшін шұғыл шығындарды (жабдықтың нақты күйін көрсетуші техникалық қызмет көрсету мен жөндеуге жұмсалған қосымша шығындар, материалдың қосымша шығындары, жөндеу технологиясын қолдану ерекшелігі және т.б.) анықтайды. Көптеген анықтамаларда жөндеуаралық циклдің, жөндеудің еңбек сыйымдылығының және жөндеуде тұру уақытының шамасы бойынша мәліметтер, сондай-ақ жөндеуді жоспарлауға қажетті басқа да нормативтер келтіріледі. Техникалық күтім көрсету мен бақылаудың, техникалық қызмет көрсету мен жөндеуді жүргізумен үйлестіре отырып сапалы орындау жабдықтың ұзақ мерзімді және сенімді жұмыс істеуін қамтамасыз етеді.
Жабдықты сақтау және пайдалануға тапсыру
Тозған жабдықты ауыстыруға немесе технологиялық жүйені монтаждауға қажетті жабдықтар, пайдалану орнына түрлі тасымалдағыштардың (су, теміржол және автомобиль) көмегімен тасымалданады.
Тасымалдау процессі тасымалдану жабдықтарының сақталуының осал жері болып келеді, себебі бұл кезде жеке түйіндердің деформациясы, сыртқы және қорғалмаған беттердің коррозиялық тозуға ұшырау мүмкін.
Дайындаушы-зауыты жабдықты жөнелту кезінде оын орамдарға орауы тиіс және де жүкке берілген тізімде жұмысқа пайдалану құжаттары: 1) техникалық сипаттамасы; 2) жұмысқа пайдалану нұсқаулары; 3) техникалық қызмет көрсету, монтаждау, ретке келтіру және жұмысқа қосуға қажетті нұсқаулар; 4) төл құжат; 5) қосалқы бөлшектер мен құралдар тізімі келтіріледі.
Ірі салмақты жабдықтар үшін, бөлшектелген түрде жеткізілетін жанасушы орындарын белгілеудің шартты белгісін және де жабдықтың бөлшектелген монтаждық біліктері тізімін көрсете отырып қосымша таңбалаушы сұлбасы беріледі.
Жүк тұтынушыға келіп түскен кезден бастап, жүктің сақталуын тұтынушы толық жауапкершілігіне алады. Сонымен қатар келіп түскен жабдықтың сақталуы тапсырма берушінің міндетіне кіреді.
Сақтау орны мен тәсілін таңдап қабылдауға қойлатын негізгі талаптар: бүтінділігін қамтамасыз ету; коррозиялық тозудан және ортаның басқада әсерінен қорғау; жүк көтергіш жабдықтардың болуы. Осыған орай жабдықты шаңның шоғырлануы үлкен орындарда, агрессивті қышқылдық және сілтілік ортасы бар орында сақтауға қатаң тиым салынады.
Қоймада 9 айдан артық мерзімде сақталған жабдықтардың ескі майлары жаңа майлармен алмастырылып, қайтадан сақтауға дайындалады. Негізінен жабдықтар қоймада сақталады және де бұл қоймалар келесі төрт типке бөлінеді: 1) ірі салмақты жабдықтар сақталатын ашық алаңдар; 2) тек қана атмосфера әсерінен қорғайтын жартылай жабылған алаңдар мен қалқалар; 3) жабық, бірақ жылытылмайтын қоймалар; 4) жабық және жылытылатын қоймалар. Сақтау тәсілін таңдап қабылдау жабдық түріне және мекеменің мүмкіндігіне байланысты болады.
Жабдықты монтаждауға берер алдында, ол тиісті дәрежеде дайндықтан – монтаждау алдында тексеруден өтуі тиіс. Бұл кезде орындалатын жұмыс тізімі шамамен төмендегідей болады:
· жабдықты оралған орамдардан аршу;
· ашық және механикалық өңделген беттерді қорғаушы құрылымдар мен сақтандырғыш май қабатынан тазарту;
· жабдықты шаң мен ластардан тазарту;
· техникалық шартпен талап етілген жағдайда, майлау майын ауыстыру;
· сырт көзбен тексере отырып жинақ біліктер жинақтылығыш комплектілігін және олардың техникалық күйін тексеру.
Қажет болған жағдайда жабдықты «бос» жүрісте байқап көреді. Монтаждаудан соң жабдықты жұмысқа пайдалануға тапсырады.
Жабдықты жұмысқа пайдаланудан бұрын келесі дайындау жұмыс тарын орындау қажет: коммуникациялық құбырларға және электр торабына жалғау; машинаны ретке келтіріп міндетін орындауға дайындау қажет; «бос» жүріс тәртібінде және де жұмыс жағдайында байқап көру. Іске қосар алдындағы жұмыстар мазмұны мен орындалу тәртібі пайдалану құжаттарымен тәртіптелінеді.
Жабдықты пайдалануға тапсыру актымен бекітіледі. Актыда сырттай бақылап тексеру нәтижелері келтіріледі. Қажет жағдайда байқау қысымында (егерде бұл жұмысқа пайдалану құжаттарында көрсетілген болса), «бос» жүрісте және күш түсіре отырып байқау, өнімнің бір қатар байқау партиясын алу жұмыстарын жүргізеді. Жабдықтың жұмысқа пайдалануға қабылдағаны жайындағы актыға, оның техникалық күйіне жауапты тұлға қол қояды. Қазақстан Республикасының өнеркәсіпте жұмысты қауіпсіз жүргізуді қадағалау және кең қадағалау жөніндегі мемлекеттік комитетіне (КЕНТЕХҚАДАҒАЛАУМЕКОМ) бағынышты (қарасты) жүк көтергіш жабдықтар, электр қондырғылары мен қазаңдар комитет инспекциясының тексеруінен соң жұмысқа пайдалануға беріледі.
Бақылау жасау және техникалық күтім көрсету, жабдықтың күйін диагностикалау
Кез келген жабдықтың жұмыс сипаттамаларын белгілі бір көрсеткіштер арқылы шамамен бағалауға болатын процестің жүрумен сипаттауға болады. Сонымен білікті ұсатқыштың білігі айналуы жылдамдылығымен; араластырғыштың жұмыс істеуі кезінде пайда болатын шу, материалды құю дәрежесімен; элеватордың тіреуіштерінің қызуы температурамен сыпатталады. Әрбір мұндай параметрлер мәні келесі үш негізгі параметрлерге тәуелді болады: берілген жұмыс тәртібі, қоршаған ортаның күйі; машинаның өзіндік техникалық жағдайы.
Машинаның техникалық жағдайын анықтау барысында жұмыс тәртібі мен қоршаған ортаның күйі берілген және тұрақты деп қабылдау шарт. Мұндай ұйғарулар барысында жұмыс процесінің параметрлері тек қана машинаның техникалық жағдайына байланысты.
Кез келген түйіннің параметрі оның толық алғандағы жұмысын және де жеке элементтерімен байланысты анықтайды. Сонымен білік-тіреуіш қосылы үшін мұндай параметрлер, білік пен тіреуіштің жанасу беттері арасындағы саңылау мен сығылым шамасы, жанасу бет элементтерінің овалдығы мен олардың бірөстігі және т.б.
Кез келген жабдықтың жұмыс істеу процесінде, оның техникалық жағдайын сипаттаушы параметрі бастапқы бір мәннен мүмкін шектік мәнге дейін өзгеріп отырады. Техникалық жағдайының параметрлерінің өзгеру жылдамдығы бөлшектің тозуымен және де жұмысқа пайдалану факторларымен шартталады.
Машинаның техникалық күйінің шекті параметрлері, оның жұмыс кезіндегі істен шығаруының басталуы мен немесе жұмыс көрсеткіштерінің - өнімділігі , энергияны тұтыну дәрежесі, жұмыс қауіпсіздігі мүмкін болатындай шектен төмендеп кетпеуімен шартталады.
Осы себепті жабдықты диагностикалау үшін, ең алдымен машинаның істен шығуын анықтаушы параметрлерді қолдану қажет. Құрылғыларда структуралық параметрлерін тікелей өлшеу мүмкіндігі шектелген, сондықтан техникалық күйіне баға беру үшін жұмыс істеп тұрған машинада туындайтын жанама көрсеткіштерге көңіл бөлінеді.
Мұндай көрсеткіштерді диагностикалық белгілер деп атайды. Жабдықтарды диагностикалау үшін көрсеткіштердің диагностикалық белгісі ретінде тиімді жұмыс көрсеткіштерін, діріл мен шудың деңгейін, герметикалығын, түйіндері мен бөлшектерінің температурасын, өндірілуші өнім сапасын қолданады. Механизмнің диагностикалық белгілері мен структуралық параметрлері арасындағы орнатылған байланысқа сай оның техникалық күйін жеткілікті дәл анықтауға болады.
Диагностикалық нәтижесі бойынша қорытынды жасалынады және де бұл қорытынды мыналарды қарастырады:
· жарамсыздықты анықтау;
· техникалық қызмет көрсету немесе жөндеу жүргізудің қажеттілігі;
· жабдықтың қалдық ресурсы.
Жабдықтың жағдайын диагностикалаудың негізгі тәсілдері бұл – механика-технологиялық көрсеткіштер комплексі бойынша жұмыс тиімділігін бағалай; «бос» жүріс және жұмыс тәртібіндегі жұмысында энергияның нақты шығындарын анықтап табу; қозғалмалы қосылыстардағы саңылаудың мәнін анықтау; тіреуіштер температурасын және редуктордағы майлау майының қызу дәрежесін тексеру; жабдықтың акустикалық және дірілдік күйін анықтау.
Пайдалану құжаттары
Өндірістік цехтарда жүргізілетін жөндеу-техникалық құжаттар құрамына келесі құжаттар кіреді: жабдықты тапсыру-қабылаудың ауысымдық журналы; жабдықты жөндеуге және одан қабылдап алу-тапсыру журналы; орындалған жөндеулерді тіркеуші жөндеу журналы; ақаулар ведомосты; жылдам тозатын бөлшектер альбомы; машинаның жеке карточкасы. Бұл құжаттардың толық және дер кезінде толтырылуы, машиналар мен агрегаттардың жөнделу сапасы мен жеделдігін анықтайды.
Жабдықты тапсыру-қабылдау ауысымдық журналы – жабдық жұмысындағы жарамсыздықтар мен ақаулары тіркеуге арналған. Журналда тіркелу ай сайын жүргізіледі. Және де тіркелген жарамсыздықтарды кезекті Т.Қ.К немесе жөндеу барысында оларды қалпына келтіру бойынша нұсқаулар келтіреді. Журнал мәліметтерін техникалық қызмет көрсету және жөндеулер кезінде, ақау ведомостін түзу үшін қолданады.
Жабдықты жөндеуге тапсыру-қабылдау журналы – журналда жабдықтың атын, оның технологиялық сұлба бойынша позициялық номерін, жүргізілген жөндеудің қысқаша сипаттамасын, жөндеу алдын орындалған дайындау операцияларының мазмұнын көрсете отырып жабдықты жөндеуге тапсыру және одан қабылдап алу уақыты көрсетіледі. Жазбаларда технологиялық және жөндеу персоналдарының жауапты тұлғаларының қолы қойылады.
Орындалған жөндеулерді тіркеуші жөндеу журналы әрбір жабдық үшін арналады. Журналда келесі мәліметтерді көрсете отырып барлық жабдық үшін жүргізілген жөндеулер жайындағы мәліметтер келтіріледі: алдыңғы жүргізілген жөндеуден кейінгі істеген жұмыс уақыты; орындалған жөндеу түрі мен күні; орындалған жұмыстардың қысқаша сипаттамасы.
Ақаулар ведомосты – жоспарлы жөндеулер басталар алдында түзіледі. Және де бұл жөндеу жұмыстарының орындалу көлемін, қажетті материалдар мен қосалқы бөлшектер түрі мен санын, жөндеу жұмыстарының кестесін анықтау үшін негіз болып табылады. Онда машинаны жұмысқа пайдалану және оны тоқтатқан кездегі анықталған барлық ақаулар тіркеледі. Ақау ведомості жабдық жөндеуге қойылып, оны бөлшектегеннен соң қайта тексеріледі. Ведомоста ақау түрі және тозу сипаты көрсетіледі. Жабдық бөлшектері ведомостке құрастыру реттілігінде тіркеледі. Ақау ведомостін түзуге технологиялық персоналдар қарастырылады.
Ақау ведомостін түзу үшін, бұрын орындалған жөндеулер нәтижесінде түзілген типтік ведомостер кеңінен қолданылады. Мұндай ақау ведомосттарында бұрын кездескен ақаулардың түрлері және жөндеу кезінде орныдалатын жұмыс сипаттамалары келтіріледі. Типтік ақау ведомості механикалық қызметтің тәжрибелі және квалификацияланған қызметкерлерімен түзіледі.
Жылдам тозатын бөлшектер альбомы. Бұл альбомдар машинаны жасаушы зауытпен шығарылады да құрамында келесі құжаттарды қарастырады: түйіндерінің жалпы көрінісі мен бөлшектерінің сызбалары; мемлекеттік стандартталған бөлшектер кестесі; тез-тозатын, сонымен қатар сатылып алынатын бөлшектер тізімі. Сызбада әрбір бөлшектің өңделі түрі, жанасатын бөлшектердің өлшем шегі мен орнына отырғызылуы көрсетіледі.
Техникалық құжаттардың бақылау нормасы КҚБЖ (конструкторлық құжаттардың біркелкі жүйесі) және ӨОБЖ (өлшем шегі мен отырғызулардың біркелкі жүйесі) талаптарына сай орындалады.
Технологиялық жабдыққа көрсетілетін барлық жөндеуші техникалық қызмет көрсетулер түрін дайындау және жүргізудің техникалық шарты (ТШ), сондай-ақ оны жөндеуден қабылдау, жабдықты жөндеу орнында жасалып дайындалады. ТШ өнеркәсіптің бас инженері бекітеді.
Жөндеу жұмыстарын ұыймдастыру және басқару. ЖСЖ жүйесінің тағайындалуы мен мазмұны, жалпы қағидалары
ЖСЖ жүйесі деп, алдын ала түзілген кесте бойынша орындалатын , жабдықты жөндеу және оларға қызмет көрсетуге қажетті ұйымдастырылымдық – техникалық іс-шаралар комплексін айтамыз.
ЖСЖ жүйесінің негізгі мақсаты бұл – жабдықтың аппаттық істен шығуын алдын алу; өндіріс жоспарларымен келісілген мерзімде жөндеулерді жүргізу; жөндеуді жүргізу үшін алдын ала қосалқы бөлшектерді, материалдар мен жұмысшы күшін дайындау; жөндеу жұмыстарын дәйекті ұйымдастырудың арқасында жабдықтың жөндеуде тұру уақытын қысқарту.
Сонымен қатар жөндеулерді жоспарлы жүргізу барысында жөндеу персоналдарын уақыт бойынша біркелкі жүктеу, жөндеуге кеткен шығындарды және де басқа да кеткен шығындарды азайту мүмкіндігі пайда болады.
ЖСЖ жүйесі келесі жағдайларды қарастырады:
- кететін жабдықтың үнемді шығындарын және жөнделген бөлшектер мен түйіндердің ұзақ мерзімділігін қамтамасыз ететін, бөлшектің қалпына келтірілуінің қазіргі кездегі технологияларын қолдану негізінде жабдықты жөндеу, жөндеу арқылы қызмет көрсету және де профилактикалық тексеру;
- мекемені қосалқы бөлшектермен, түйіндермен қамтамасыз етуді және де олардың сақталуы мен есепке алуының ұйымдастыру;
- жөндеудің еңбек сыйымдылығын, жабдықтың жөндеуде тұру уақытын, жөндеу кезіндегі кететін материалдар мен бөлшектер шығынының, бөлшек қорының нормасының нормативтерін жасап дайындау;
- бөлшектер мен түйіндерге жұмысшы сызбаларды дайындау;
- жөндеу жұмыстарын механикаландыру құралдарын дұрыс қабылдау.
ЖСЖ бойынша іс-шараларды жалпы ұйымдастыру және жүргізу үшін жауапкершілік бас механикке жүктеледі.
Көмекші жабдықты жөндеу үшін тексеруден кейінгі жөндеу әдісін қолдануға болады. Бұл жөндеу әдісімен жөндеу кезекті жоспарлы тексеруден соң орындалады. Тексеруді орындау мерзімі, конструкциядағы бөлшектердің қызмет ету мерзімінің жобасымен анықталады. Бұл әдіс жабдықтың жөндеу аралық жұмыс уақытын ұлғайтады және де жөндеудің құнын төмендетуге мүмкіндік береді.
Жабдықты көмекші жабдықтар қатарына жатқызу оның толық алғандағы технологиялық жүйенің жұмысына әсер ету дәрежесіне байланысты болады. Яғни, машинанның немесе аппараттың істен шығуы технологиялық жүйе жұмысының тоқтауына мәжбүр етсе ол негізгі, ал егер істен шығу өз әсерін тигізбейтін болса онда ол қосымша (көмекші) жабдық болып саналады.
Жөндеулерді жүргізудің тәсілдері мен әдістері
Жөндеу жұмыстырын жүргізуге дайындалудың басты шарты бұл, жөндеудің тәсілдері мен технологиясын қабылдау. Жөндеу жұмысын жүргізудің негізгі тәсілдері бұл, орталықтандырылған, орталықтандырылмаған және аралас тәсіл.
Бірінші тәсілде жөндеу жұмыстары бір ортаға шоғырландырылған жөндеу базасында орындалады. Бұл кезде жөнделінуші жабдық жөндеу жұмыстарын орындайтын орталық жөндеу базасына жеткізіледі. Бұл әдісті кіші өлшемдегі аппараттар мен машиналар үшін қолдануға болады. Сол себепті жиі қолданылмайды, өйткені жөндеу базаларының жеткілікті дәрежеде жасақталуын және жабдықтардың резервтік қорының болуын талап етеді.
Жөндеудің орталықтандырылмаған әдісі барысында, оын жабдықты бөлшектемей-ақ цехтің арнайы жөндеуші персоналдарының көмегімен орындайды. Бұл әдістің кемшілігі сонда, жөндеу кезінде жабдықтың ұзақ уақыт жөндеуде тұру және де жөндеу жұмыстарының сапасының төмен болуы. Осыған орай әдісті конструкциясы күрделі емес машиналарды жөндеу үшін және жөндеу жұмыстарының көлемі аз жағдайларда қолданады.
Жөндеудің араласқан түрі кезінде, жабдықтың қалпына келтірілуі бойынша орындалатын операциялардың бірқатары орталықты жөндеу базасында және де бірқатары тікелей жабдық орнатылған цехтарда орындалады. Бұл әдісі бір шама кең таралған жөндеу әдісі болып табылады, себебі бұл кез нақты жағдайды ескере отырып жөндеудің икемді әдістерін қолдануға мүмкіндік береді.
Іс-тәжрибеде келесі жөндеу әдістерін қолданады: бөлшекті, түйінді, дәйекті – түйінді, агрегатты.
Бөлшекті жөндеу әдісінде, машинаның жөнделуге берілген бөлшектері мен түйіндерінің, ақауларын анықтаудың нәтижесінде бұрынғы күйіне сай қалпына келтіреді және де жаңа бөлшекпен алмастырады.
Қарастырылып оыртған әдістің елеулі кемшілігі бұл, жабдықтың жөндеуде ұзақ мерзімдет тұруы; жөндеудің жоғарғы өзіндік құндылығы; жұмысшылардың жоғары квалификациясының қажетті; бөлшекті дайындау мен қалпына келтірудің қазіргі таңдағы технологияларын қолданудың қиындығының пайда болуы. Әдіс көбінесе кәсіпорындағы аз мөлшердегі жабдықтар үшін қолданымды.
Түйінді әдіс, жөндеу қорындағы жаңа түйінмен жарамсыз түйінді алмастыруды қарастырады. Бөлшектенген түйін қалпына келтіріліп қоймада сақтауға жөнелтеді. Егерде кәсіпорында типтес жабдықтар саны көп болса, бұл әдіс кең қолданылады. Бұл жөндеу әдісі жабдықтың жөндеуде тұру уақытын елеулі қысқартуға мүмкіндік береді.
Дәйекті – түйінді әдіс, түйіндердің ауыстырылуы мен жөнделуін бір уақытта емес, қызмет ету мерзіміне байланысты тозу шамасы бойынша жүргізілуін қарастырады. Бұл кезде жөндеуді технологиялық үзіліс кезінде жүргізу тиімді. Әдісті конструктивті ерекше түйіні бар агрегат үшін қолдану лайықты болып табылады; мысалы үшін ленталы конвейрлер мен ін тәріздес элеваторлар және т.б.
Жөндеудің агрегатты әдісі, жөндеу кезінде істен шыққан агрегатты, осы маркадағы дайын агрегатыпен ауыстыруды қарастырады. Жөнделуге тиісті бөлшектелген агрегатты жөндеу үшін жөндеу кәсіпорнына (жөндеу механикалық цехына) жөнелтеді. Әдістің басты кемшілігі бұл, жабдықты қазіргі таңдағы тиімді жөндеу технологиясын қолдану және де жабдықтың модернизациялануын жүргізу мүмкіндігі. Сонымен қатар, жөндеудің құны төмендейді, ал оның сапасы артады.
Жөндеудің агрегатты әдісі жақсы жасақталған жөндеу базасы бар ірі мекемелерде, ұтымды түрде кіші габаритті жабдықтар үшін қолданылады. Бұл кезде жабдықты, жөндеу үшін орнына босатып алу және тасымалдау кезінде үлкен еңбек шығындарын талап етпеуге тиіс. Қазіргі таңда, бұл әдіс, өнеркәсібі жағынан дамыған – Жапония, Германия және т.б. елдерде кең қолдануда. Қазақстанда негізінен жөндеудің бөлшекті және түйінді әдістері қолданылады.
Жөндеулер түрі мен олардың мазмұны
Жоспарлы – сақтық жөндеу жүйесі келесі техникалық қызмет көрсетулер мен жөндеулер түрлерінің орындалуын қарастырады: жөндеу аралық қызмет көрсету; мезгілді профилактикалық тексерулер; ағымдағы жөндеу; орташа жөндеу; күрделі жөндеу.
Жөндеу аралық қызмет көрсету менмезгілді тексеруде орындалатын жұмыс мазмұны алдыңғы тарауларда қарастырылған.
Ағымдағы жөндеу барысында, келесі кезекті жөндеуге дейін жабдықты жұмыс қабілеттілік жағдайында ұстауға бағытталған жұмыс көлемі орындалады. Жөндеу жұмысының мазмұны, жеке бөлшектер мен түйіндерді (тез тозатын) қалпына келтіру немесе ауыстырудан, сондай-ақ оларды реттеп келтіруден тұрады. Жөндеудің бұл түрі жабдықтың орнатылған орнында өндірістік цехтардың жөндеу персоналдарының күшімен орындалады.
Ағымдағы жөндеу цех механигінің жетекшілігімен орындалады, ал цех механигі өз-кезінде жөндеу жұмыстарының уақытылы орындалуын және оынң сапасына жауап береді.
Орташа жөндеу. Орташа жөндеу процесінде тозған бөлшектері мен түйіндерін жөндеу немесе ауыстырудың көмегімен машинаның (агрегаттың) жұмысқа пайдалану сипаттамалары қалпына келтіріледі.
Мұнда міндетті түрде барлық бөлшектері мен түйіндерінің техникалық жағдайы тексеріліп, анықталған ақауларды қалпына келтіру бойынша іс-шаралар орындалады. Орындалатын жұмыс мазмұны машинаның конструциясына байланысты және де нақты жабдық үшін техникалық құжаттарға келтіріледі.
Орташа жөндеуді орындау барысында көбінесе орындалатын жалпы жұмыстар мыналар болып табылады:
- шекті тозу шамасы жеткен жеке бөлшектерін ауыстыра отырып, түйіндерді жөндеу;
- жарым-жарты бөлшектей отырып, машинаның барлық механизмдерін тексеру;
- тростарды, шынжырларды, тасымалдау лентасын, фрикциялық жапсырмаларды тексеру және тозған жағдайда оларды ауыстыру;
- тіреуіштерді жуу және тексеру, қызмет ету мерзімі анықталған жағдайда оны ауыстыру;
- редукторларды жуу, ревизия жасау және оын ретке келтіру;
- төсемдерді, тығыздағыштарды, бекіту бөлшектерін тексеру және тозған жағдайда оларды ауыстыру;
- қажет жағдайда жеке бөлшектер мен түйіндерді бояу;
- машинаны құрастыру, жеке түйіндері мен бөлшектерінің бекітілуін тексеру, ретке келтіру және де бос жүрісте, сондай-ақ күш түсіру арқылы тексеру.
Күрделі жөндеу. Жөндеудің бұл түрі кезінде машина толық бөлшектелініп, ақаулары анықталады, және де барлық тозған бөлшектерді ауыстыру жүреді (базалық бөлшегімен қоса). Мұнда барлық жанасатын бөлшектердің өлшем шегі мен отырғызылу шамасы, машинаға берілген техникалық шартпен анықталған мәнге келтіріледі. Сонымен қатар машина жұмысының техника-экономикалық көрсеткіштерін жақсарту мақсатында, оын жаңаландыру (модернизациялау) орындалады.
Күрделі жөндеу келесі жұмыстарды қарастырады:
- құраушы бөлшектерінің барлық өлшемдерін, сондай-ақ өлшем шегі мен отырғызылу шамасы техникалық құжаттармен анықталған мәнге келтіре отырып барлық түйіндер мен бөлшектерін ауыстыру;
- машинаның рамасы мен станинасын өлшеп тексеру, және де іргетасты (фундаментті) жөндеу;
- құбырларды және бөгетті-реттегіш арматураларды ревизия жасау және жөндеу;
- автоматты бақылау және басқару құралдарын игеру және реттеу, ал қажет жағдайда оларды ауыстыру;
- жеке бөліктерін немесе бүкіл машинаны бояу;
- бос жүрісте және күш түсіру тәртібінде байқау, комплексі тексеру және де реттеу.
Күрделі жөндеулер кезінде орындалатын жұмыстарға кәсіпорынның бас механигі басшылық етеді.
Жабдықты жаңаландыру бойынша іс-шаралар ЖСЖ жүйесімен қарастырылған жұмыстар құрамына кірмейді, бірақ оын әдетте күрделі жөндеу жүргізу кезінде қатар орындайды. Жабдықты жаңаландыруды орындау жайында шешім, оын орындаудың экономикалық тиімділігі мен техникалық мақсатқа сәйкестігі талдау негізінде қабылданады. Жабдықты жаңаландыруды кәсіпорынның конструкторлық бюросымен немесе арнайы жобалау-конструкторлық ұйымымен дайындалған техникалық құжаттар негізінде жүргізеді. Жаңаландыруды жүргізуге берілген техникалық құжаттар жабдықты дайындаушы-зауытпен келісіледі, содан соң ол кәсіпорынның бас механигімен бекітіледі. Жабдықты жаңаландыруға кәсіпорынның бас механигі жауапты.
Жөндеуді жоспарлау және басқару, негізгі түсініктер мен нормативтері
Жөндеулерді жоспарлау, жөндеудің көлемін, құнын және де жөндеудің барлық түрін орындау мерзімі мен техникалық қызмет көрсетулердің мерзімділігін анықтау мақсатында орындалады. Сонымен қатар, мұнда жөндеу персоналдар тізімін, оның профессионалдық және квалификациялық құрамын және де материалды-техникалық ресурстар мұқтаждығын анықтау қарастырылады.
Жөндеулерді жоспарлау барысында жөндеулердің сапасы мен орындалу мерзімдерінің, кәсіпорынның өндірістік техника-экономикалық көрсеткіштеріне әсерін талдау мүмкіндігі пайда болады.
Жөндеулерді жоспарлау келесі құжаттарды қолдана отырып жүзеге асырылады:
· анықталағн жөндеу нормативтерін;
· ыдыстар мен аппараттарды куәландыру мен сынаудың мерзімділік нормативтері;
· кәсіпорынның негізгі қорын жөндеудің титулді тізімі;
· сметалық – техникалық құжаттар;
· жабдықтарды жоспарлы-мерзімділік жөндеудің жылдық кестесі;
· жабдықты жөндеудің ай сайынғы жоспар-кест есебі;
· жөндеулердің күнтізбектік мерзімін анықтауға (өзгертуге) жасалынған акт;
Жабдықты жөндеудің жылдық және ай сайынғы жөндеулер кестесінің түрі, оларды ЭЕМ-де есептеу мүмкіндігін қарастыруы қажет:
· жөндеуге кететін уақыт шығындарын;
· жөндеуге кететін жұмыс күшінің шығындарын;
· қосалқы бөлшектер мен жөндеу аспаптарының қажетті мөлшерін;
· жөндеуге тұрған уақытта жабдықты жаңаландырудың орындалуын.
Қазіргі таңда өнеркәсіптің әрбір саласы үшін, «Жоспарлы-сақтық жөндеулер жүйесі жайында ережелер» дайындалған. Мұнда жөндеу бойынша құжаттар мазмұны мен оларды түзу түрлері келтірілген.
Жабдықтың тозуы. Тозу түрлері
Жабдықтың сеніді жұмысының төмендеуі, оның жұмысының негізгі көрсеткіштерінің нашарлауы физикалық моральді тозуымен түсіндіреді.
Физикалық тозуы ретінде түйіндер мен бөлшектердің пішінінің, өлшемдерінің, физико-механикалық қасиеттерінің өзгеруін түсінуге болады, және де бұл өзгерістерді органолептикалық әдістермен не болмаса өлшеулердің көмегімен анықтауға болады.
Жабдықтың моральдық тозуы оның сыртқы көрінісі мен технико-экономикалық көрсеткіштерінің заман талабына сәйкес келмеуінен жүреді. Жабдықтың моральдық тозуын анықтаудың біркелкі критериінің болмауын айта кеткеніміз жөн, сондықтан да бұл мәселе әрбір нақты жағдай үшін жеке шешіледі.
Физикалық тозу үшін шектік – мүмкін шама орнатылады да, оның сырт көзбен бағалауға және де шамасын құралдық әдіспен анықтауға болады. Көрсетілген нормадан асып кету, апаттың болу мүмкіндігінен жабдықты онан әрі эксплуатациялаудың мақсатқа сай еестігін көрсетеді.
Механикалық тозу біршама көп таралған тозу түрі және де ол бөлшектердің сынуы (шартты күйреу), беттік желіну (қажалу), деформациялану және үгетілу мен микрокүйреу байқалады.
Сыну. Бөлшектің толық сынуы немесе ондағы жарғыншақтың пайда болу мүмкін жүктемеден асып кеткен жүктеме әсерінің нәтижесінде орын алады.
Бөлшектің сынуы және осының салдарынан жабдықтың апатқа ұшырауын алдын алу үшін шекті жүктемелердің пайда болуын алдын алу іс-шараларын қолдану қажет. Сондықтан да технологиялық және де конструктивті сипаттағы іс-шараларды қолданады. Сонымен қатар, жауапты бөлшектерді жұмысқа пайдаланудың барлық кезеңдерінде үнемі тексеріп отыруымыз қажет.
Беттік тозу. Іс жүзінде жанасқан бөлшектердің беттерінің арасында әсерлесудің болмауы мүмкі емес. Олардың бір-біріне қарасты қозғалысы барысында механикалық тозу жүреді. Механикалық тозудың сипаты мен жылдамдығы көптеген факторларға тәуелді. Ең алдымен тозу интенсивтілігіне, жанасқан беттердің материалының тозу тұрақтылығы, меншікті жүктелулері, салыстырмалы қозғалу жылдамдығы және жүктелулері, салыстырмалы қозғалу жылдамдығы және бөлшектің жанасушы беттерінің адырлығы әсерін тигізеді. Беттік тозудың негізгі төрт түрін қарастыруға болады – қажалу, молекулалы механикалық тозу, жарақаттану және шаршаушы үгетілу.
Қажалу кинетикалық жұптардағы үйкелістердің нәтижесінде болып табылады. Үйкелісудің нәтижесінде пайда болған тозу, үйкелісу сияқты физикалық және механикалық сипаттағы аса күрделі процесс. Сондықтан да, бақыланып отырған құбылысқа түрлі түсініктер беріледі. Бұл процесс барысында құбылыстың жүру сипатына түсініктеме беру үшін жиі, молекулалық-механикалық теорияны қолданады. Екі бөлшектің бір-біріне қарағандағы қозғалысы олардың жанасушы беттерінің қажалуымен жүреді. Қажалу механизмін түсіндіру үшін осы процестің жүруін түсіндіруші бірқатар физикалық модельдер қолданылады.
Ұсынылып отырған модельдерге сай, бөлшектердің тозуының жылдамдығы материалының қаттылығы мен тұтқырлығына, әсерлесу беттерге түсетін меншікті қысымға, бет адырлығына және жылжуының салыстырмалы жылдамдығына байланысты болады. Үйкелісуші беттерде өте сапалы өңделу кезінде төбешіктер мен сайлар кездеседі. Осы себепті фазалардың әсерлесуі толық беті бойынша емес (нақты), тек қана төбешіктер жотасы бойынша жүреді, мұның ауданы нақты беттен ондаған және мыңдаған есе аз болады. Осыған орай олардың бетінде қысым ондаған және жүздеген мПа-ға дамиды. Беттердің салыстырмалы қозғалысы кезінде деформацияға ұшырайды. Ал елеусіз қысым әсерінде төбешіктер тек серпінді деформацияланады. Бұл кезде төбешіктер сығу күші бірнеше рет әсер еткеннен соң шаршаушы тозу салдарынан күйрей бастайды. Бұл процестер май қабаты болған кезде де жүреді. Егер де бөлшектің бірінің қаттылығы екіншісінен жоғары болса, онда бөлшек интенсивті жүреді.
Егер де тозудың басқа түрін болмайды деп жорамалдайтын болсақ, онда үйкелісуші беттердің бір-бірімен үйренісуінің нәтижесінде тозу тоқтайды.
Әрине, іс жүзінде олай болмайды. Өйткені тозудың екінші бір механизмі дами бастайды. Егерде жанасушы беттер арасында тозудың қатты өнімдері немесе басқа да қатты түйіршіктер пайда болған кезде бөлшектің жанасушы бетінде адырлық пайда болады да жоғарыда қаралған тозу механизмі қайталанады.
Беттік тозу шамасына әсер етуші болаттың негізгі параметрлреі, бұл оның қаттылығы мен тұтқырлығы. Қаттылық пен тозу тұрақтылық арасында сызықтық байланыс бар. Қаттылығы жоғары болған сайын тозу тұрақтылық жоғары.
Тұтқырлықтың жоғарылауы тозуды төмендетеді, себебі бұл кезде беттен болат түйіршіктерінің ажырауы қиындайды.
Сонымен қатар жазғылау мен соққылау тозу тұрақтылықты үлкейтеді, себебі өңдеуден соң болаттың беттік қабаты майда дәнді структураға ие болады да тығыздалады.
Жанасатын бөлшек материалдарын таңдап қабылдау кезінде келесі ережеге сүйену қажет: біршама күрделі және жауапты бөлшекті едәуір тозуға тұрақты материалдардан дайындайды, ал едәуір қарапайым бөлшекті аз қаттылығы мен елелусіз үйкелісу коэффициенті бар материалдардан дайындайды. Есте сақтауға тиістісі, бұл білік-подшипник типті жұпты дайындау үшін қолданатын біртекті материал, әртектіге қарағанда үлкен үйкелісу коэффициентіне ие болады.
Сонымен қатар бөлшектің тозу тұрақтылығына болаттағы қоспалар үлкен әсерін тигізеді. Болатты хром, молибден және басқа да компоненттердің, корбидттердіңтүзілуінің есебінен, жоғары микроқаттылықты қамтамасыз етеді, оның тозу тұрақтылығын бірнеше есеге арттырады.
Көміртекті құрамының өсуі болаттың тозу тұрақтылығын төмендетеді, ал ондағы марганецтің болуы оның тұтқырлығы мен тозу тозу тұрақтылығын жоғарылатады. Құрамында 11-13 пайызға дейін марганец бар, марганецтің болаттарды диірмендерді, ұғатқыштарды іштей футировкалау үшін қолданады.
Күкірттің құрамының мүмкін шамадан жоғары (0,02 – 0,03 пайыз) әсер етуі қоспаның үгетілуінің салдарынан болаттың қажалымдылығын жоғарылатады.
Өздігінде хром болаттың қаттылығын жоғарылатады. Хром 0,7 % жоғары қосу қажеттігі жоқ, себебі қаттылықтың шамадан тыс өсуі болады. Сондай-ақ молибден мен вольфрам да болаттың тозу тұрақтылығын жоғарылатады.
Шойындарда тозу тұрақтылық оншалықты жоғары емес. Біршама үлкен тозу фериттік шойында, ал аз тозу перлиттік шойындарда байқалады. Шойынның тозу тұрақтылығын жоғарылату үшін келесі элементтер қосады -1 – 2 % никельді және 0,4 – 0,5 % хромды.
Бос күйде болатын графит, шойынның қаттылығын азайтады, үйкелісу коэффициентін төмендетеді, осының салдарынан жалпы алғанда бөлшектің ұзақ мерзімділігі өседі.
Адырлық едәуір аз мәнге ие болатындай бетті өңдеудің жоғары сапасы кезінде, механикалық тозудың бірқатар түрлері орын алады.
Молекулярлық-механикалық тозу.Бұл тозу түрінің механизмін қаралған механикалық теорияны қолдана отырып ашу мүмкі емес. Ғалымдардың түрлі зерттеулері көрсеткендей, үйкелісу екі жақты меолекулярлы-механикалық табиғатқа ие болады. Бұл кездегі жүретін құбылыстың маңыздылығы келесіге келіп тіреледі. Бөлшек ішіндегі және де оның бетіндегі молекулалар бірдей күйде болмайды. Ағаш, қоршаған ортамен молекулалар өзара әсерлесе отырып тепетеңгеріледі. Беттегі молекулалар, бір жағынан бөлшек ішіндегі молекулалармен өзара әсерлеседі де, соның бетінде артық энергияға ие болады және де магнит өрісін түзеді.
Бұл кездегі жанасушы бөлшектер арасындағы қалыптасқан өзара тартылу күші орасан зор мнге жетеді. Болаттың микрокөлемінің суық пісірілісу жағдайда байқалады (майлау майы болмаған кезде). Техника тілінде бұл құбылысты ілігісу деп айтады. Мұндай тозу елеусіз салыстырмалды қозғалыс жылдамдығында, майлау майының жанасу аймағында болмағанда және де жоғары меншікті қысымында жүреді.
Ілігісу құбылысы әсерлесу нүктесінде, болаттың жұмсалуы мен пісірілісуі болатындай температураның жоғарылауымен байқалады. Болаттың жұқа қабатындағы температураның жоғарылауы түрлі механикалық қасиетегі болаттардың үйкелісуінде байқалады. Егерде бір бөлшек біршама қатты материалдан жасалса.
Жарақаттану. Жанасушы бөлшектің бірінің бетінен елеулі мөлшердегі болаттың сыдырылып әкетілуімен сипатталады. Жарақаттанудың нәтижесінде бөлшектің бірінің бетінде терең оршын қалыптасады. Бұл өз кезегінде интенсивті қажалуға себеп болып қызмет етеді.
Жарақаттанудың негізгі екі себебі болуы мүмкін – үйкелісуші беттердің жергілікті берік ілігісуі және де екі бөлшектіі әсерлесу аймағына ірі образивті түйіршіктің келіп түсуі. Бірдей материалдан жасалған жанасушы бөлшектерде жиі жарқаттанудың орын алуы байқалған.
Абразивті қажалу. Үйкелісуші беттерге шаң, құм және басқа да үлкен мөлшердегі майда түйіршіктердің келіп түсуімен жүреді. Көпшілік жағдайда бұл түйіршікте майлау майымен бірге қоршаған ортадан келіп түседі не болмаса жұмысқа пайдалану барысында қалыптасады. Егерде түйіршіктердің өлшемдері елелусіз болса олардың әсері елеусіз. Кері жағдайда бөлшектердің тозу тұрақтылғы бірдей болмауынан беттердің бірінің интенсивті тозу жүреді, немесе екі бөлшекте тозуға ұшырайды. Абразивті түйіршік қысымының әсерінен біршама жұмсақ бөлшекке енеді де онда ұсталып қалады, ал бұл кезде біршама жұмсақ болат қажалады.
Абразивті қажалу, майлау майының құрамында коррозияны тудырушы зат толған жағдайда үдете түседі. Әдетте, бұл кезде интенсивті тозу жоғары температурада жүреді.
Әсерлесуші шаршау тозуы. Бұл жағдайда бөлшектің күйреу процесі южоғары, циклді өзгеретін жүктеменің әсер етуімен жүреді.
Шаршау тозуына тән белгілер, бұл елеулі қадықты деформацияның болмауы және қиылу орнында тегіс беті бар жарғыншақтың болуы. Шаршаушы күйреу мүмкін кернеуге қарағанда аз кернеуылік жағдайда жүреді. Шаршау беріктігін төмендетуші негізгі себептер: бір диаметрден екінші диаметрге өтер жерде доғалдану радиусының болмауы. Келесі бір басты себептері, бұл беттің өңделуі және де кеуек, көпіршік түріндегі структурасының ақауы.
Тоғысу шаршау тозуы үйкелісу бетіне әсер ететін жүктеменің бағыты мен шамасының өзгеруімен сипатталушы бірнеше рет кернеуцлілік жағдайға ұшырауының нәтижесінде жүреді де, нәтижесінде жеке түйіршіктері ажырай бастайды. Мұндай тозу түрін шаршаушы ұғатылу деп атайды,
Ұғатылу, майлау майының үлкен мөлшері кезінде қарқынды жүреді, себебі майлау майы қысым әсерімен үйкелісу бетіндегі алғаш пайда болған жарғыншақтарға енеді де олардың әрі қарай дамуына ықпал етеді. Мұндай құбылысты, шамасы мен бағыты бойынша айнымалы жүктелуші үйкелісуші жұптар үшін майлау жүйесін жасап дайындау кезінде ескеру қажет. Тоғысу – шаршау тозуы шестреня тістері, тербелу және сырғанау подшипниктеріне тән құбылыс.
Жаншылу деформайциясы. Үлкен меншікті жүктемелердің ұзақ мерзімді әсері барысында үйкелісу беттері бірте-бірте жаншылуға ұшырайды. Үйкелісуші беттердің өңделуінің төмен сапасы кезінде нақты тоғысу беттерінде жүретін нақты меншікті қысым күшейеді. Мүмкін шектік мәніне жеткенде адырлық жоталарының шығып тұрған бөлігі жаншылады. Бұл тозу шамасын, өңдеу сапасын жоғарылата отырып, үйкелісуші беттерді алдын ала жұмыстың үйреністіре отырып және де жүктемелердің мүмкін шегін қатаң ұстай отырып төмендетуге болады.
Машинаның конструтивтік элементтерінің тозуы механикалық, жылулық және химиялық факторлардың әсерінің нәтижесі болып табылады. Ықпал ету факторына қарай тозуды механикалық, жылулық және коррозиялық деп түрлендіреді.
Механикалық тозу – табиғи процесс, және де бөлшектің геометриялық пішіні мен өлшемінің өзгеруі, деформацияға ұшырауы, тұтастығының бұзылуы, сондай-ақ беттік қабаттағы материалдың қасиетінің өзгеруі түрінде байқалады.
Механикалық тозу келесі факторларға тәуелді:
1) үйлесуші беттер материалдарының сапалары
2) үйлесуші беттердің өңдену тазалығына
3) үйлесу жұптарындағы жағармайдың болуы мен сапасы
Аталған факторлардың ықпалы заңды және де тозу жылдамдығына елеулі әсер етеді. Сонымен қатар механикалық тозу шамасына жанасу жұптарындағы динамикалық жүктемелердің де әсері зор. Яғни бағыты айнымалы жүктемелердің әсерінен металлда шаршаушы тозуға ұшырайды.
Үйкелісуші бөлшек материалдарының сапасы, үйкелісуші жұптардың тозутүзілділігін, жұмсақ деформациялануының қарқындылығы мен сипатын, сонымен қатар үйкелісу жылуының әсеріндегі болатын шаршауы түріндегі құбылыстың орын алуын анықтайды.
Жанасушы бөлшек беттерінің бет тазалықтары да үйкелісуші бөлшектер арасындағы нақты жанасу бетін анықтайды.
Өңделу бетінің сапасы конструктивті элементтің әсерге төзімділігі мен шаршау беріктігіне де әсер етеді.
Бөлшектің жұмсақ деформациялануы кинематикалық жұптағы меншікті жүктеменің, мүмкін шамадан артып кетуінің салдары болып табылады.
Механикалық тозу түрі болып табылатын, бөлшектің тұтастылығының бұзылуы келесі бірқатар себептердің салдары болып табылады:
1) мүмкін жүктемеден артып кету;
2) ескерусіз болған кернеудердің шоғырлануы
3) металлдың механикалық көрсеткіштерінің үлкен алшақтығы
4) дайындалу сапасы – термомеханикалық, пісіру және құрастыру операцияларының сапасы
5) майлау сапасы
механикалық тозудан басқа материалдың ескіруі де орын алады. Ескіру процесі, металдағы атомдардың диффузиялық араласуы, термоөңдеу барысында алынған структураның құлдырауы, және де химиялық құрамының өзгеруі түріндегі қат-қабат жүретін күрделі процесс.
Коррозиялық тозу
Коррозия деп, жұмысшы және қоршаған ортаның химмиялық немесе электрохимиялық әсер етуінің нәтижесіндегі бөлшек металлының күйреуі.
Химия, мұнайхимия және мұнайөңдеу өнеркәсібінің кәсіпорындарындағы технологиялық жабдықтарының істен шығуының басым себебі болып табылады.
Күйретуші әсерінің сипатына қарай коррозия тұтас және жергілікті (жеке дақ, жарғыншақ, саңылау) болуы мүмкін.
Технологиялық жабдықтардың істен шығуы коррозия түріне қарай келесідегідей үлеседі:
1) коррозияның шытынау – 35 %
2) саңылаулы коррозия – 20 %
3) тұтас коррозия – 18 %
4) кристалларалық коррозия – 16 %
5) коррозияның басқа түрлері – 11 %
Сонымен басмы коррозия түрі, бұл коррозиялық шытану. Бұл бір мезгілде әсер етуші келесі екі фактордың салдары болып табылады – ортаның агрессивтілігі мен металдағы қалдық керенулілік. Коррозияның бұл түрі кенеттен, алдын ала металдық структурасы мен қасиетінің өзгеруінсіз орын алады. Әдетте бұл, пісірмелі қосылыстарда, иілген орындарда, развальцовкаланған орындарда жүреді. Яғни коррозияның бұл түрі металдың кристалдық дәндерінің өсуі орын алған орындарда жүреді.
Саңылаулы коррозия – металлда өнбойына өткен саңылаудың орын алуымен сипатталады. Коррозиялық шытынау сынды, саңылаулық корозия ең алдыменен жоғары қысымда жұмысістейтін аппараттар үшін қауіпті. Саңылаулы коррозияны дер кезінде байқау үшін жабдық қаңқасының ішкі қорғау қабатында белгі бергіш саңылаулар ойылады. Бұл саңылауда коррозия қоздырғыштарының орын алуды коррозиялық күйреудің басталғандығын білдіреді.
Коррозиялық тозу түрі болып табылатын кристаларалық коррозия кристаллдар мен дәндердің шекарасында даму алады.
Бұл тозудың қауіптілігі, сырт көрінісі бойынша металл өзгермегеніменен, оның беріктіктік қасиеті күрт төмендейді. Коррозияның бұл түріменен күресудің бірден-бір жолы – болатты 1080-11500С қыздырып, кейіннен суда шынықтыру.
Атмосфералық коррозия қоршаған ортаның тотығу-тотықсыздану әсерінің салдары болып табылады. Коррозияның бұл түрі ашық аспан астында орнатылған конструкцияда басым. Корорзияның бұл түріменен күресудің басты әдістері – конструкцияны бояу және коррозияға қарсы металлдың қабат беру (тозаңдатып жапсарлауменен). Тозаңдатылып төселген қабат қалыңдығы 50-500 мкм болады.
Сонымен қатар орта әсерінен болатын жабдықтардың ішкі қуысының корорзиялық күйреуіменен күресу әдістерінің бірі, бұл әдістер жұмысаймағына ингибиторлар беру және де металды электрохимиялық қорғау.
Коррозия ингибиторлары бөлшек бетінде металл мен ортаның электрохимиялық әсерлесуіне кедергі болатын жұқа қабат немесе ерітіндіге түспейтін тұнба түзеді. Бұл қорғау әдісі болаттың корорзияға төзімділігін бірнеше есе арттырады. Және де өнімнің тұйықталған циркуляцияланудағы жүйесіне тиімді.
Электрохимиялық қорғау әдісі, металлконструкцияны тоқ көзінің оң (анотдық қорғау) немесе теріс (катодтық қорғау) полюске жалғауменен түсіндіріледі. Сонымен қатар іс-тәжірибеде протекторлық деп аталатын қорғау тәсілі де кеңінен қолданылады. Тәсіл қорғалуға тиісті аппарат қаңқасының металына қатысты теріспотенциялы бар металлменен жалғастыру арқылы жүреді. Протектор ретінде қалыңдығы 10-15 мм мырыш пластинасын қолданады. Протектор ауданы аппарат бетінің 3-5 % құрайды. Тізбекте протектор анод болып табылады да, қарқынды күйреуге ұшырайды, алосы анодтың процестер нәтижесінде аппарат қаңқасының күйреуі азаяды. Сонымен қатар протектор ретінде никельдік сырықтарды да қолданады.
Едәуір дәрежеде коррозияға келесі жабдық бөліктері бейім:
1) ортаның жоғары сызықтық жылдамдығы бар орындар
2) қалдық кернеуі бар орындар
3) тұрып қалу аймақтары
4) қызу жүретін аймақтар
5) үйкелісу орындары
Эрозиялық тозу
Эрозиялық тозу, әдетте құрамы қатты түйіршіктерден тұратын қозғалмалы ортаның әсерімен жүреді. Мұнда бөлшектерге қарасты қозғалушы қатты түйіршіктер, бетпен соқтығыса отырып оны қажап байқайды. Сонымен қатар эрозиялық тозу құрамында қатты түйіршіктері жоқ сұйық немесе будың толасы бетке ұзақ әсер етуі барысында да байқалады. Жоғарыдағы айтылғандарға анализ жасайтын болсақ, онда эрозиялық тозу үйкелісу мен соққының әсерінен болатындығына көз жеткізуге болады, эрозиялық тозу шамасы бөлшек беті мен ортаның физика – механикалық қасиетіне, тоғысу бетіне әсер етуші меншікті қысым мен соққы күшіне, ортаның және бөлшек бетінің салыстырмалы жылдамдығына, сондай-ақ түйіршіктердің өлшемі мен салмағына байланысты болады.
Бөлшек беті мен ағын толасының бір сәтте тоғысуы кезінде, бөлшектіі температурасының жылдам жоғарылауын тудыратын энергияның бөлінуі жүреді. Мұның салдарынан беттік қабат тек деформацияланып қоймайды, сонымен қатар елелулі структуралық және фазалық түрленуге ұшырайды. Эрозиялық тозу технологиялық құбырлардың сүйірлену жерлерінде. Газ немесе сұйық толсаның бағытының өзгеруі кезінде пайда болады.
Жылулық тозу
Химия және тамақ өнеркәсіптерінің көптеген жабдықтары жоғары температурада жұмыс істейді. Мұндай жағдайлардағы жабдық жұмысы конструктивті материалдардың релаксация, аққыштыққа, сондай-ақ оның структурасының өзгеруіне алып келуі мүмцкін. Аққыштыұ құбылысы конструктивтік элементтің қалыпты әсердегі жүктемелердің әсерінен баяу пластикалық деформациялануымен түсіндіріледі. Егер де бөлшектегі кернеу елеусіз болатын болса, онда деформация шамасының өсуі тежеледі. Үлкен жүктемелер барысында деформация, конструкция күйреуге ұшырағанға дейін өседі. Өздігінде материалдардың аққыштық шегі нақты материал үшін температуралық шекпен анықталады, онда көмертекті материал үшін бұл шама 3750С-ді құрайтын болса, ал қоспалық болаты үшін 4200С аспауы керек.
Релаксация ретінде, бөлшектегі кернеу оның деформациясының шамасы өзгеріссіз болғандығы өз бетінше түсінуге болады. Бұл кездегі жүретін процестің физикалық мағынасы сонда, жоғары температурада бастапқы кезеңдегі бөлшектегі пайда болған серпімді деформацияға үлеседі. Жиі релаксация үлкен кернеу әсеріндегі бөлшектерде байқалады. Осының салдарынан реликсация жабдықтың герметикалығының бұзылуына және апатқа ұшырауына алып келеді.
Шойындық, көміртектік болаттарда 5000С температурадан жоғары температурада графиттелу байқалады. Графиттелу барысында карбиттің күйреуі жүреді де еркін карбид түзіледі, мұның нәтижесінде болатын соққылы тұтқырлығы төмендейді. Бұл процесс пісіру жіктері мен бу құбырларында интенсивті жүреді.
5000С жоғары температурада ұзақ мерзімді жұмыс істеу соққылық тұтқырлықтың төмендеуіне алып келеді (жылулық морттық), бұл құбылыс өздігінде қатты қоспадан бірқатар компоненттердің майда дисперсиялық күйде бөлінуімен түсіндіріледі.
Коррозиялық тозу
Коррозиялық тозу – химиялық және тамақ өнеркәсіптері жабдықтарында кең таралған тозудың түрі. Коррозиялық тозуды төмендету немесе алдын алу жабдық жұмысының эксплуатациялық сенімділігі қамтамасыз етуге және оның жөнделуіне кететін шығындарды азайтуға мүмкіндік береді. Коррозия ретінде бөлшек бетінің химиялық және электрохимиялық процесстердің жүру нәтижесінде күйреуін түсінуге болады. Бұл процестің физикалық мағынасы, жүру жылдамдығы және нәтижесі болаттың қоршаған ортамен өзара әсерлесу сипатына байланысты.
Коррозияны болаттың бір қатар қышқылдарда ерітіндіге түсуімен жүретін процестерден айыра білген жөн. Бетте таралу сипатына байланысты – тұтас, жергілікті, кристал аралық және селективті коррозия. Барысында бөлшек беті біркелкі күйреуге ұшырайды. Біркелкілігі бойынша тұтас коррозия біркелкі тұтас және жергілікті тұтас болып түрленеді.
Қоршаған орта әсерінің нәтижесінде химия және тамақ өнеркәсібі жабдықтары тұтас коррозияға ұшырайды. Сондай-ақ мұндай коррозия түріне көпшілік жағдайда болат конструкциялар көп ұшырайды. Атмосфералық коррозиямен күресудің негізгі әдісі бұл, бояу және коррозияға қарсы төсем төсеу (коррозияға төтеп беруші темірлеу). өздігінде лак бояулы төсемнің қызмет ету мерзімі 3-4 жылдық құраса, ал тозаңдатылып келтірілген темірлік қабат 8-10 жылды қамтиды.
Жергілікті коррозия кезінде бөлшектің тек қана жеке учаскелері бүлінеді. Жергілікті коррозияның түрлері, бұл саңылаулы коррозия және де дақ түріндегі коррозия. Саңылаулы коррозия кезінде алдын ала кратерлер мен шықурлар қалыптасады, және де дами отырып өн бойына өткен саңылауға айналады. Саңылаулық коррозиялық тозуға ұшырауын байқау қиын. Осыған орай күйреуді дер кезінде анықтау үшін аппарат қаңқасында хабар беруші саңылаулар қарастырылған. Мұндағы коррозия өнімінің пайда болуы, қорғау қабатының күйреуін дәлелдейді.
Кристал аралық коррозия, болаттың дән шекарасы бойынша күйреуімен сипатталады. Коррозияның бұл түрі тамақ, химия және басқа да өнеркәсіп салаларында қолданылатын хром никельді болаттарға тән. Кристаларалық коррозияның механизмі келесідегідей – юолаттың дәндерінің шекарас ыбойынша 400-5000С температурада хром карбиді жойылады, және де бұл жерлерде хромның жетіспеуінің салдарынан коррозияға тұрақтылығы жойылады. Бірқатар жағдайларда дәндердің жалпы салмақтан ажырап қалуы байқалады. Бұл құбылыс пісіру аймағында болуы ықтимал.Коррозияның бұл түрі кезінде коррозия өнімдері болат ішінде орналасқан және де болаттың сырт көрніісі өзгремейді, ал оның беріктік қасиеті күрт төмендей бастайды.
Коррозияның бұл түріен күресудің екң таралған әдісінің бірі – бұл 1050 – 11500С температураға дейін қыздырып сонан соң оны шынықтыру.
Коррозиялық жарылу. Жарғыншақтардың қалыптасуымен жүреді де, бұл кезде негізгі терең орналасқан жарғыншақпен қатар микрожарғыншақтар торабы дами бастайды, мұндай жарақаттарды пісіріп бітеу жанындағы микрожарғыншақтардың жеке дара дамуына алып келеді. Коррозиялық жарылу себептері, - механикалық өңдеу. Нәтижесінде дән өлшемдерінің өсуі және де өңдеуден соң қалыптасқан созу кернеулерінің орын алуы. Корорзиялық жарылу пісірілмелі қосылыстарда, құбырларда, табақшаларда және де керілген түтіктерде байқалады. Жарылу болаттың қасиеттерін структурасын алдын ала өзгеруінсіз бірденнен жүреді. Көміртекті болаттардың корорзиялы әсерге тұрақтылығын жоғарылату үшін, оларды 6500С-да күйдірумен өңдейді. Тотықпайтын болаттардың коррозияға тұрақтылығын жоғарылату, оларды 650-8500С температурасында, ал бірқатар жағдайларда жоғары температурада суғармен қамтамасыз етіледі.
Машина бөлшектерін қалпына келтіру. Бөлшекті қалпына келтірудің технико-экономикалық тұжырымдамасы
Машина бөлшектерін қалпына келтіру, жөндеу процесінің тиімді экономикалық көрсеткіштері негізінде бөлшектерді қалпына келтірудің жоғары техникалық көрсеткіштерін қамтамасыз ететін тиімді жөндеу технологиясын таңдап қабылдауды талап етеді. Жөндеудің технологиясы ретінде бөлшектің жөнделуін белгілі бір операциялар реттілігімен орындаудың техникалық процесін түсінуге болады.
Бөлшектің қалпына келтірілуінің технологиялық процесін жасап дайындау барысында, ұқсас бөлшек конструкциясын жөндеу үшін іс-тәжірибеде қолданылып жүрген және де тиімді технико-экономикалық көрсеткіші бар қалпына келтіру әдістері негізге алынады. Тозған төлшекті қалпына келтірудің қажеттілігі туралы шешім экономикалық талдау негізігд қабылданды. Егер де қалпына келтірудің құны жаңа бөлшек құнынан төмен болдса, онда қалпына келтіру тәсілін таңдап қабылдау барысында бөлшектің тозу шамасын, оның көне...
Әдетте бөлшекті қалпына келтірудің құны дайындалған жаңа бөлшек құнының 10-25% құрайды, ал күрделі конфигурациядағы бөлшек үшін 5-10 %.
Бөлшектің конструктивтік ерекшелігін, әсер етуцші жүктемелер сипатын, сондай-ақ жөндеуден соң термиялық өңдеудің қажеттігін ескеру қажет. Бөлшекті қалпына келтірудің тәсілін қолдану жайындағы түпкілікті шешім жоғарыдағы айтылғандарды ескере отырып, нақты өндірістің техникалық мүмкіндігіненегізделіп қабылданады.
Сонымен қатар қабылданған қалпына келтіру әдісі, қалпына келтірілген бөлшектің мехнаникалық және техникалық сипаттамаларының жеткілікті техникалық ресурсын мүмкіндігінше толық қамтамасыз етуге қажет. Бөлшектіі талап етілген әдісін таңдап қабылдау кезінде тек қалпына келтіру құны ғана негізге алынбайды, сонымен қатар қалпына келтірілу сапасы жанасушы бөлшектердің тозу жылдамдығына әсер етуі де ескерілуі тиіс.
Бөлшекті қалпына келтірілудің қолайлы тәсілін таңдп қабылдау критериі, бұл оның тиімділік көрсеткіші Э:
Э= C/Т*О
Мұндағы: Т- бөлшектің жөндеуден кейінгі қызмет ету мерзімі;
С – жөндеуге кеткен шығындарҒ О – бөлшекті қалпына келтіру барысындағы орындалатын операциялар саны.
Қазіргі кезде бөлшекті қалпына келтіру үшін пісіру, балқыма қабат төсеу, болат қабатын электролиттік өсіру, жөндеу өлшеміне дейін өңдеу, қосымша бөлшектер әдісі, сондай-ақ пластикалық деформацилау әдістері кеңінен қолданылады.
Пісіру
Көміртекті және қоспалы болаттарды пісіру.Пісрісу бөлшектің бүтіділігін қалпына келтірудің біршама кең тараған әдісі болып табылады. Жөндеу жұмыстарын жүргізу кезінде келесі пісіру түрлері біршама жиі қолданылады: Электр доғалы пісіру – қолмен атқарылатын, жартылай автоматты және автоматты, қорғау газдарының ортасында электршлакты. Құбырларды пісіру үшінацетилендіоттекті пісіру кеңінен қолданылады.
Бөлшекті пісіру мен қалпына келтіруді бөлшектің бүтінділігінің бұзылуы – жарықтың өнбойына өткен саңылаудың және бөлшектің сынуының пайда болуы кезінде қолданылады.
ЖЖөндеу жұмыстары кезінде қолмен атқарылатын электрдоғалы пісіру кеңінен қолданылады, себебі ол жұмысты жіктің кез келген орналасуында және кез келген жағдайда қолданылады. Сонымен қатар бұл пісіру түрінің кең түрде қолданылуы пісіруші жабдығының кең таралуы мен төмен құндылығы.
Жабдықты жөндеу механикалық цехында жөндеу кезінде пісірудің едәуір өнімді әдісі – флюс қабаты астында автоматты және жартылай автоматты, инертті газ ортасында пісіру қолданылады. Нақты пісіру әдісін таңдап қабылдау бөлшектің физико-механикалық ұасиетіне, пісіру жігінің сапасына қойылатын талаптарға және жөндеуді жүргізу жағдайына байланысты болады.
Пісіруді тұрақты және айнымалы тоқты қолдана отырып жүргізеді. Тұрақты токпен пісіру барысында жоғарғы сапалы жік қалыптасады, бірақ бұл кезде жоғары құнды және күрделі жабдықтың қолданылуы процесті біршама күрделендіреді.
Тұрақты токпен пісіруді тура және кері полярлықта жүргізеді. Пісірудің бірнеше тәсілінде тұрақты тоқ генераторының оң клеммасын бөлшекке жалғайды, ал сол клемманы пісіруэлектродына қосады, ал пісірудің кері полярлығнда клеммалар керісінше қосылады. Оң электродта, сол электродқа қарағанда үлкен жылу бөлінеді. Сондықтан да пісіру процесін оң және кері полярлықтағы тоқты қолдана отырып реттеуге болады. Сонымен қатар полярлылықтың қабылдануы бөлшек салмағы мен конструктивті өлшемдеріне байланысты, мысалы, массивті бөлшектерді оң полярлық тоқпен пісіру кезінде бөлшек жақсы қызады, және де болаттың балқы тереңдігі көбейеді. Ал жұқа қабықты болаттарды пісру үшін оларды кері полярлық тоққа жалғайды, бұл жағдай бөлшекті қатты қызып кетуден және пісіру жігінің күюінен сақтайды.
Пісірудің технологиялық процесін жасап-дайындаудағы басты кезең бұл, пісіру электродын таңдау болып табылады. Электродты таңдау барысында пісірілуші бөлшектің конструктивті материалы ескеріледі.
Көміртекті болатты қолмен электрдоғалы пісіру кезінде балқитын болат электродтар қолданылады. Мұндай электродтардың сипаттамалары 5.1 кестесінде берілген.
5.1 кесте
Электродтың типі |
Үзілуге уақытша кедергісі, мПа |
Салыстырмалы ұзаруы % |
Соққылық тұтқырлығы, кДж/м3 |
Э-38 |
380 |
- |
- |
Э-42 |
420 |
18 |
784 |
Э-42А |
420 |
22 |
1372 |
Э-46 |
460 |
18 |
784 |
Э-46А |
460 |
22 |
1372 |
Э-50 |
500 |
16 |
588 |
Э-50А |
500 |
20 |
1274 |
Электродтың диаметрі пісіруші қырдың қалыңдығына, пісіру қосылыстарының түріне және де жіктің өлшеміне байланысты қабылданады.
Пісірілу қырының қалыңдығына байланысты түйістірмелі жік үшін келесі диаметрдегі электродтарды қолданады:
5.2 кесте
Пісірілуші қырдың қалыңдығы, мм |
2-дейін |
3:5 |
6:8 |
9:12 |
13:15 |
Электродтың диаметрі, мм |
2 |
3:4 |
4:5 |
5:6 |
6:7 |
Түйістірмелі қосылыстағы жіктерді көп жүрісті пісіру кезінде алғашқы жүрісі, әдетте, диматері 4 мм-ден көп болмайтындай электрод көмегімен орындалады. Бұл жасақ түбіндегі жік діңгеін жақсы пісіру үшін қажет. Бұрыштық және жіктер үшін жік катетіне зең қою қажет. Жік катеті 3:5 мм болған кезде пісіруді диматері 3+4 мм электродпен орындайды, ал жік катеті 6-8 мм болғанда диаметрі 4-5 мм электродты қолданады.
Электродтың әрбір диаметріне пісіру тогының белгілі бір арақашықтығы сәйкес келеді. Ток күшінің шамасын келесі өрнектен анықтауға болады.
І=(β + αdэл) dэл
Мұндағы β және α – тұрақты коэфициентер (β=20 және α=6) dэл – электродтың диаметрі, мм. Болат қалыңдығы 3 dэл көп болған жағдайда тек күшін 10-25 пайызға ұлғайту қажет, ал, 1,5 dэл аз қалыңдықта 10-15 пайыз азайтады.
1*13 және 2*13 хромды болатынан жасалған конструкцияны қалпына келтіру бірқатар қиындықтар тудырады. Бұл жағдай өздігінде хром 600:9000С температурада көміртекпен жеңіл қосылысқа түсетіндігімн түсіндірілеі. Сондай-ақ хромды болаттарды ауада суыту барысында өздігінше шынығуға бейімдейді. өздігінен шынығудың нәтижесінде пісірілу жігі мен жік аймағының болаты үлкен қаттылық пен морттылық қалыпқа ие болады. Және де хромның күшті тотығуы қиын балқығыш тоттардың түзілуіне әкеліп соғады, ал бұл өз кезегінде пісірілу жігінің сапасын төмендетеді.
Құрамында 0,2 % дейін көміртегі және 12:14 % дейінгі хромы бар хромды болаттар, аустениттік класқа жатады.
Мұндай болаттарды пісіру алдын 200:3000С температураға дейін қыздырып, пісіруден соң термиялық өңдеу қажет.
Электрдоғалы пісіруді аз ток кезінде кері полярлықтағы тұрақты тоқта жүргізеді. Мұнда ток күшін электрод диаметрінің әрбір 1 мм-не 25:30 А болатындай етіп қабылдайды.
Пісіруді Э-55, Э-60, Э-70 типтегі электродтардың көмегімен жүргізеді.
Хромды болаттарды газды пісіруді бөлшек қалыңдығы 1:3 мм болған кезе орындайды. Елеусіз ацетиленнің қатынасы бар ацетилендіоттекті қоспаны қолданады. Пісіруді 50% бурадан және 50% бор қышқылынан тұратын флюсті қолдана отырып, бір жүрісте орындайды. Присадалық материалы ретінде (Св 10ХМ, Св 10Х5М, Св 08Х3ГСМ) қоспалы болатарынан немесе (Св 6Х14, Св10Х13) жоғары қоспалы болаттардан дайындалған сымды қолданады.
ОХ18Н9 және 1Х18Н9 хромни келді қосылыстарды пісіруден алдын 850:10000 С температураға дейін қыздырып суда жылда суытудың көмегімен термиялық өңдеуге береді, егер де пісіруші болат аз қалыңдықта болса, онда оны ауамен суытады.
Термиялық өңдеу болаттың механикалық қасиетін жаңартады және де кристаларалық коррозияға тұрақтылығын жоғарылатыд.
1Х18Н9Т және 1Х18Н115 хромникельді болаттар өз құрамында титан және ниоби сияқты элементтерді қарастырады, бұл элементтер хромға қарағанда күшті карбид түзгіштер болып табылады. Көмітекпен реакцияға алдын түсе отырып хром карбидінің түзілуіне жол бермейді. Бұл кезде пісіруден соң термиялық өңдеуді жүргізудің қажеті жоқ.
Газды пісіру 2мм-ге дейінгі қалыңдықтағы бұйымдар үшін, құрамында 57 % суссыз бурасы, 32,6 % кремни балшығы; 0,15 % ферромарганеці бар флюсті қолданумен жүреді. Флюсті түйіспенің қарама-қарсы бетіне шағылады. Пісірілмелі қосылыстар негізгі болат пен салыстырғанда кристаларалық коррозияға біршам аз тұрақтылыққа ие болады.
Х18Н9 және Х18Н9Т болатты доғалы пісіру кері полярлықтағы тұрақты тоқта орындауқажет. Материалдың қызып кетуін төмендету үшін пісіру тоғын салыстырмалы аз шамада қолданады. Соынмен қатар, пісіру аймағынан жылуды әкету бойынша қосымша шаралар қолдану қажеттігі туады, мысалы, мысты төсемді қолдана отырып ЦЛ-2 немесе ЦЛ-4 төсемі бар Св08ХМА немесе СвХ19Н9Т болаттарынан жасалған электродтарды қолданамыз. Қосалқы болаттарды пісіру барысында біршама сапалы жік аргонды доғалы қолданумен қалыптасады. Бщұл жағдайда электродтың төсемінің құрамына кіретін көміртегінің есебінен пісірілу жігінің көміртегімен нығайтылуы жүреді, бұл болаттың кристаларалық коррозияға тұрақтылығын жоғарылатады.
Шойыннан жасалған бұйымдарды пісіру
Шойынды пісіру барысында келесі бір қытыр қиындықтар туады, мұндай қиындықтардың орын алуы бір жағынан ондағы көміртегі мен кремнидің жоғары құрамы болса, екіншіден – шойынның төмен жұмсақтығы мен ыстыққа сезімталдығымен түсіндіріледі. Қарастырылып отырған ерекшеліктердің нәтижесінде пісіру жігінде келесі ақаулар орын алады.
- Графит дәндерінің цементке жергілікті түрленуі, мұның салдарынан ақ шойын структурасы қалыптасады. Бұл пісіру аймағындағы хромнидің күйіп кетушінің нәтижесінде жүреді. Сондай-ақ шойынды жылдам суыту ақ шойынды участкелердің орын алуына әкеледі.
- Пісіруден соң бөлшекті суыту кезінде, жіктің біркелкі отырмауының салдарынан, жік аймағында жарғыншақтың қалыптасуын тудырады.
- Төмен балқу температурасы мен қатты күйден сұйық күйге жылдам өтуі, болатттан газдардың бөлінуін толық қамтамасыз етпейді. Осы себепті жік кеуекті болып қалыптасады.
- Балқу ваннасының бетінде марганец пен кремнидің қиын балқитын тотықтарының қалыптасуы.
Шойын балқымасының суық аққыш болуының салдарынан, оларды тек жіктің көлбеу орналасу жағдайында пісірген жөн. Шойынның барлық түрінің ішінде біршама жақсы пісірілетіні, бұл сұр шойын. Үлкен графитті бар шойындар нашар суытылады.
Шойынды газ және электрдоғалы пісірудің көмегімен пісіруге болады. Шойынды газды пісіруді қаыпты немесе көміртегімен нығайтушы жалынмен орындайды. Бұл кезде флюсті және көмірқышқыл натриді қолданады, сапалы жіктің қалыптасуына бейімдеуші.
Пісіру кезінде қызғылт түске дейін қыздырылған присадкалы сым ұшын мезгілді алмастыра отырып флюске және болат балқымасына батырып тұрады. Сондай-ақ флюсті пісір ваннасына батырып тұрады. Шойынды газды пісіруді алдын ала жергілікті немесе жалпы қыздырумн орындайды.
Жергілікті қыздыруды пісіру горелкасының (оттығының) көмегімен ішкі кернеулеп пайда болатын және де пісіру жігіне тікелей жалғасып жатқан орындарда жүргізіледі.
Қыздыру балқыған болаттың суытылу жылдамдығын тежейді және ақ шойынның түзілуін болдырмайды, сондай-ақ шойынның едәуір толық дәрежеде графиттелуіне бейімдейді. Присадкалы материалдар ретінде А немесе Б маркалы шойын сымдарын қолданады.
Шойынннан жасалған жауапты бөлшектерді және де күрделі конфигурациядағы бөлшектерді пісіру кезінде оларды алдын ала 600-7000С температураға дейін ошақтарда, термостарда немесе горналарда қыздырады, себебі шойынның оқ шойыға айналуын және де шынығуын алдын алу үшін бөлшекті 6000 С температурадан төмен температурада қыздыру кезінде қатаюшы пісіру ваннасы мен негізгі болат арасындағы үлкен температуралар айырмасының себебінен шойынның ақшойынға айналуын алдын алу мүмкіндігі болмайды. Ал бөлшектің қыздырылу температурасын 7500С температурадан асырып жіберу шойын дәндерінің елеулі өсіп кетуіне әкеліп соғады.
Шойын қиын балқитын дәнекерлеуіш пен дәнекерлеуге жақсы беріледі. Сондықтан да жарғыншақтар мен сынықтарды жөндеу үшін Л62, ЛОК 62-06-04, ЛК 62-05 маркалы латундық дәнекерлеуіштерді кеңінен қолданады. Латунның балқу температурасы 850-9500С аралығында жатады, яғни шойынның балқу температурасынан елеулі төмен. Осыған орай дәнекерлеу кезінде бөлшек қырлары балқымайды, тек қана 900-9500С температураға дейін қыздырылады, сонан соң балқытылған дәнекерлегіш жатады.
Дәнекерлеу процесінде балқыған латун тек қана күйген графиттен болған тегіссіздіктер мен ойпаттарды толтырып қоймайды, сонымен қатар шойын дәндерінің арасына енеді, бұл латунның шойынмен берік байланыс түзуін қамтамасыз етеді. Сондай-ақ қосылыс беріктігінің қаматамасыз етілуі белгілі бір шамада темір, цинктің және мыстың қалыптасуымен түсіндіріледі. Дәнекерленген болатының беріктік шегі 8-15 пайыз салыстырмалы ұзару кезінде 350-400 мПА жетеді. Бұл әдіс кезінде ауыспалы қабат негізгі және балқыған беріктігін жақсарту үшін ауыспалы аймақтағы көлденең қиманың ауданын ұлғайтамыз.
Шойыннан жасалған бөлшектердің қолмен атқарылатын доғаны пісірілуін ладын ала қыздырумен немесе онысыз балқымалы пісіру жік аймағындағы ақшойындық және де шынықтырылған участкелердің қалыптасуын, сондай-ақ жік аймағы мен жіктің өзіндегі жарғаншақтың қалыптасуын алдын алудың ыңғайлы тәсілі болып табылады. Пісіруді ОМ4-1 электродын қолдана отырып кері полярлықтағы тұрақ токта жүргізеді.
ОМ4-1 электродынан басқа пісіру үшін, сондай-ақ графиттеуші қабат жағылған А немесе Б маркалы шойыннан құйылған сымдарды қолдануғ болады.
Пісіру тәртібі мен шойын сымының диаметрін пісірілуші бөлшектің қабырғасының қалыңдығына байланысты таңдап қабылдаймыз:
Пісірілуші бөлшектің қабырға S<10 S=10-5 S=15-30
Қалыңдығы мм
Шойын сымының диаметрі мм. 4 6 8
Ток күші, А 170-180 270-280 300-350
Пісіру процесінде қалыптасушы шлактың балқу температурасын төмендету үшін, пісіруден алдын қырға жағылатын, бурадан немесе 50 пайыз бурадан және 520 пайыз екікөмір қышқылды натриден тұратын флюсті қолданамыз.
Егерде бөлшекті пісіру үшін жалпы қыздырудың мүмкіндігі болмаған жағдайда, оны 600-7000С температураға дейін пісіру аймағын жергілікті қыздырумен шектелуге болады.
Суық доғалы пісуді жөндеулер кезінде кең таралуына байланысты жиі қолданады. Бұл әдістің кемшілігі анағұрлым жылдам суытылуына байланысты пісірілу жігінде ақ шойынның пайда болуы. Сонымен қатар бұл кезде жік айфмаындағы шойынның беріктік шегінің жоғарылауының себебінен жарғыншақтардың қалыптасуы орын алады.
Аталған кемшіліктерді алдын алу үшін қолданылушы технологиялық шаралар бұл, пісіру аймағындағы болаттың қызып кетуін алдын алу, жіктің жатуы барысында қалыптасатын кернеулік жағдайды төмендету, және де болатқа шойынның графиттелуін бейімдеуші элементтерді қосу.
Шойынды суық пісіру барысында шойындық, немесе болат электродтарды, сондай-ақ мыстан, оның қоспаларынан және үйлестіріліп жасалған электродтарды қолданады.
Мсыла ыүшін қыздырусыз пісіру барысында құрамында жоғары дәрежедегі көміртегі мен кремний бар электродтарды қолданады. Мұндағы көміртектің жоғарғы дәрежесі оның пісірілу кезіндегі күйген мөлшерін толықтау үшін. Іс-тәжірибеде жабдықты жөндеу барысында көпшілік жағдайда суық пісіру үшін шойын сымдарын қолданады. Бұл кезде пісіру доға ұзындығы 4-5 мм болатын айнымалы немесе тұрақты тоқта жүргізеді.
Графиттелу жағдайын жақсарту үшін және балқыған болаттың суытылу жылдамдығын баяулату үшін пісіруді электродтыілгері-кейінді қозғалта отырып орындайды.
Шойынды электродпен суық пісіру барысында балқыған болаттың графиттелуі толығынан жүрмейді.
Псіірілмелі қосылысқа тек жеткілікті механикалық беріктік талабы қойылған кезде, болат электродтардың қолдануға болады.
Шойынды болат электродтармен пісіру кезінде электродтық болаттың балқыған щойынмен араласуының нәтижесінде құрамында жоғарғы дәрежедегі көміртегі бар қоспа түзіледі, ал бұл өз кезінде кристолизациялық және де суық жарғыншақтың қалыптасуына әсер етеді.
Бұл кезде кернеуді төмендету үшін, күйдіруші валиктерді төсеу және беріктеуші штифтер мен скобаларды орнату әдістері қолданылады.
Алдын ала қыздырусыз шойынды пісіру кезінде шеті мыстан және оның қоспаларынан жасалған электродтарды қолданады. Темір мен мыстың өзара нашар ерітіндіге түсуінің есебінен тікелей пісірілу жүрмейді, мұндағы механикалық беріктік ең алдымен темір мен мыс түйіршіктерінің бір-біріне енуінің есебінен механикалық ілігісуінің арқасында қамтамасыз етіледі. Доғаның жану тұрақтылығын жақсарту үшін мыс электродтарға графит кен ферросилицидің теңдей бөлігінен тұратын шақпасы төселеді.
Бұл блалқу шекарасында ақшойынның қалыптасуын азайтады, сол себепті жік жеткілікті тығыз және төмен қаттылықпен қалыптасады, бірақ мұндай жіктің беріктігі үлкен емес.
Жарғыншақтар мен соқылауларды пісірп жөндеу үшін үйлестірілген электродтарды қолданады.
Үйлестірілген электродтардың көмегімен пісіруді, бөлшектің уақытша шамадан тыс қызып кетуін болдырмау үшін, тік ұзындығы бойынша теңдей орналастырылған қысқаша участкелермен жүргізеді. Темірмысты электродтардың негізгі артықшылығы сонда, бұл кезде шатыстырылу кернеуі төмендейді және де жік аймағындағы кеңістікте жарғыншақтың пайда болу қауіпі азаяды.
Мұндай электродтардың негізгі кемшілігі, структураның біртекті болмауы және балқыған материалдың жоғарғы дәрежедегі қаттылығы.
Алюминиді пісіру
Алюминидің пісірілуі оның бетінде жұқа (2 мкм дейін), қиын балқитын (20500С) алюминий тотығының қабығы қалыптасуымен күрделенеді. Осы қабықтың жойылуынсыз пісіруді жүргізу мүмкін ретінде литидің, калидің, натридің және кальцийдің фторлық немесе фромдық тұздары қолданылады.
Өздігінде алюминий электрдоғалы және газды пісірумен пісіріледі. Алюминиді газды пісіру нетралды жалынмен немесе елеусіз артық шығындағы ацетиллені бар жалынмен жүргізеді. Жаттықтыру материалы ретінде СвА97, СвАМц, СвАК5 және басқа да маркалы сымдарды қолданады. Пісіру алдын пісіруші бөлшекті 200-2500С температураға дейін қыздырады. Пісіруден соң ішкі кернеуден босату үшін және майда дәнді жік алу үшін термиялық өңдеуді жүргіземіз (екі сағаттық ұстаумен 300-3500С температурада күйдіру және баяу суыту)
Алюминий – кремнилік қоспаны флюссіз пісіруге болады, ал тотықтық қабықты механикалық тәсілмен жояды.Алюминиден жасалған конструкцияны доғалы пісіру барысында пісірілуші қырлардың тазалығы негізгі мағынаға ие болады. Сол себепті пісірер алдын болат мұқият тотықтық қабаттан тазартылады. 15-20 мм ендегі түпкілікті қырларды тазалауды тікелей пісірер алдын тотықпайтын болаттан дайындалған шеканың көмегімен орындайды. Осылайша тазартылған қырлар 5-6 сағат ішінде пісіруге жарамды. Нұсқалған мерзім аяқталғаннан соң қырлар қайта тазартылады.
Пісіруге тазартудың ең тиімді әдіс химиялық тазалау әдісі. Қырларды майсыздандыру үшін пісірілу қырлары сілтілердің әлсіз ертінділеріне батырылады, бұл ерітінді қолданылар алдын 60:700С температураға дейін қыздырылады. Пісіру кезінде қолданылушы әдістердің бірі бұл, бөлшекті артофосфат қышқылының судағы ерітіндісі (300 Т/л) мен хромликте (0,1:1 г/л) судағы ерітіндісінің 20-300С температурада беттік қабатты тазарту . Өңдеу уақыты бұл кезде 15-20 минутты құрайды. Беттік тазартудан соң бөлшекті таза суда жуып ыстық ауамен кептіреді.
Химиялық тәсілмен пісіруге дайындалған бет, пісіруге 24-36 сағат аралығында жарамды.
Электрдоғалы пісіруді балқымайтын электрод көмегімен және балқитын болат электродпен жүргізуге болады. Бірінші жағдайда, сапалы жік алу үшін флюсті қолданады. Флюстің шамасын пісірілу жігінің сыртқы көрінісі бойынша анықтаймыз.
Жіктің тегіс және жылтыр беті, қара дақсыз және кеуексіз, флюстің жетіспеуі немесе артық шамасы кеуектердің орын алуына әкеліп соғады.
Балқитын болат электродты қолданумен жүретін доғалы пісіруді 5 мм кем болмайтындай қалыңдығы бар үлкен бөлшектерді қосу үшін қолданылады.
Пісіру кезінде 03А-1, 03А-2 типті жақпасы бар электродты қолданады. Электродты қатаң түрде жікке перпендикуляр ұстау қажет, оның көлденең тербетілуі рұқсат етілмейді. Бұл кезде элекрод қозғалысы біркелкі, ал доғаның ұзындығы минимал болуы тиіс.
Алдын ала қыздыруды болат қалыңдығы 6 мм және оның жоғары болғанда қолданады. Қажет қыздыру температурасы 100-4000С.
Бөлшекті электролиттік қалпына келтіру
Бөлшек бетінде электролиттік металл қабатын өсіру немесе жапсарлауға балқымаларды тұндыру, хромдау, темірлеу, никелдеу, мыстау, мырыштау және т.б. әдістер жатады. Жиі жөндеу тәжірибесінде хромдау мен темірлеуді қолданады. Бұл кезде алынатын төсем қалыңдығы – хромдауда 0,2 – 0,3 мм, ал темірлеуде – 2-3мм-ге дейін жетеді. Бұл жағдай темірдің хромға қарағандағы тұну жылдамдығы 10-20 есе үлкендігіменен түсіндіріледі.
Электролиттік хромдау барысында атқылығы мен тозу төзімділігі жоғары және де корорзияға қарсы қасиетті қабат ал үшін қолданады. Темірлеу барысында алынатын төсем қаттылығы хромға қарағанда төмен болғаныменен, өзіндік физико-механикалық қасиеттері бойынша орташакөміртекті болаттарға сай келеді. Темірлеуді қалпына келтіру әдісіретінде де, сондай-ақ хромдық қабатқа астар қабат келтіру ретінде де қолданады. Темірлеу барысында сапалы тұнба қалыңдығы 1,5 мм-ге дейінгі жағдайда қамтамасыз етіледі. Соныдықтан да едәуір қалың қабат алу үшін цикл толығымен бірнеше рет қайталанады.
Жөндеу шаруашылығында қалпына келтіруші бөлшектің конструктивті ерекшелігіне конструктивті материалына, пайдалану жағдайына және қажетті қабат қалыңдығына қарай электролиттік қабат төсеуде келесі электролиттер қолданылады:
-электролиттік хромдауда – құрамында 150 г/л хромогидриді, 1,5г/л күкірт қышқылы және де құрамы 250 г/л хром ангидриді мен 2,5 г/л күкірт қышқылы бар электролиттер қолданылады. Сонымен қатар процесс басталарда электролитке 1,2 – 2,5 г/л мөлшерде хромның үшвалентті ионы қолданылады. Электролиздеу процесінде катодта тотықсыздана отырып хромның алтывалентті қосылысын түзеді.
- электролиттік темірлеуде – құрамында түрлі үйлесімде хлорлы темір, хлорлы натрий және тұз қышқылы бар электролиттер қолданылса, ал ваннидан тыс темірлеу үшін келесі құрамдағы электролиттерді қолданады. Хлорлы темір – 500 г/л; тұз қышқылы – 1,5 – 3,0 г/л Бөлшектің тозған өлшемін электролиттік төсем төсеумен қалпына келтіруде процесс келесі сатылардан тұрады:
1) тозуды жою және бетке немесе бет элементіне дұрыспішін беру мақсатында механикалық өңдеу;
2) электролиттік төсем төсеу
3) алынған қабатты полинал (бастапқы) өлшемге өңдеу, қажет жағдайда механикалық өңдеу
Электролиттік төсем төсеу сатысы, төсем төселмейтін беттерді изоляциялау, бетті майсыздандыру, тотық пленкасын алу, тұнба төсеу, қабатты тұнба өнімінен шайып тазалау технологиялық өтулерді қарастырады.
Бөлшектің геометриялық пішіні мен өлшемін қалпына келтіру әдістері
Бөлшектің беттері мен бет элементтерінің геометриялық өлшемі мен пішінін қалпына келтіру үшін жөндеу шаруашылығында келесі әдістерді қолданады: балқыма қабат төсеу; металлдау; электролиттік металл қабатын өсіру; жұмсақ деформациялау және жөнделінген өлшемге өңдеу. Қарастырылып отырған әдістердің барлығы да, қалпына келтіруші бөлшек өлшемінің тозу дәрежесіне, пайдалану жағдайына қарай нақытылы қолданылады.
Балқымақабаттау (паплавка) әдісбалқытып төсеу күйдіру және өлшемді бастапқы өлшемге механикалық өңдеу сатыларынан тұрады. Әдісті цилиндрлік, жазық және біркелкі келтірілген беттер үшін қолданады. Балықмақабаттау барысында алынатын қабаттың беріктігі мен тозу төзімділігі атқарылу тәсіліне, қолданылатын электрод немесе присадкалық материалына, атқару тәсіліне қарай негізгі материалдан кем түспейді және тозған бетте жеткілікті металл қабатын өсіруге мүмкіндік береді. Мұндай қалың қабатты көп қабатты балқымақабаттауды бірнеше валиктерді түсіруменен атқарады – үйіліміне немесе сатылы жік түсруменен.
Балқымақабаттаудың басты кемшілігі – бұл, жергілікті қызу салдарынан орын алатын керенуліліктің нәтижесінде майысқақтану. Бұл кемшілікті алдын алу үшін келесі іс-әрекеттерді қолданады:
1) балқымақабатталушы бөлшекті 100-4000С температураға дейін қыздыру
2) цилиндрлік бөлшектер үшін жікті керісатылы төсеу неммес жазық беттер үшін кішігірім участкелерменен ретсіз түсіру;
3) балқымақабаттаудан соң термоөңдеу
Балқымақабатауменен болаттан, шойыннан, қоладан, қорғасыннан, сондай-ақ сырғанау подшипниктердің баббиттік вкадыштерін қалпына келтіруді Флюсті немесе инертті газды қолдана отырып болаттардан жасалған бұйымды қалпына келтіреді.
Балқымақабаттау
Әдістің сипаттамасы және қолдану жерлері . Механикалық өңдеумен үйлестіре отырып бөлшекте балқыма қабат төсеу бөлшектің геометриялық өлшемі мен пішінін қалпына келтірудің біршама кең таралған әдісі.
Әдістің негізгі жетістікері: құрылғыларының салыстырамлы қарапайымдылығы және қолданушы жабдықтарының кең таралғандығы: цилиндрлік, жазық және біркелкі келтірілген бөлшек беттерін қалпына келтірудің ерекшелігі; өте жоғарғы қабатты балқыма қабат төсеу жолмен елеулі қалыңдықтағы балқыған қабатты алу мүмкіндігі.
Балқыма қабат төсеудің кемшіліктері – кернеудің себебінен бөлшектің майысқақталуы, бөлшектің жергілікті қыздырылу салдарынан пайда болатын, жарғыншақ қалыптасу мен кеуектердің орын алуы.
Майысқақталуды қалпына келтіру үшін: 1. балқыма қабат төселуші бөлшекті 100-40000С температураға дейін газ оттығының көмегімен қыздыру қажет. 2) Цилиндрлік бөлшек беттерінде кері сатылы жікпен немесе кіші участкелермен бөлшектің тегіс бетінде жан-жақты пісіру воликтерін түсіру; 3) Балқыма қабат төселгеннен соң термиялық өңдеуді қолдану.
Балқыған қабаттағы жарғыншақтың пайда болуын алдын алу үшін, бөлшектің 200-2800С температураға дейін газ оттығының көмегімен қыздыру қажет.
Бу қалыптасуын төмендету үшін балқыма қабат төсер алдын электродты 1,5-2 сағат уақыт 200-2500С температурада алдын ала қыздыру қажет.
Балқыма қабат төсеумен бөлшекті қалпына келтіру әдісін болаттан, шойыннан, қоладан, қорғасыннан жасалған бөлшектерді сондай-ақ сырғанау подшипниктерінің баббиттік вкладыштерін қалпына келтіру үшін қолданылады.
Цилиндрлік бөлшектерде балқыма қабат төсеу
«Білік» типті цилиндрлік бөлшектерде балқыма қабат төсеу және механикаландырылған түрде жартылай автоматты және автоматты флюс қабатының астында балқыма қабат төсеу жүзеге асырылады.
Қолмен атқарылатын балқыма қабат төсеу елеусіз диаметрдегі және күрделі пішіндегі бөлшектер үшін қолданылады. Бұл әдісте валиктерді түсірудің кері сатылы әдісі қолданылады. Ені электродттың 2,5-3 диаметріне тең болатын валиктер жақсы сапаға ие болады. Бұл жағдайда балқыған болаттардың барлық кратерлері бір жалпы ваннаға құйылады, осының арқасында негізгі және балқыған материалдың жақсы ілігісуі қамтамасыз етіледі.
Ені ұлғайтылған валикті алу үшін пісіруші электродқа үш қозғалысты хабарлау қажет: электрод осі бойында жоғарыдан төмен қарай ілгерілеп, жік сызығы бойында ілгерлі қозғалысты және жікке көлденең оның осіне перпендикуляр тербелмелі қозғалыс.
Тербелмелі қозғалыс қырлардың қызуын қалыптастырады және де ваннаның суытылуын баяулатады.
Қолмен атқарылатын балқыма қабат төсеу әдісінің негізгі кемшілігі, оның еңбексиымдылығы мен төмен өнімділігі. Мұнан басқа, жоғары квалификациядағы пісірушінің қажеттігі.
Қолмен атқарылатын балқыма қабат төсеудің ақаулардың алдын алу үшін, оларды 700-8000С температураға дейін алдын ала қыздырған жөн.
Механикаландырылған балқыма қабат төсеу әдісі кезінде біршама тиімді тәсілі, винттік сызық бойынша балқыма қабат төсеу. Жұқа қабырғалы қуыс цилиндрлік бөлшектерде балқыма қабат төсеуді винттік сызығы бойынша үлкер адымда, екі өтуде орындайды. Бұл кезде екінші өтудегі валиктер бірінші өтудегі алынған валиктер арасына төселеді.
Балқыма қабат төсеуге арналған қондырғы сым төсегіш механизмі бар балқытқыш бүршіктен, бүршікті қозғалту және білікті айналдыру механизмінен және ток көзінен тұрады.
Балқытушы бүршікті токр станогының суппортында бекітеді, бұл айналу жиілігін 0,004 тен 0,33с-1 дейін өзгертуге арналған редуктормен қамтамасыз етілген. Бөлшекті патронда немесе центрде бекітеді. Ток бөлшекке мыс графитті щетка және патронда орнатылған сақиналы мыс доңғалағы арқылы келеді. Балқыма қабат төсеуді бөлшектің айналу кезінде балқытқыш бүршіктің ұзына бойғы супортпен бірге қозғалысында алдыңғы түсірілген валикті кейінгісі 1/3-1/2 енін жауып жататаындай етіп жүргізеді.
Флюсті қолдана отырып балқыма қабат төсеуді диаметрі 100 мм үлкен бөлшектер үшін қолданылады. Бөлшектердің кіші диаметрінде балқыма қабат төсеу біршама күрделенеді, себебі қажет қалыңдықтағы флюс қабатын ұстау қиын. Жөндеу кезінде кеңінен АН384А, АН384АМ, ОСЦ45 маркалы жоғары кремнилік марганецті флюстер, ал жиі, АН20, АН30 маркалы аз кремнилік флюстер қолданылады.
Жоғары кремнилік флюстерді негізінен көміртекті және аз көміртекті болаттарда балқымай төсеу барысында қолданылады. Бұл флюстер жікті марганецпен және кремнимен қанықтырады да оттегін біршама тотықтырады. Төмен кремнилік және марганецсіз флюстерді орташа және жоғарғы қоспалық болаттарда балқыма қабат төсеу үшін қолданылады. Бұл флюстер балқыма қабат төсеу кезінде қоспалық элементтерді аз қоспаландырады.
Балқыма қабат төсеу кезінде ток шамасын келесі өрнек бойынша анықтауға болады.
1=10d+10d2
Мұндағы d – пісіру сымының диаметрі, мм.
Балқыған қабаттың жоғарғы сапасы кері полярлықтағы тұрақты токты қолдану мен қамтамасыз етіледі, себебі тұрақты ток балқыма қабат төсеу процесін қалыптастырады, будың түзілуін төмендетеді шлактық қабықтан тазарту талап етілмейді.
Көмірқышқыл газы ортасында балқыма қабат төсеу, оның тотықтыру әсеріне байланысты жоғары құрамды марганеці мен кремниі бар балқығыш сымын қолданумен жүреді – Нп 40Г, Нп 50Г, Нп 30ХСА
Тозу тұрақты материалдармен балқыма қабат төсеу
Бөлшек бетінің тозуға тұрақтылығын жоғарылату үшін, интенсивті абразивті және эррозиялық тозу жағдайында жұмыс істейтін, олардың бетіне қатты қоспадан балқыма қабат төсейді. Бұл кезде қоспаландырушы элементтер жақпа қабатының құрамына енгізілген пісіру сымынан дайындалған стержендік электродтар кең қолданыс тауып отыр.
Балқытылған қабаттың физико-механикалық қасиетіне қойылған талапқа байланыстағы келесі электродтарды қолданамыз:
1. Т-300 электроды. Соққы күшінсіз абразивті тозу жағдайында жұмыс істейтін, шойындық және болат бөлшектерге балқыма қабат төсеу үшін қолданылады
2. Т-600 электроды. Абразивті тозу және бірқатар төмен соққы күші жағдайында жұмыс істейтін болат және шойыннан жасалған бөлшек үшін қолданылады.
3. Т-540 электроды. Абразивті тозу және соққы күші жағдайында жұмыс істейтін бөлшекте балқыма қабат төсеу үшін қолданылады.
Балқытылып төселген қабат беті, балқытылған валикпен қалыптасқан үлкен толқындыққа ие болады. Сол себепті, механикалық өңдеу барысында үлкен әдісі – шамасын тағайындауға мәжбүр етеді. Ал бұл өз кезегінде кескіш құрал шығынының өсуіне әкеледі. Мұндай жағдайларда механиклық өңдеудің еңбексиымдылығын – төмендету үшін балқыма қабат төсеумен бірге бір мезгілде жазғылау роликтерімен жұмсақ деформациялауды қолданады.
Доғалы балқыма қабат төсеу барысында негізгі болаттың терең балқытылуының салдаырнан, талап етілген қасиеті мен қоспа құрамы үшінші және онан кейінгі қабаттарда қалыптасады. Сол себепті балқыма қабат төсеу үш қабаттан аз болмайды. Балқыма қабат төсеуді кері полярлықтағы токта жүргізеді. Бірінші өтуде азайтылған ток күшін қолданады. Ацетилендіотекті жалын көмегімен қатты қоспадан балқыма қабат төсеу барысында балқытылып төселген қабаттың негізгі болатпен араласуы болмайды. Плазмалық балқыма қабат төсеу әдісіне қарағанда негізгі болаттың аз балқуын қамтамасыз етеді.
Балқыма қабат төселгеннен соң бөлшекті 8500С температурада күйдіруді жүргізу үшін ошаққа орналастырады, сонан соң оны баяу суытады.
Дірілді доғалы балқыма қабат төсеу
Дірілді доғалы балқыма қабат төсеудің артықшылығы, бұл, бөлшектің қалпына келтірілуші бетінің әлсіз қызуы және де термиялық әсер ету аймағының аз шамасы. Білік материалының физико-механикалық қасиеттері тіпті өзгермейді, ал балқытылып төселген қабатқа іргелес жатқан материал аймағында структура алғашқы қалыпта сақталады. Тіпті көміртектік құрамдағы электродтарды қолдану барысында өзіндік жоғарғы беріктік және де тозуға тұрақтылығымен өзгешеленетін балқытылған болаттың шынықтырылған структурасының барлық түрін алуға мүмкіндік туады. Дірілдоғалы балқыма қабат төсеуді шынықтырылған және шынықтырылмаған болаттар үшін, сондай-ақ цементецияланылған төмен қоспалы болаттардан дайындалған бөлшектерді қалпына келтіру үшін қолдануға болады. Бұл тәсілмен диаметрі 15 мм және онан жоғары цилиндрліка бөлшектерде балқыма қабат төсеуге, подшипниктің отырғызылу беттерін қалпына келтіруге болады. Бұл әдісті бұранда, майда шлица түріндегі пішінді беттер үшін қолдану тиімсіз.
Дірілдоғалы балқыма қабат төсеудің негізгі кемшіліктері: қалпына келтірілген болаттың шаршау беріктігінің төмендеуі; кейінгі өңдеудің күрделенуі; осы әдіспен балқытылып төселген қабатта толық жаймайынша қайта балқыма қабат төселумен немесе қалпына келтірудің басқа әдістерімен қалпына келтірудің мүмкін болмауы.
Бұл әдіспен балқыма қабат төсеудің мағынасы төмендегідей.
Балқыма қабат төсеу орнына берілген, дірілдемелі электродтық сыммен балқыма қабат төселуші бөлшек арасында мезгілді электрлік доғасы қоздырудың нәтижесінде, доға есебінен электрод ұшының және бөлшек беті балқи отырып, балқыған болат ваннасы қалыптасады. Балқыту орнына суытушы сұйық беріледі, осыған орай болат жылдам суытады. Бөлшектің тиімді айналу жылдамдығында бетінде ені электрод димаетріне қарағанда екі есе үлкен болатындай балқытылған валик қалыптасады. Қатарына төселген валик пен өзара балқи отырып тұтас қабат түзеді. Суыту сұйығы ретінде глицириннің кальциленілген соданың судағы ертіндісі қолданылады.
Тәжірибемен орнатылғандай, суыту сұйығы ретінде 10-20 % глицириннің ертіндісін қолдану барысында жақсы нәтиже қамтамасыз етіледі.
Процестің тұрақтылығ негізінен суытылу сұйығының мөлшеріне және оның берілу тәсіліне байланысты. Әдетте, суыту сұйығы тікелей балқыма қабат төселуші аймаққа емес, пісіру доғасы жанын жатқан орыннан 10-20 мм қашықтықта беріледі, ал орташа көміртекті болатта балқыма қабат төсеу барыснда бұл арақашықтық 30-40 мм аралығын қарастырады. Суытылушы сұйық аынының балқыған болат ваннасына түсу балқытылған қабат жігінде қуыстылық пен кеуектіліктерді қалыптастырады.
Сымның берілу жылдамдығын нақты жағдайға байланысты таңдап қабылдайды. Бұл жылдамдықтың тиңмді шамасы 0,6-1,5 м/мин деп есептеледі. Едәуір төмен жылдамдықта дененің жануында үзіліс болады және де балқытылған төселген валикте қуыстылық қалыптасады. Ал сымның берілуінің едәуір жоғары жылдамдықтарында, ол балқып үлгермейді.
5,4 кесте
Төселген балқыма қабат қалыңдығы, мм |
Жылдамдығы, м/мин |
Балқыма қабаттың төселуі |
Электрод амплитудасы, мм |
|
Балқыма қабат төселу |
Сымның берілу |
|||
0,5 |
2 |
0,8 |
1,5 |
1,5 |
0,7 |
1,5 |
0,4 |
1,5 |
1,8 |
0,9 |
1 |
1 |
1,5 |
2 |
1,5 |
0,6 |
1,2 |
1,8 |
2 |
Бөлшекті қалпына келтіруді 14-18В кернеулікте орындайды. Кернеуліктің жоғарылауы барысында, процесс біршама тұрақты жүреді – ток күші өседі, ал осыған сәйкес жылу бөліну интенсивтілігі жоғарлайды. Пісіру жүйесінде ток өздігінен реттелініп отырады. Тұрақты керену барысында ток күшінің шамасы электродтық сымның диаметріне және оның берілу жылдамдығына тәуелді болады. Дірілдоғалы балқыма қабат төсеу тәртібі 5,4 кесетед берілген.
Сұйықтағы дірілді балқыма қабат төсеу процессі түзілген қабаттың шынығуымен жүретін болғандықтан, қалпына келтіруші бөлшектің механикалық өңделуі тек ажарлау әдісінің көмегімен жүреді.
Металлдау
Металдау соққылы күш жағдайында жұмыс істемейтін бөлшектерді қалпына келтіру үшін қоладанады. Арнаулы қондырғыда балқытылған метал, - метализаторда, бірнеше микрондағы түйіршіктерге шашыратыла отыырп сығылған ауамен қылпына келтірілуші бөлшек бетіне төселеді. Шашыратылып төселген қабат пен бөлшек арасындағы ілігісу молекулярлы-механикалық күш есебінен жүреді де ол шама 10-25 МПа жетеді. Металдау мен бөлшекті қалпына келтіру процесі кезектесе орындалатын келесі үш сатыдан тұрады: 1) төсемді төсеу үшін бөлшек бетін дайындай; 2) металды төсеу; 3) металдаудан соң бетті өңдеу.
Бетті металдауға дайындау, оны тазарту және оның бетінде «үздік бұранда» ою тәсілімен қажетті адырлықта қалыптастырумен жүреді. Мұндай адырлық шашыратылған қабатпен бөлшек беті арасында сенімді ілігісуді қамтамасыз етеді. Металдауға тағайындалған бөлшекті, оған дұрыс пішін беру мақсатында алдын ала жонады. Сонан соң үшкір кесу қыры бар кескішпен өңделген бетте үздік бұранданы ояды, үздік бұранда алу үшін кескіш ұшын біліктің айналу осінен 2,6-дан 6 мм-ге дейін арақашықтыққа төмен қарай соғыстырады. Өңдеу процесінде біліктің дірілі пайда болады, бұл өңделуші бөлшек бетінде металдың ұлғайтылуына және де үлкен адырлық шамасының қлыптасуына әкеліп соғады. Металданушы бетте ойықтар шегі болса, соншалықты оынң беттегі саны көп болады да негізгі материалмен шашыратылған қабат арасындағы байланыс жақсы болады.
Метализаторлар металды балқыту тәсіліне байланысты газ жалынды және электрлік болып келеді. Өндіріс орындарында жиі электрлік метализаторларды кеңінен қолданады. Электродты балқыту үшін, олардың арасында қоздырылушы, электр доғасын қолданады. Электродта шашыратқыш қаңқасында орналастырылады.
Металды төсеу процесі келесі кезектілікте орындалады – металды балқыту орнына беру; метал түйіршіктеріне елеулі жылдамдық беру, жылдам қозғалып келе жатқан түйіршіктің бөлшек бетіне соқтығысуы және төсемнің қалыптасуы.
Металдау барысында бөлшектің механикалық қасиеті өзгермейді, ал келтірілген елеусіз жылу салдарынан майысқақталуы мүмкін.
Металдаудың кемшілігі – төсемнің бөлшек материалымен ілігісуінің төмен беріктігі мен процесстің үлкен еңбек сыйымдылығы. Сол себепті металдаудың қолданылуы, сйық үйкелісу маен елеусіз жүктемелер жағдайында жұмыс істейтін ірі бөлшектерді қалпына келтіру үшін шектелген.
Электролиттік әдістер
Бөлшекте электролиттік төсем төсеу әдістеріне хромдау, темірлеу, никелдеу, мыстау, цинктеу және т.б. әдістер жатады. Жиі жөндеулер кезінде хромдау мен темірлеу қолданылады. Төсемнің максимал қалыңдығы хромдау барысында 0,2-0,3 мм-ге, ал темірлеу барысында 2-3 мм-ге жетеді. Бұл жағдай темірдің хромға қарағандағы тұндырылу жылдамдығы 10-20 есе жоғарылығымен түсіндіріледі. Хромдау бөлшекті электролиттік қалпына келтіру әдістерінің ішіндегі басты мағынаға ие болады, себебі хромдық қабат төселген бөлшектер үлкен қаттылық пен тозу тұрақтылыққа ие. Сондай-ақ мұндай төсемдер үлкен коррозияға қарсы тұру қасиетіне ие болады. Темірленген беттер елеусіз қаттылыққа ие болады. Темірлеу әдісіимен төселген қабат, өзіндік физио-механикалық қасиеті бойынша жуық шамамен орташа көміртекті болаттарғ сәйкес келеді.
Электролиттік хромдау
Хромдау процесі, өзіндік жоғарғы тозу тұрақтылығымен, қаттылығымен, аз үйкелісу коэффициентімен, және де негізгі материалмен жақсы ілігісуімен сипатталатын бетті алуға мүмкіндік береді. Хромдаудың негізгі кемшілігі – хромның электролитте төмен тұну жылдамдығы мен оның майлау майымен нашар малынуы. Іс-тәжірибеде хромдау процесін жүргізу үшін құрамында негізгі компоненті ретінде хромның анедридін қарастыратын электролиттер қолданылады. Сапасы бойынша қанағаттандырылатын хромдық төсем алу үшін, хромда елеусіз шамадағы SO4-2 ионы бар болуы қажет. Әдетте электролитте хромдық ангридиді мен күкірт қышқылының қатынасын 100:1 етіп қабылдайды. CrO3 аз консентрациясы кезінде біршама үлкен ток бойынша шығынды алуға болады., бірақ ваннада кернеу жоғарылайды. Төмен консентрациядағы электролиттерде жоғары консентрациядағы электролиттерге қарағанда жоғарғы қаттылықтағы төсем алуға болады. Бірақ төмен консентрациядағы электролиттің кемшілігі – жиі хромдық ангридидінің қосылып отыруы. CrO3 үлкен консентрациясы хромның ток бойынша шығынын төмендетеді және үлкен электролид шығынына әкеліп соғады. Бөлшекті қалпына келтіру үшін негізінен төмен немесе орташа консентрациядағы электролиттерді (150-250 г/л CrO3 және 1,5-2 г/л H2SO4 немесе 200-250 г/л CrO3 және 2,-2,5 г/л H2SO4 ) қолданады.
Бейметалдық материалдардан жасалған бөлшектерді жөндеу. Бейметалдық материалдардың қолданылу салалары
Өнеркәсіптің түрлі салаларында қолданылатын машиналар мен аппараттардың кейбір бөлшектерін болат емес материалдардан жасайды.
Материалдың әрбір түрінің қолданылу жерлері оның физико-химиялық қасиеттерімен және де технологиялығымен анықталады. Қазіргі таңда, машиналар мен аппараттардың жеке бөлшектерін дайындау үшін пластмассаларды, резеңкені, кей жағдайларда шыны мен ағашты кең түрде қолданады.
Машина және аппарат жасаудағы қолданылып жүрген болат емес материалдардың кең таралған түрлі пластмасса болып табылады.
Пластмассаның қолданылуын болатпен салыстырғанда көп жағдайда артығырақ ететін қасиеттер жиынтығына ие болуы: едәуір арзан: меншікті салмағы аз: жону, пісіру және басқа да әдістермен өңдеу барысындағы технологиялығы. Пластмассаның қолданылуы болатқа қарағандағы төмен техникалық беріктілігімен: балқу температурасының төмендігімен: ылғал сіңіруге бейімділігімен және де соның салдарынан ісінуімен әсіресе күн сәулесінің әсерінен ескіруге бейімділігімен шектеледі.
Қазіргі таңда пластмассаны: аппараттың ішкі бетін коррозиядан сақтандыру үшін төсем ретінде: білік беттерін қалпына келтіру және де білік-төлке типті кинематикалық жұптарда фрикцияға қарсы төсем өсе түсу үшін: құбырларды және құбырлық арматураларды дайындау үшін, кеңінен қолданады.
Өнеркәсіпте пластмассамен бірге резеңкеде кең қолданым тауып отыр. Резеңке конструкциялық материал ретінде, кең ауқымдағы бұйымдар номенклатурасын дайындау үшін кеңінен қолданылады.
Резинканың едәуір басты артықшылығы: герметикалығы, жұмсақтығы, механикалық өңдеу әдістерімен жақсы өңделімділігі, аз меншікті салмағы. Тоқыма негізбен біріктіріле отырып резеңке созылып жұмыс істеу барысында жоғары беріктікке ие. Өнеркәсіпте мұнай өнімдерінің әсеріне (майлау майына, бензинге және т.б.) тұрақты резинкалар шығарылады.
Резеңке тоқымалы материалдардан негізінен сынады – белбеулі берілістердің жетектік белбеулері, тасымалдағыш таспалар дайындалады. Тезеңкенің біршама пластмассаға қарағанда кең қолдану тапқан саласы, оны тығыздауыш бөлшектер – монжеттер және сальниктер жасау үшін қолданылды. Резеңкені қолданудың ең басты орыны оны әртүрлі конструкциялардың бекіту жерлерінің тығыздаушысыретінде (тасымалдағыш, бункерлер және т.б. жабдықтардың тығыздаушысы) сондай-ақ ыдыстардың ішкі беттерін коррозия әсерінен қорғау (резеңкемен қаптау) үшін қолданылуы.
Резеңкенің қолданылуын шектеуші басты кемшіліктері: ескіруге бейімділігі, оталу температурасының төмендігі, жақсы жанғыштығы. Мақта-мата тоқымасы негізінде жасалған тасымалдау таспасы ылғал ортада жұмысістеген кезде шіруге бейім.
Шыныдан жасалған бұйымдар негізінен аппараттың келесі бөлшектерін: аппараттар мен машиналардың байқау-бақылау саңлауларын, шыны құбырларды, түтіктерді және т.б. бұйымдарын дайындау үшін қолданылады. Шынының басты кемшіліктерінің қатарына оның жоғарғы морттылығы мен механикалық әдістермен нашар өңделетіндігін жатқызуға болады.
Темір беттерге пластмассадан төсем төсеудің технологиясы
Жоғарыда айтылғандай пластмасса төсем ретінде аппараттардың ішкі беттерін қорғау үшін, сондай-ақ ұзақ мерзімді эксплуатациялану процесінде тозуға ұшыраған білік мойнының беттерін қалпына келтіру үшін қолданылады. Соңғы жағдайда бетті қалпына келтіруден басқа, ол жаңа сапаға ие болады – майлау майынсыз жұмысістей алу қабілеті. Бөлшек бетіне төселген пластмассаның жұқа қабаты іс-жүзінде оның механикалық көрсеткіштеріне елеулі әсер етпейді, бірақ пластмасса төселген бөлшек беті, біршама икемді болады. Сол себептен білік пен төлкенің жинасу бетінің ұлғаюы байқалады.
Пластмассадан төсем төсеудің әдісітөсемнің тағайындалуына, өселуші беттің пішіні мен өлшеміне байланысты қабылданады. Пластмассаның төселу технологиясына қатаң әср ететін факторлар – төселуші пластмассаның түрі. Термо жұмсақ пластмассалар, әдетте, балқытылған түрде құю әдісімен және де шашырату жолымен төселеді. Бұл кезде процесстің температуралық тәртібі пластмассаның түріне байланысты болады және де бұл мәіметтер анықтамаларда келтіріледі. Көптеген жағдайларда еңбек өнімдлігін жоғарылату үшін пластмасса табақтарын желімдетуді қолданады. Мұндай әдістерді шіні бойынша қарапайым аппараттардың (ыдыстардың және т.б.) ішкі бетін қорғау үшін қолданылады. Термореактивті пластмассадан қорғаушы қабат төсеу тек қана желімдеу жолымен жүргізіледі.
Пластмассаны білік бетіне төсеу барысында, алдын ала оның бетіне геометриялық пішін беру үшін механикалық тәсілмен өңдейді. Сонымен қатар беттің адырлығы төсем мен негізгі қабаттың жақсы байланысуын қамтамасыз етуі тиіс. Қажетті жасанды адырлық алу үшін кескінің ұшын біліктің айналу өсінен 3-4 мм-ге төмен орналастыру жеткілікті. Пластмассаны төсеу қысым арқылы құю әдісімен жүзеге асырылады. Пластмассаны құяр алдында, бөлшек беті мен пресс-пішінді қажет температураға дейін қыздыруқажет. Пластмассаның пресс-пішін бетіне жабыспауын қамтамасыз ету үшін, оның бетіне жұқа қабатта силикон майын жағады.
Бұл кездегі төселетін пластмассаның қабаты қалпына келтірілуші беттің барлық ұғымдығында бірдей және мүмкіндігінше минимал қалыңдықта болуы тиіс. Қарастырылып отырған әдістің негізгі артықшылықтары: 1) қабатты төсеуден соң оны механикалық өңдеудің қажетсіздігі; 2) Білік мойынын қалпына келтіру кезінде бірнеше рет қолданылу мүмкіндігі; 3) Кинематикалық жұптарда майлау майынсыз жұмысістеу мүмкіндігі; 4) алынған қабаттың жоғарғы тозу тұрақтылығы.
Әдістің қолданылуы 60 +800 С-дан аспайтын температурада, сондай-ақ пластмасса қабатын төсеу процесінің технологиялық параметрлерін сақтауға қойылатын қатаң талаптармен шектеледі. Пластмассаны төсер алдында оны кептіріп алу қажет, ал ьөсеу процесінде көрсетілген температуралық тәртіпті қатаңсақтау қажет. Шамадан тысқызып кету төселген қабаттың мортты қасиетке ие болуына және де онда жарғыншақтың пайда болуына әкеліп соғады. Ақаудың пайда болуының сырттай көрінісі, төсем үшін алғаш шикізаттың түсіне қарағанда біршама күңгірт түске өзгеруі.
Пластмассалық қабатты ортадан тебу тәсілімен құю, тербелмелі подшипникті ортада тебу күші көмегімен құю әдісіне ұқсас келеді.
Пластмассалық қабатты төсеудің газ – жалынды әдісі қажетті температураға дейін бөлшекті қыздырып, сонан соң ұнтақ тәрізді пластмассаны төсеумен жүреді. Тозаңдату, құрамында пластмасса балқымасы бар газ-жалынды ағын толасымен бетке үрлеу көмегімен жүреді.
Қорғау қабатын төсеудің жоғарыда сипатталған әдістерімен қатар, табақшалы материалдардан фторопластан және полипропиленнен жасалған коррозияға қарсы төсемдерде кеңінен қолданылады. Фторопласт – аса тиімді төсем, бірақ металлға төмен дәрежедегі адгезиялық қаситеі бар. Сол себепті төсемнің қорғалушы бетке сенімді бекітілуін қамтамасыз ету үшін қосымша шаралар қолдану қажет. Фторопласттың сенімді бекітілуін қамтамасыз етудің біршама кең таралған әдісі – фторопласт қабаты мен шыны тоқыма қабатынан тқратын қос қабатты төсемді қолдану. Мұнда фторопласт пен шыны тоқымасы арасында, байланыстыру – материалы болып табылатын фторопласт – 4 қабығын орналыстырады. Осылайша алынған үш қабатты материал, орамға оралып 320-3800 С қыздырылады, сонан соң эноксид желімінің көмегімен қорғалушы қабатқа бекітіледі.
Сондай-ақ пропиленді, шыны тоқымасы мен эноксид желімінің көмегімен серпімді етіп қорғалушы бетке желімдейді..
Көп жағдайларда серпімді полиэтиленнен жасалған қорғау қабатын қолданады. Полиэтилен 88 маркалы желімніңкөмегімен төселеді. Желім қабатын төсер алдын, төсем төселуші қабат құматқылау әдісімен өңделеді. Полиэтиленнен жсалған дайындамаға да 88 марка желімнің екі-үш қабатты жағылады. Желімнің әрбір қабаты 20-30 минут келтірілуден өтеді, сонан соң дайындама болат бетіне төселіп роликтің көмегімен жазылады. Әрбір табақшалар арасындағы түйісу жерлері пісіру пистолеті көмегімен ыстық ауаны қолдана отырып пісіріледі. Сонымен қатар, фторопласттық қорғаушы қабат электростатикалық өрісте тозаңдату көмегімен төселуі мүмкін. Шыны пластиктерді желімдеу, шыны тоқымасының қалдықтарымен араластырылған ПН-1 маркалы смоласымен жүзеге асырылады. Бұл тәсілде төселуші қабатты бетке дәл келтірудің қажеттігі жоқ, себебі қабықша мен жабыстырылушы фланец арасындағы бос кеңістік смоламен толтырылады. Қатаю мерзімі 1,5 – 2 сағат. Бөлшекке жабыстырылған пластмассалық қабаттың жарақаты, тиісті участкелерді тазартып сонан соң фиониттік жақпа қоспасы мен графиттік жағумен қалпына келтіріледі.
Пластмассалық бұйымдарды пісіру және желімдеу
Пластмассаны пісіруді, пісірілуші бетті сұйық аққыш күйге дейін қыздырудың көмегімен орындайды. Жылу көзі ретінде қыздырылған ауаны қолданады. Ауа тепмературасы пластамасның түріне байланысты болады. Пісіру присадкалық материалдарды қолданумен және онынсыз жүреді. Присадкалық материалдарды қолданусыз пісіру кезінде сұйық аққыш күйге дейін қыздырылған түйісу қырларын 0,2 + 0,4 мПА қысым түсіре отырып қосады. Бұл кезде суытуды күштік жағдайда жүргізеді. Қыздыру температурасы: фторопласт үшін – 3700С; органикалық шыны үшін -140 + 1450С; полипропилен -210+2400С құрайды.
Пластамассалық құбырларды пісіріп жалғастырудың конструкциялары. (а-қиғаш: б-корпусты: в-бір-біріне кигізіп)
Пісірілу жік материалының беріктігі, негізгі материалға қарағанда төмен болғандықтан, пісірілу орындарын күшейту үшін конструктивтік сипаттағы шараларды қолданады. Пластмассалық құбырлардың жалғанған жерлерін пісіру кезінде, пісірілу түйіспелерін мықтау үшін, қиғаш (5,1 а сурет), конустық (5,1 б сурет) бір-біріне кигізілген) (5,1В сурет) жасақтауларды қолданамыз. Пластмассаны желімдеулі негізінен басты мақсатта құбырлар мен қаңқаларды герметизация, төсем төсеу және бұйымның бүтінділігін қалпына келтіру барысында қолданады.
Жөндеу кезінде желімдеуді қолдану жерлері бұл, қоңқалық бөлшектердегі жарғыншақтармен өн бойына өткен саңлауларды бітеу, қозғалмайтын қосылыстарды қалпына келтіру, майысулар мен тегіссіздіктерді түзету.
Қозғалмайтын қосылыстарды қалпына келтіру үшін, ең алдымен бөлшектерді коррозия өнімдерінен тазартамыз. Желімдену бетін ұлғайту үшін бетке жасанды адырлық береміз. Бұл үшін бетті егеумен, кескішпен және тағы басқа да өткір жүзді құралдармен дөрекі өңдеу әдістерін қолданамыз. Сонан соң бөлшекті майсыздандырып кептіреміз. Процестің аяқталушы сатысы бұл, бөлшектерді бір-біріне қосу және түрлі көмекші құрылғылар көмегімен қосылысқа қысым түсіру.
Өнеркәсіптердегі жөндеу шаруашылығында кең қолданыс тауып отырған эпоксидті негіздегі желімдер. Бұл желімдер келесі бір қатар құнды қасиеттерге ие – коррозияға қарсы тұру қасиеті, мұнай өнімдерінің қышқылдар мен сілтілер әсеріне тұрақты желімдік қосылыстар беріктігі температураның 1000С-қа дейінгі жоғарылауы кезінде әлсіремейді.
Эноксидтік негіздегі желімдердің негізгі компоненті бұл ЭД-16, ЭД-20, ЭД-40 эпоксид смолаларға жұмсартқыштар (салмағынан 16 пайызға дейін) қосылады. Жұмсартқыш ретінде дибутил фтолатты қолданады. Тікелей, қолданар алдын 7-16 пайыз мөлшерде қатайтқыштар қолданады. Қатайтқыштарды таңдап қабылдау түйіспенің жұмыс істеу жағдайына және де жөндеу жұмысының сипатына байланысты. Өте жоғары температурада жұмыс істейтін түйіспелер үшін (1200 С дейінгі) фталилік және малейіндік андегридтерді қолданамыз. 1000 С дейінгі температурада жұмыс істейтін түйіспелер үшін полиэтилен полиамидті қолданады. Қатайтқыштарды желімге жұмыс бастауға 15-20 минут алдын араластырылады. Малейндік қатайтқыштарды қолдану барысында бұл мерзім 5 тәулікке дейін созылады.
Шыныдан жасалған бөлшектерді өңдеудің және жөндеудің технологиясы
Силикат шынысын конструктивті материал ретінде, негізінен, технологиялық құбырларды және түрлі пішіндегі шынылық жазық әйнектерді дайындау үшін қолданады. Шыны құбырының ақауы негізінен, оның сыныуымен немесе жарылуымен түсіндіріледі.
Көпшілік жағдайда бұл бөлшектердің жөнделуі ақау болған бөлшектерді жаңа бөлшекпен ауыстыру көмегімен жүреді. Бұл кезде жиі шыныны кесу және пісіру операциялары орындалады.
Жазық шыны табақшаларын кесу шыны кескіштің көмегімен орындалады. Кесу операцияларындағы, біршама күрделісі бұл, шынылық құбырларды кесу. Бұл үшін қазіргі кезде бірнеше әдістерді қолданады: 1) Жергілікті қыздырып сонан соң ау немесе сумен жылдам суыту; 2)Обрезивті доңғалақпен кесу; 3) Шыны кескіш құралмен кесу жазық дайындамада саңылау ою кезінде ультрадыбыстық және басқа да әдістерді қолдану мүмкін.
Жергілікті қыздырумен құбырларды кесу барысында, құбырдың кесілуге тиісті жеріне нихром сымының орамын орайды. Спирал хромы қоректенетін ток автотрансформаттың көмегімен реттеледі.
Жылдам суытудың нәтижесінде сақиналы жарғыншақ қалыптасады.
Шыны кескіштің көмегімен шыны құбырын кесу токр станогында жүзеге асырылады. Бұл кезде шыны кескішті станок суплортында, ал құбырды резинкалы немесе ағаш оправканың көмегімен станоктың центрінде орнатады.
Құбырды пісіруді газ электрлік пісірудің көмегімен орындайды. Пісірудің технологиялық рпоцессі келесі операцияларды қарастырады: құбырларды бір-біріне центрлеп орнату; құбырдың қырларын 650-7980С дейін қыздыру (шынының жұмсару температурасы); қыздырылған кескін беттерді қосу. Сонан соң пісірілу жігінің өзара қарама-қарсы жатқан екі нүктесіне 3-4 минутқа жоғарғы кернеуліктегі токты қосады; пісірілу жігін күйдіруді анителенді – оттектік жалын көмегімен қыздыра жүреді.
Жоғарғы жиіліктегі ток көмегімен шыны құбырын пісіру пісірілу жігін 650-7000С температураға дейін алдын ала қыздырудың қажеттігі, бұл, шынының 5000С температурадан өз бойынан ток өткізбейтіндігімен түсіндіріледі.
Шыны құбыр бетіндегі жарғыншақтар, жарақаттанған участкелердегі бірнеше қабат шыны тоқымасын орау көмегімен қалпына келтіріледі. Бұл кезде байланыстырған материал ретінде эпоксид желімін қолданамыз. Елеусіз ұзындықтағы құбырлар болат құбырының көмегімен тұтастырылады. Бұл кезде шыны тоқымасының талшығы түрінде толықтырғышы бар эпоксид желімін қолданған жөн.
Резеңкеден жасалған бұйымдарды өңдеудің және жөндеудің технологиясы
Тасымалдағыш лентасын тозған қырларды тігумен немесе істен шыққан участкелерді ауыстырумен жөндейді. Вулканизациялаумен лентаның ұштарын жалғауға дайындауды келесідегідей орындайды. Алдын ала лентаның тоқыма төсемдерінің сатысымен қиғаш кесуді орындайды, сонан соң оның ұштарын пышақпен немесе зімпаралы қағазбен (лентаның шамадан тыс енінің болуы кезінде электражарлау машинасының біліге отырғызылған доңғалақ болат щеткасымен) мұқият тазалайды.
Резеңкелі лентаны, резеңке өнеркәсібінің ҒЗИ-мен жете дайындалған, технолгияны жетекшілікке ала отырып ыстық вулканизациялау әдісімен жалғайды. Жалғау кезінде ЛС-425 желімін және БР-1 немесе БР-2 бензинін қолданады. Жалғастырушы беттерді сүрту және де желімнің тұтқырлығын төмендету үшін техникалық этилоцетатты қолданады, бұл бензинмен бірге (1,2; 1) қажетті консентрациядағы компоненттерді алу үшін желімге араластырылады. Төсемдік және жоспарлау материалы ретінде қалыңдығы 0,5 мм№450 колондорлық резеңкені және ИРП -1371 -12 мм қалыңдықтағы резеңкені немес резеңке сіңірілген брекерлік тоқыманы қолданады. 1м2 жалғанған бетке кететін материалдар шығын (кг-да); 1,5 ЛС-425 желімді; 1,2 №450 резеңкені; 1,3 ИРП-1371—1 резеңкені құрайды.
4-6м ұзындықта лентаны жалғау үшін вулканизациялауға ыңғайлы орында демеуші роликтерді адып тастап, оның орнына ағаш жайма тақтасын төсейді. Жайма тақтаның ұзындығы жалғама ұзындығынан 1м-ге ұзын, ал ені табаннан 200-300 мм-ге енді болуы керек. Лента ұштары (кергіш бараманды алғашқы жағдайға орнатқан кезде) жалғану ұзындығында жапсарлана біріктірілетіндей етіп тұтастырылады.
Сатылардың бетін корундты ажарлау қайрағының көмегімен пневмаажарлау машинасында өңдейді. Сонан соң оны шаңнан және резеңке қиқымдарынан сығылған ауамен (немесе щеткамен) тазартады.
Үрлеп тазартқаннан соң авиация бензиніне батырылған матамен сүртеді, және де инфроқызыл лампамен немесе фенмен 10-15 мин. Уақыт кептіріледі. Желімденуші бетке щеткамен екі рет біркелкі желім қабатын жағады, бұл кезде әрбір жағылған қабаттан соң қабат кептірілуге беріледі: біріншісі 20-30мин., екіншісі 10-15 мин., жабысқақтық жоғалғанға дейін.
Кептіруді жеделдету үшін ЭВН-6 жылу электр жеделдеткішін қолданады.
Жалғанатын беттердің біріне 15 мин. Аралығында авиация бензиніне батырылған протекторлық резеңкені төсеп мұқият ортадан шетке қарай құрыш роликпен жазады. Сатылардың шекарасында лента ені бойынша жазық ені 3-5 мм және қалыңдығы 1,55 мм жұқа резеңек қабатын роликпен жазып жабыстырады. Осылайша дайындалған лента ұштарын, жоғарғы сатыдан бастап бір-біріне төсей отырып, бүкіл бетті ортасынан шетке қарай жазғылайды; соңғы сатыны ауа шығу үшін бізбен теседі.
Жалғама кескін беттеріне екі рет әрбір қабатты келтірумен желім жағылады. Екі кескін бетіне де ені 100 м болатын қыспақ төселеді, ал оларға – ИРП1-1371-1 жапсырмалы резеңкеден дайындалған рещенке дайыедамас төселеді (мұның қалыңдығы 1,5-2,5 мм-ге жапсырма қалыңдығынан үлекн). Талк (немесе пергамент қағазы, целофан төселген) себілген ленталардың жалғанған жерлері сыртқы ауаның температурасы 50С төмен болмайтындай жағдайда престе фулканизациялайды. Пресс өздігінде екі құрыш плитасын (дюралюминий) және винттік тұтастырғыштан тұрады.
Тасымалдай лентасын жалғауға арналған ыстық (t>1000С) және суық қатаюдағы желім маркасын орамның ұшына бекітілген зауыттың жазба қағаздарында көрсетіледі.
Сегіз диафрагмаланған бөлімшесі мен қызған ауаны тарату саңлауы бар жермен тұйықталған әрбір плита ішінде, асбестпен (б-4,-5мм) оралған газ құбырлары орнатылған. Құбырға никель, нихром немес фехрал сымын қыздырғыш спирал оралған, спиралдар кезектесе қосылған.
Қыздыруға арналған плиталар пісіру трансформаторына жалғанған (кернеу 65В, ток күші 160А); сығылған түйіспеге түсірілген қысым 1 МПА аз болмауы тиіс.
Лентаның вулканизациялану температурасы t мен ұзақтығы i төсем санына n байланысты болады.
t=1430С және i=18-20 мин, егер де n=3 болғанда;
t=1430С және i=25 мин,. Егер де n=4 болғанда;
t=1400С және i=30 мин, егер де n=5 болғанда;
t=1400С және i=35 мин, егер де n=6 болса.
Уақыттың есептелуі, төменгі плитаға бекітілген термометр бойынша бақыланып отырған қажетті температураға қол жеткен кезде басталады.
Вулканизациялаудың нұсқалған жылулық тәртібіне байланысты, пресстер берілген температураны бақылап және де берілген шамада ұстап тұруға мүмкіндік беретін, түрлі автоматты құрылғымен жабдықталған. Түйісуді вулканизациялау және оны суыту кезінде престен 1,5 м кем болмайтындай қашықтықта түзу орналасуы тиіс, бұл ең алдымен лентадағы көлденең жарғыншақтың қалыптасуын алдын алу үшін қажет. Қазіргі таңда Б-820 мақта-мата тоқымасы негіздегі ленталарды вулканизациялаудың суық әдісі жете зерттелініп жетістікті енгізілуде.
Машиналар мен жабдықтарды жөндеудің технологиялық процессі. Жөндеу операциялары
Жөндеу технологиясы ретінде жабдықтың техникалық ресурсын қалпына келтіру бойынша орындалатын жөндеу жұмыстарын белгілі реттілікпенен орындаудың техникалық тәсілін түсінуге болады.
Жалпы жағдайда жабдықты жөндеудің технологиялық процесі келесі реттілікте орындалады: 1) жабдықты жөндеуге дайындау; 2) жабдықты жинақ бірліктер мен бөлшектерге бөлшектеу; 3) жинақ бірліктер мен бөлшектерді тазалау және жуу; 4) тозған және ақау бөлшектер мен жинақ бірліктерді қалпына келтіру және ауыстыру; 5) бөлшектерді бақылау, ақаулыққа тексеру және сұрыптау; 6) машиналар мен аппараттарды құрастыру; 7) жабдықты сынау және бақылау;
Жабдықты жинақ бірліктерге бөлшектеу жабдықты құраушы бөліктердің біртұтастығын және жөндеуге қолжетімділігін сақтай отырып келесі операциялардың келесі операциялардың кешенді орындалуымен жүреді: 1) бөлшектер мен түйіндерді көтеру және жылжыту; 2) бұрандалы және престік қосылыстарды бөлшектеуменен және де түйіндік және бөлшектік ақаулыққа тексеру.
Ауыр салмақты түйіндер мен бөлшектерді көтеру және жылжыту үшін түрлі көтеру-тасымалдау құрылғылары мен механизмдерін қолданады: крандар (мұсылы, көпіршектік және оқшаулы), талдар, тельдерлер және кран-балкалар. Бөлшектеу барысында такеллаждық аспаптар мен құрылғылардың жарамадылық және жұмысқабілеттік күйін тексеру қажет.
Машиналар мен жабдықтарды бөлшектеу барысында штирттері болмаған түйіндер мен бөлшектердің өзара орналасу жағдайын белгі соғу, болу жағу және таңбалауменен белгілеп алу қажет. Жанасатын металл бұйымдарда белгі соғу үшін электрокарандаштарды да қолданады.
Бұл жөндеуден құрастыру барысында жанасатын бөліктердің үйкелісінен жағдайын орнықтыру,осының нәтижесінде өңдеп келтіру жұмыстарын орындалуға мүмкіндік береді.
Бөлшектеуден соң түйіндер мен бөлшектерді ластардан тазартады. Жуып тазартудан алдын бөлшектерді қаттардан, ластар мен майлардан тазартады. Қаттардан механикалық немесе химиялық тәсілмен тазартады. Химиялық тазарту тәсіліндежиі 1 л суға 24 гкаустикалық соданы, 35 г канциленген соданы, 1,5 г сұйық шыны және 25 г сұйық сабын аралыстырылған ерітіндіні қолданады. Жуу ұсақталған ерітінді температурасы 80÷90 °С жағдайда 23 сағ созылады.
Май мен ластардан аппаратураны тазалау үшін керосинді және содалық ерітіндіні буменен бірге беруді қолданады. Бұл кезде соданың ерітіндісі маймен бірге жеңіл шайылатын майлы эмульсияны түзеді.
Аппаратураны қатты шөгінділерден тазартуды коррозия ингибитарларын араластыра отырып, 5 % тұз қышқылы ерітіндісінде атқарады.
Бөлшектеу барысында жылжымайтын ажырамалы қосылыстарда бөлшектеу мәселесін орындау қажет.Жылжымайтын ажырамалы қосылыстарды ажыратуда ажыратқыштарды, пресстерді және гидравликалық тәсілдерді қолданады. Бөлшектерді кері престеу барысында керіпрестеуге қажетті күшті әлсіретуді үшін қамтушы бөлшекті қыздыру немесе қамтылушы бөлшекті суыту технологиялық амалдарды қолданады.
Бөлшекті қыздыруды май ваннасында батырумен немесе майды бөлшеккке құюменен орындайды. Бөлшекті суыту үшін құрғақ мұзды (-78 °С температурадағы) немесе сұйық азотта (-196 °С температурадағы) атқарады.
Престеу (керіпрестеу) үшін қажетті күшті жуықша келесі эмпирикалық өрнекпен есептеп алады:
P = 20 δ l
Мұнда δ – сығылым, мин; l –престеп отырғызу ұзындығы, мм:
Кез-келген бөлшекті құрастыру бөлшектеуге кері реттілікті жүреді. Құрастыру барысында бұл реттілікті сақтаумен қатар бөлшектің өзара орналасу жағдайын бақылауда орындау қажет.
Жөндеуден кейінгі құрастыру, жаңа бөлшекті құрастыруға келесі топтағы бөлшектердің келіп түсуіменен ерекшеленеді: 1) мүмкін шама шегінде тозған, бірақ жөндеу операциясының қайта пайдалануға болатын бөлшектер; 2) қалпына келтірлген бөлшектер 3) жаңа бөлшектер. Осы себепті құрастыру слесарлық жұмыстарды қолданумен жүреді.
Конустық роликті подшипниктерді, радиал-тіректі шарикподшипнтктерді және басқа да ұқсас құрылғыларды құрастыруда, реттеп кейбіреуін мүмкіндігі болатындай жағдай қамсыздануы қажет.
Біліктерді құрастыру барысында келесі операциялар орындалады: салынған белгілер мен өлшемдер бойынша біліктерді орнықтыру; біліктің горизонталдылығы мен вертикалдылығын, параллельдігін, өзара перпендикулярлығын және остестігін тексеру.
Тісті берілістің құрастырылуы келесі операциялардың орындалуын қарастырырады: 1) біліктердің өзара орналасуын, тісті доңғалақтың отырғызылуы мен бекітілуін тексеру; 2) қажетті радиал және бүйірлік саңылаулықтың қамтамасыздалуын; 3) тістердің жұмысқа беттерінің жанасуын тексеру;
Червякты берілістерді құрастыру барысында червяктың доңғалақ тістеріменен бірігуінің дұрыстығына назар аудару қажет. Бұл кезде тісті доңғалақтың орташа жазықтығы червяк осіменен сай келуі тиіс, централдық қашықтық сызбаға дәл сай келуі тиіс, бүйірлік саңылаулық ілігуде техникалық талаптарға сай келуі.
Белбеулі берілісті құрастыру подшипниктердің, біліктердің, остердің өзара орналасу жағдайын және белбеулердің ілінуін орнықтыру, тексеру және түзетумен жүреді.
Шпонкалық қосылыстарды құрастыру келесі талаптарды қанағаттандыруы қажет: 1) аршықтың кең қырына сыналы шпонканың жатысуы бүкіл ұзындығында біркелкі болуы тиіс, ал шпонканың бүршігі шығыңқы жағдайда керітпештің 0,8-1,0 шпонка биіктігінен аспайтындай қашықтықта орнатылуы тиіс: 2) призмалық шпонкалы қосылыста ешқандай тербеліс пен ығысу болмауы тиіс: 3) жылжымалы шпонканың жергілікті ығысуы мен сыналауын бағдарлау қажет.
Жылжымалы және жылжымайтын шлицалық қосылыстарды құрастыру барысында қолмен айналдырғандағы айналу моментінің әсерінен болатын "сығылу" мен "тербеліске" бақылау жасау керек.
Айналу бөлшектерін тепе-теңгеру. Тепе-теңгеру айналу бөлшектерін қалпына келтірудің спецификалық тәсілі болып табылады. Бұл кезде олардың тозу және жөндеуден кейінгі жоғалған тепе-теңсіздігін алдымен статикалық , сонан соң динамикалық қалпына келтіреді. Сонымен қатар, тепе-теңсіздік бұрыс құрастырудың нәтижесі болып табылады. Статикалық немесе динамикалық тепе-теңгеруді қолдану шегін анықтайтын факторлар, бұл бөлшек ұзындығының қатынасы L/D мен айналу жиілігі n. Іс жүзінде, жиі аралас тепе-теңсіздік кездеседі. Бұл кезде ең алдымен қорытынды күшті азайту үшін статикалық тепе-теңгеруді, сонан соң динамикалық тепе-теңгеруді қолданады.
1 сурет. Статикалық және динамикалық тепе-теңгерулер шекарасы.
I – статикалық тепе-теңгеру аумағы; II – аралық аумақ; III – динамикалық тепе-теңгеру аумағы;
Бөлшектерді бақылау және ақауға тексеру. Жабдықты бөлшектеу процесінде ұштасып ақаулыққа тексеруді қолданады. Ақаулыққа тексеру ақау ведомстін түзу және ақау бөлшектерінің схемасы мен нобайын түзумен аяқталады. Алдын ала ақаулыққа тексеру жабдықты жөндеуге тоқтатар алуан орындайды. Алдын ала ақауға тексеруде машинаның нақты функционалдық көрсеткіштерін қадағалайды – үйкелісу тораптарының қызу температурасын, дірілдің, соққының болуын және соққының шыстын және т.б.
Түйінді ақауға тексеруде түйіннің берілген өзара орналасу жағдайынан ауытқуын, нақты техникалық күшін тексереді. Бөлшектік ақауға тексеруде қайта қолданудың мүмкіндігі мен талап етілген жөндеу сипатын анықтау орындалады. Сонымен қатар бөлшектерді келесі топтарға сұрыптайды:
1) Тозу шамасы өлшем шегінде және қайта қолдануға жарамды бөлшектер;
2) Тозу шамасы өлшем шегінен асқан және жөндеуге жарамды бөлшектер;
3) Тозу шамасы өлшем шегінен асқан және жөндеуге жарамсыз бөлшектер;
Бөлшек күйін анықтау үшін сырттай бақылауды, өлшеуді, мондай-ақ жасырын ақауларды анықтауа мүмкіндік беретін әдістерді қолданады – магниттік және ультрадыбыстық ақау көшіруді, рентгенграфияны және т.б.
Сынау
Машиналар мен жабдықтарды жөндеу процесінің аяқтаушы кезеңі, бұл беріктікке және тығыздыққа сынау, бос жүріс және жұмысшы тәртіпте түсірумен сынау.
Ри шамасы беріктікке сынау барысында жұмыс қысымына және температураға тәуелді. Беріктікке сынау пневматикалық және гидравликалық тәсілдермен жүреді. Рр≥0,5 Мпа қысымда жұмыс істейтін аппараттар үшін бақылау қысымының шамасын 1,25 Рр құрайды.
Тығыздыққа сынауды жанғыш, жарылысқауіпті және улы заттарменен жұмыс істейтін аппараттар үшін орындайды. Тығыздыққа сынауды ауа немесе инертті газ көмегімен орындайды.
Жабдық қаңқаларын жөндеу. Қаңқалық бөлшектерді жөндеу
Қаңқалық бөлшектерге машиналар мен аппараттардың базалық бөлшектері жатады – қабықтар мен станинаналар.
Алуан түрлі қаңқалық бөлшек типтерін ортақ тән тозу түрлері, бұл:
1) жарғыншақ, сынық, майысу түріндегі механикалық жарақаттар, сонымен қатар бұрандалы саңылаулардағы шпилка сынықтары;
2) подшипниктер мен толкелер отырғызылу беттердің, бұранданың және бос отырғызылған беттердің тозуы;
3) жиналушы іргелес беттердің майысқақтануы, саңылау өстерінің өзара орналасу жағдайының айнуы;
4) қабырға қалыңдығының жергілікті тозуы түріндегі коррозиялық тозуы
5) аптама қабаттың қабықталуы және ісінуі;
6) коррозиялық жарғыншақталуы және де сырт көзбен анықталмайтын корорзия түрлері.
Қаңқалар конструкциясы бойынша пісірілмелі және құйма болып түрленеді. Химия өнеркәсібі кәсіпорындарында қолданылатын жабдықтар қаңқаларының басым көпшілігі көміртекті болаттардан дайындалады да, ортаның агрессивтілік әсерінен қорғау үшін ішкі бетінен агрессивті әсерлерге төзімді металлдық және бейметалдық материалдарменен апталады – футеровкаланады. Бейметалдық аптамалар бейорганикалық және органикалық негізде болуы мүмкін.
Қаңқалық бөлшектерді жөндеу ақаулық ведолятіні талдаудан және оны пысықтаудан басталады. Қаңқалық бөлшектердегі жарғыншақтар мен қаңқа қалыңдығының коррозиялық әсерден жергілікті жұқаруы пісіріп бітеу және пісіріп жапсарлауменен қалпына келтіріледі. Қаңқада кездесетін мұндай жарақаттарды қалпына келтіру келесідегідей атқарылады.
Қабырға қалыңдығы жергілікті жұқарған жағдайда, ақау болған орындар таза металға дейін механикалық және жолынды тәсілдермен өңделеді. Өн бойына өткен жарғыншақтар болған жағдайда жарғыншақтар өңделіп жасақталады.
Жарақаттанған участкелер горизантал жағдайда 300-3500 С температураға дейін қыздырылады, сонан соң пісіп жапсарланады. Пісіріп жапсарлау тәртібі мен тәсілі электрод маркасы мен диаметріне және бұйым материалына тәуелді болады. Пісіру жұмыстары аяқталғаннан соң жоғары (отпуск) ............. тәртібінде жедел термоөңдеу орындалады. Қыздыру 650-6800С дейін орындалады да, температурада ұстау жапсарланған қабаттың 1мм қалыңдығында 7 ман есеппенен жүреді. Термоөңдеуді кішігаборитті газ пешінде орындайды. Пеш бір орнатылуда 3 м ұзындықтағы қаңқа участкесін термоөңдей алады.
Мемкентехбақылауға құзырлы емесе аппарат қаңқасының ақаулық участкесін жөндеу, бұл ақау орындарды ойып алып орнына жаңа элемент пісіруменен орындалады. Ойық пішіні дөңгелек, овал, эллипстік немесе бұрыштары 50 мм кем болмайтындай радиуста дөөңгелетілген тікбұрышты болуы мүмкін. Ойылатын участке ені 250 мм кем болмауы тиіс. Жаңа элементтер түйістіріліп пісіріледі.
Ішкі беті өзара сақиналы және ұзына бойғы жіктермен пісіріліп, табақшалардан кептірілген қорғасын, мыс, титан, қышқылтөзімді болаттан жасалған футеровкаларды жөндеу жарақаттанған футеровкалық табақшаларды алып тастап жаңасыменне ауыстыру арқылы жүреді. Жұмысты орындау үшін аппаратты люктер мен паздар болуы тиіс.
Бұл кезде ескі және жаңа футеровкалардың қырларын дайындау келесі тәсілдерменен жүреді. Ескі футеровка қыры технологиялық мұртшаны алу мақсатында жасақталады (1 сур.). Мұртша ұзындығы 5 мм және қалыңдығы 1 мм кем болмауы тиіс. Технологиялық мұртша жаңа футеровканы пісіру кезінде астар толық ролін атқарады.
Орнатылушы футеровка қаңқаға және ескі футеровкаға кергіш винт көмегімен тығыз тақалады. Осылайша жаңа футеровкалар астар жолақта және технологиялық мұртша пісіріледі. Астарсыз жіктер бағанадан тыс пісіріледі. Футеровканы жөндеу аспалы алаңдарды қолдануменен жүреді. Жөндеуден соң пісіру жіктері түсті ақау көшіруменен тексеріледі және 105ПА қысымда керосинменен опресовкаланады.
Сонымен қатар кірпіш, плиташалар, фасонды бөлшектер, цемент, бетон түсіндегі бейорганикалық футеровкаларды қолданады.
Ұзақ мерзімді пайдалану барысында бейорганикалық материалдардан жасалған футеровканың күйреуі, қаңқа материалы мен футеровканың сызықтың ұлғаюының түрлі коэфициенттерінің болуы салдарынан болатын күнеу нәтижесінде орын алады. Ақау болған участкені жөндеу негізгі футеровка мен астар төсемді таза болатқа дейін алып тастап жаңасы менен ауыстыру арқылы жүреді.
Футеровканы толық ауыстыру барысында, оны аппараты монтаждағандағыдай келтіреді. Футеровкалау процесі аппарат беті мен футеровкалау материалын дайындау, тікелей футеровкалау операциясы мен кептіруден тұрады. Футеровканы кептіру температураны берте-бірте көтеруменен жүреді. Футеровкаланған аппаратты сынау жұмыс қысымына тең байқау қысымында жүреді.
Футеровкалауда астар қабат ретінде полиазобутиленді қолданады.
Тік аппаратты толық футеровкалау барысында ең алдымен түпті футеровкалайды, сонан соң сатылар мен аспалдақтарды орнатып цилиндрлік бөлігін футеровкалайды, сонан соң ғана опалубка немесе шатырша көмегіменен қақпақты футеровкалайды. Цилиндрлік горизантал аппараттарды ең алдымен түптері футеровкаланады, сонан соң төменгі бөлігі футеровкаланады, байланыстырушы құрам қатқаннан соң ғана қабықтың жоғарғы бөлігі футеровкаланады.
Ыстық төзімді төсемдердегі жарғыншақтар мен сынықтар жарақат орындарды сұйық шынымен малу арқылы дайындап алып ыстыққа төзімді бетонмен жапсарланады.
Атап өтетін жағдай, аппарат қаңқасындағы келтеқұбыр, люктер, термопаралар, приборлар үшін саңылаулар футеровканың моножиттілігін (біртұтастылығын) бұзады, тозуға қарқынды ұшырайды, футеровкалау барысындла едәуір күрделіліктер туындайды. Сондықтан да футеровкалау жұмыстары басталар алдын келтеқұбырларға владыштер орнатады. (2 сурет). Фартугі бар вкладыштер аппартқа тұтас жікпенен пісіріледі. Тастан құйма, пластмассалық немесе графиттік вкладыштер сұйық жақпаға малынған асбестік бауменен расчиканкаланады.
Қаңқалық бөлшектердегі конструктивті элементтердің бірі, бұл, келтеқұбыр. Келтеқұбырлар мен люктер аптама қабатты балқымақабаттаумен, жаңа келтеқұбырды орнатуменен – күшейту сақинасын ауыстыру және ауыстырусыз; сондай-ақ келтеқұбырды қауыздауменен (фланецті және фланецсіз)
Қауыздар келтеқұбырға екі ұшынан да пісіріледі. Пісіру жігінің тығыздығын гидравликалық сынауменен тексереді. Келтеқұбыр денесінде екі М10 бұрандалы саңылау ойылады. Бұл саңлаулар арқылы пайдалану барысында пісіру жігінің жағдайлары қадағаланады. Бұрандалы саңылауларға газдыың өтуін тексеру келтеқұбырлары бұралып орнатылады.
Бейқаңқалық бөлшектерді жөндеу.
Бейқаңқалық бөлшектердің қатарына біліктерді, подшипниктерді, шестерняларды, муфталарды, шлициялық элементтерді жатқызуға болады.
Біліктерді жөндеу барысында тозған беттері мен бет элементтерді, иілген бөліктерді түзету бойынша жұмыстар орындалады.
Тозған білік мойынын механикалық өңдеумен, балқыма қабаттаумен және металдаумен қалпына келтіреді.
Біліктерді түзету келесі тәсілдердің біріменен орындалады: 1) механикалық тәсілмен, елеусіз өлшемдегі бірліктерүшін қолданылады; 2) термиялық әдіспен, елеусіз иілу шамасындағы және шынықтырылмаған біліктер үшін үшін жарамды; 3) термомеханикалық тәсіл, механикалық түзетуге дейінгі және онан кейінгі жалпы және жергілікті күйдіруменен орындалады.
Түзетудің термиялық әдісі, біліктің дөңес учаскесін жылдам жергілікті қолдаумен жүреді. Бұл кезде біліктің қызған металл қабатында аққыштық шегінен жоғары кернеулік орын алады. Қыздырылуға тиісті участкенің өкшелі иілу шамасыменен анықталады. Білік асбесттік қабатпен қапталып, қыздыру терезесі ойылады. Қыздыру газдың пісіру оттығымен жүреді. Қыздыру температурасы 600-700 ºC дейін жетеді (болат күңгірт ших түске енгенге дейін). Қалдық иілу шамасы білік ұшының кескін бетінде орнатылған индекстердің көмегімен, толық суытылғаннан соң анықталады. Қажет болған жағдайда бірнеше рет қайталануы мүмкін. Түзету түзетілуші білік участкесінде кері иілу шамасы 0,10 ÷ 0,15 мм жеткенге дейін жүреді. Бұл кері иілу шамасы білікті түзетуден кейінгі күйдіруменен қалыпқа келтіріледі.
Подшипниктерді жөндеу. Сырғанақ подшипниктерді жөндеу қажеттілігі келесі жарамсыздықтан туындайды: 1) үйкелісу бетінде шырықтар мен сызаттардың болуы; 2) үйкелісу бетінің алғашқы геометриялық пішінінің бұрмалануы; 3) баббиттің жергілікті немесе толықтай дерлік еруі не қабатталуы; 4) жарғыншақтың орын алуы;
Сырғанақ подшипниктер конструкциясы бойынша ажырамалы және тұтас болады. Тұтас сырғанақ подшипникті жөндеу барысында саңылаудың ішкі бетін қашау немесе балқымақабаттан сонан соң жаңа төлкені престеп отырғызу үшін қашау жұмыстары орындалады.
Вкладыш елеулі тозғанда немесе баббиттік қабат қат-қатталғанда, оларды қайта құяды. Қайта құю келесі операциялардан тұрады: 1) Подшипникті жөндеуге даярлау; 2) подшипникті қалайылау; 3) баббитті құюға даярлау; 4) подшипникті құю; 5) өңдеу және тексеру.
Дайындау операциясында бұйымды ластардан, майдан және коррозия іздерінен тазалау, подшипник вкладышынан тозған баббит қабатын ерітіп алу жұмыстары орындалады.
Тозған баббиттік қабатты еріту операциясы подшипниктің тік орнатылуында артқа бетінен 240-260 ºC дейін газ оттығымен немесе ұйытқыш калмамен қыздыру арқылы жүреді.
Сонан соң вкладышты 10-15 % тұз немесе күкірт қышқылдарының көмегімен бөлме температурасында 20-10 мин уақыт жалаң қабаттау операциясы орындалады.
Қалайылау процесі баббит маркасына байлансыты. Б83 баббит үшін таза қалайыны қолданады. Баббитттік қабатты қолмен,
центрден тебу тәсілімен және қысыммен құяды.
Құйылуға тиісті қабат қалыңдығы төмендегідей анықталады:
δδ = k · 0,05d
мұнда δδ – құйылған подшипникті қисығанысы кейнгі баббиттік қабат қалыңдығы; k – қашауға қор коэффициенті, k = 1,03÷1,05; d – білік мойны диаметрі;
Құйылған подшипник суығаннан соң тексеруге беріледі. Баббитті қабаттың беті тегіс және күміс түсті болуы керек. Баббиттің подшипник бетінде тығыз жаттасуы балғаның соғылуымен тексереді.
Құйылған вкладышта майлау канавкалары фрезерленіп, май саңылауы бұрғыланады. Соңынан шаберлеу жүреді.
Шестерняларды жөндеу. Шестерняларды жөндеу ондағы келесі жарамсыздықтарды қалпына келтірумен жүреді: тістің ұзындығы мен қалыңдығы бойынша тозуы, тістің сатылы қажалуы, тістің целентацияланған және шынықтырылағн жұмысшы беттерінің үгітілуі, тістерінің сынуы, шпонка сайының тозуы. Жөндеу тозу шамасы мен сипатын анықтаудан басталады.
Ақау шамасын және сипатын анықтау келесі конструктивті параметрлерді тексерумен жүреді: штангенциркульмен тістің ұзындығының тозуын тексереді де, ал қалыңдығын бастапқы шеңберімен штангензуболерменен тексереді; шпонканың және шлицаның бер элементтерінің тозуын скобалармен, табақшалы тығын немесе шаблонмен тексереді. Қалған жарамсыздықтар сырт көзбен тексеру арқылы анықталады. Шестерня тісінің тозуын бақылау скобасымен тексереді. Егерде скоба тіс жотасында тығыз отырса, онда шестерня жарамсыз деп танылады.
Сынған тісі бар шестерняны келесі тәсілдердің біріменен қалпына келтіреді: 1) тісті винтте өзгертумен; 2) тісті пісірумен; 3) тісті "қарлығаш құйрығы" етіп орнатумен.
Шлицалық бет элементтерін жөндеу жұмысшы елес қырларында балқымақабаттаумен, ескі шлицаларды пісіріп беттеп, жаңа шлица оюмен, және де тісті жайып пісіруменнен жүреді
Машиналар типтік түйіндерін жөндеу. Білікті жөндеу
Біліктердегі бір шама кездесетін ақаулар бұл, оның майысуы, сынуы және де бұранда мен отырғызылушы беттерінің тозуы. Білігі бар аппараттарда сонымен катар, келесі тозу түрлері кездеседі: сальниктердің істен шығуы және т.б. бірқатар жарақаттар.
Біліктердің майысуы подшипниктердін істеншығыуының нәтижесінде немесе айналатын бөлшектердің айналмайтын бөліктерге қажалуының нәтижесінде болады. Бұл кезде білік деформацияланады.
Ақауды, айналатын бөлшекті токарь станогында кажет санылаулықты қамтамасыз ету үшін жонумен калпына келтірелі. Сондай-ақ елеулі және үздіксіз дірілдердің пайда болуы біліктің иілуіне алып келеді.
Білік мойнының тозуы, әдетте, тіректік подшипниктердің істен шығуының нәтижесінде. сондай-ақ коррозиялық жарақаттардың, сызаттар мен подшипниктік сынаны майлау
майымен келген бөгде қатты түйіршектерінің іздері калыптасудың нәтижесінде болады. Сырғанау подшипниктсрінде жұмыс істейтін білік мойны, көп жағдайда бір калыпты желінбейді. ұзына бойғы кимада конустықты қабылдайды, ал көлденең қимасы-эллипс тәрізді пішін калыптасады.
Тербелмелі подшипниктерде жүмыс істейтін білік мойны, дайындау процесіндегі отырғызылудың әлсіреуінің немесе жұмыстык пайдалану процeсінде қажалуының салдарынан болады.
Бұранданың тозуы-әдетте, ыстық ортаны тасымалдаушы насостардың білігіндегі қорғағыш қауызбен жанасу орындарында байқалады. Мұның себебі бұл, оны кұрастыру барысында майлау майымен граннтті араластырып майланбағандықтан болады.
Біліктің сынуы, әдетте, бір диаметр екінші диаметрге өтер жерлерде болады және де онда кернеулердің жергілікті шоғырлануымен түсіндіреді, атап айтқанда артық күш әсері кезінде. Біліктің сынуы әдетте оның майысуының салдары болыптабылады.
Біліктерді тексеру және жөндеу. Білікті сыналуға тексеру агрегаттың толық бөлшектеу мен жүреді, бөлшектеуді кажеттігінің себебінсіз.
Тексеру жұмыстарын бастар алдын, біліктің кескін беттеріндегі және де оның геометриялык өсімен сәйкес келетін, центірлік саңылаулардың болуын тексереді.
Саңылаудағы елеусіз жарқаттарды егеумен тазалайды. Токарь станогы центірінің саңылаудың конустық белдгіне жағысуын бұзатын ақауларды арнайы центрлеуші бұрғының көмегімен қалпына келтіреді. Ал егерде жөнделуші біліктеценрлеуші саңылау болмаған жағдайда немесе соңғысы қатты жарақаттанған болса, онда оны жаңадан бұрғалап ояды. Бұл үшін біліктің бір ұшын төрт кұлакшалы токарь патронында, ал екінші ұшын люнетке орнатады. Орнатудың дұрыстығын сағат типтіиндикатордың көмегімен білік беті бойынша тексереді, және де бұл бет мүмкіндігінше алшақ, сондай-ақ жұмыстық қолданылу кезінде тозуға ұшырамайтын бет болуы тиіс (мысалы үшін, қорғаушы кауыз орнатылатын бет және отырғызылушы беттерден баска беттер).
Білікті соғылуға, токарь станогынын центрінде немесе арнаулы аспаптарда жүргізеді. Білік мойнының радиустік соғылуын сағат типті индикатордың көмегімен жүргізеді. Соғылудың мүмкін шамасы, біліктің тағайындалуына, оның айналу жылдамдығына және басқа да факторларға байланысты болады. Индикатор станок суппортында орнатылады.
Төменде ортадан тепкіш насосының білігі үшін соғылудың мүмкін шамалары келтірілген, мм.
Подшипникті отырғызуга болатын білік мойны - 0,02 - 0,025 аралық тірек үшін білік мойны - 0,05 дейін, жартылай муфта, отырғызылушы беттер - 0,03-0,05, қорғағыш қауыз отырғызылушы беттер - 0,03-0,04, жұмысшы доңғалағы отырғызылатын беттер - 0,04-0,05.
Егерде саңылауының шамасы мүмкін шамадан асып кететін болса, онда білік түзетуге берілуі тиіс.
Біліктің тузетілуі кіші диаметрдегі бітіктер үшін (70 мм-ге дейінгі) колданылатын түзетудің карапайым тәсілі бұл, механикалық тузету. Негізінен механикалық түзетудің екі әдісі бар:
1. токарь станогында немесе арнаулы аспапта: білік өсін майысқан тұсқа қарама-қарсы тұсқа июмен.
2. соғу әдісімен.
Бірінші әдісте білікті түзетілуі винттің басқышпен, домкратпен, немесе ұқсас аспаппен жүзеге асырылады. Түзету үшін білікті 1 иілуін жоғары каратып, кармағыштардың 2 және шпильканың 3 көмегімен оны траверске бекітеді. Карамағыштардың арақашықтығы біліктің иілген учаскесіне сәйкес келеді. Винт 5 өзінің табанымен білікке тіреледі. Білік беті жарақаттанбау үшін қызыл мыстан қорғағыштар мен басқыш винттің табанына корғаушы төсем төсейді. Июді түзетуді, әсер етуші күші, серпімділік шегінен асатынкернеуді тудыратын шамаға дейін өсірумен жүргізеді. Түзетуді, 0,05-0,10 мм сәйкес келетін бір шама кері иілуі қамтамасыз ете отырып аяқтайды.
Үлкен диаметрдегі білікті соққылау және бір мезгілде механикалық күш түсірумен түзетеді. Майыскан жағын У-8, У-7 кұрышынан дайындалған арнайы кұралдың көмегімен соққылап түзетеді. 10-20 соққыдан соң соғылуын тексереді (дәл сол қимада). Түзетуді, білікмайысуына карсы майысу шамасы 0,05 мм жеткенде тоқтатады (соғылуы бойынша). Түзету толық аяқталған соң соғылған орындарын егеумен егейді не болмаса зімпара жолағымен тазартады.
Үлкен диаметрдегі (150 м.м және онан жоғары) білік үшін таза түрдегі термиялық әдісі немесе оны механикалық күш түсірумен киыстырылған түрде қолданады.
Түзету процесінде соғылулы үздіксіз бакылау мүмкіндігін қарастыра отырып, білікті центрде немесе подшипинкте орнатамыз. Кыздыру орнын (максимал иілуге ұшыраған орынға, қарама-қарсы майысқан өсінің дөңес бөлігінде) ылғал асбесті табағы мен жауып, онда терезе ояды. (1 сурет). Түзету жерін (терезеге бағыттап) 6 немесе 7 гарелкамсн (оттықпен) қыздырады. 4-10 минут ішінде температураны 550-650 °С-ге дейін бірте-бірте жеткізеді (күңгірт шие немесе шие түсуі пайда болғанға дейін). Сонан соң қыздырылған терезені жауып,толық суытылуын күтеді және де соғылуын тексереді. Түзету толық аяқталған соң, кыздырылған орынды күйдіру қажет.
Біліктің отырғызылу орындарын қалпына келтіру. Білік мойыны тозған кезде (сырғанау подшипнигінде жұмыс істейді), мойнын токарь станогында жонып сонан соң ажарлайды (егерде, бет шынықтырылған болса).
Кей жағдайларда, егеумен егеп (егеумен) және де майда дәнді зімпара жолағы көмегімен қолмен ажарлайды, сондай-ақ гой пастасын колдануымен.
Сырғанау подшипнигінің істен шығыуының нәтижесіндс орын алған біліктің қатты тозуын немесе тербелмелі подшипникте жұмыс істейтін білік мойнының елеусіз тозуын, сондай-ақ басқада отырғызылу орындарының алғаш өлшемдерін калпына келтіру талапетіледі. Жөндеу базасы жағдайында тозу дәрежесіне байланысты тозған болшектерді қалпына келтірудің келесі әдістерін колданады:
1. Электролиттік хромдау, тозу шамасы 0,03 мм.
2. Электорлиттік темірлеу, тозу дәрежесі 1,5 – 2 мм дейінгі жағдайда.
3. Автоматта дірілді доғалы балқыма қабат төсеу, 5 мм дейінгі тозу дәрежесінде.
4. Қолмен атқарылатын газды балқыма қабат төсеу, 4 мм дейінгі тозу шамасында.
5. Болаттау, 10-15 мм дейінгі тозу дәрежесінде (әдіс, тұрақты және елеусіз жүктемелер шамасы бойынша қолданады).
6. Қолмен атқарылатын электр доғалы балқыма қабат төсеу, 5 мм дейінгі тозу барысында.
Бұл әдістердің технологиялық әдістері алдын қарастырылған
Шпонкалық қосылыстарды жөндеу
Өнеркәсіпте жабдық конструкцияларында негізінен призма және сегментті шпонкалар колданылады. Шпонкалық қосылыстың жұмыс кабілеттілігінің негізгі критерийі, бұл олардың беріктігі.
Шпонкалық косылыстардың жұмысшы беті, ол олардың бүйірлік беттері. Ұзақ мерзімді жұмыс істеу процесінде бұл беттер тозады және жұмсақ деформацияға ұшырайды — майысады. Сегментті шпонка, мүмкін кернеулік жағдайдан артық кернеулік пайда болғанда әдетте киылады,
Шпонкалық паздар үшін тозудың келесі мүмкін шекті шамалары орнатылған: шпонкалық паз ені 10 мм дейін болғанда тозу шамасы 0,1 мм; егерде 10 — 20 мм болғанда — 0,15 мм; паз ені 21 мм-ден — 26 мм дейін болғанда — 0,19 мм.
Тозу дәрежесін калибр — шаблонмен, штангенциркульмен немесе микрометрмен аныктайды. Тозуға ұшыраған шпонкалық паздарды, алғаш өндегенде балқыма кабат төсеумен қалпына келтіреді. Бұл кезде балқыма қабатты бір шама аз жүктелген кабырғаға төсеу тиімді.
Шпонкалық паздың балқыма кабат төселмеген кабырғасьның негізгі болаты балқыма кабат төселгенге карағанда үлкен беріктікке ие. Балқыма кабат төсеудің технологлясы мен тәртібі және де колданылушы жабдықтары алдыңғы тарауларда қарастырылады.
Шпонкалық паздың елеулі тозуы кезінде, яғни бір жағынан балқыма қабат төсеп қалпына келтірудің мүмкіндігі болмаған кезде, паз толығымен балқыма қабат төселіп бітеледі де сонан соң жаңа орында (90° немесс 180° бұрышпен) шпонкалық паз фрезрленеді.
Керітпештегі паздар соққылаумен немесе тартқылаумен орындаіады. ал бсііісгерде - үршықты фрезрмен немесе дискалы фрезрмен фрезрлеумен. сондаіі-ақ токарлік тәсілмен ояды.
Көпшілік жағдайларда шпонкалық паздар жаңа өлшемге өңделеді (үлкен өлшемге). Жинау барысыңда жаңа, біршама енді шпонканы орнатады. Жөндеу барысында шпонкалық паздың қатттығы онын енінің өлшем шегінің 0.5 аспауы тиіс. Шпонкалык паздын түпкілікті енін егеумен (шабровка) келтіреді.
Машиналардың типтік түйіндерін жөндеу. Шлицалық қосылысты жөндеу
Шлицалық қосылыстардың кең таралғандығын түсіндіретін негізгі жетістігі бұл, жоғарғы дәрежедегі алып жүрушілік қасиеті; жұмыс сенімділігі мен техно-логиялығы; жеңіл жиналуы.
Ең көп таралған шлицалық қосылыс түрі бұл, түзу бүйірлі шпонкалар (тұрақты көлденең қимасы бар түзу бұрышты шлицалар). Шлицалық қосылыс бөлшектері әдетте құрамында 0,12 ден 0,455 дейінгі көміртегі бар құрыштардан дайындалады. Әдетте, шлица беттері термиялық өңделеді (цементациялау). Термиялық өңдеулердің түрі бөлшектің тағайындалуына байланысты болады.
Жабдықты ұзақ мерзімді жұмысқа пайдалану процесінде шлицалық қосылыстар тозуға ұшырайды. Тозуға басты себебі бұл, өстік және радиустік бағыттағы шпонкалардың жұмысшы беттерінің сырғанауы. Тозу процесін екі кезеңнен бөлуге болады: 1) Жұмыстық үйренусілік тозу; 2) Шлицалардың жанасушы беттерінің, жұмыс процесінде олардың салыстырмалы радиустік және өстік қозғалысының нәтижесі ретіндегі тозуы.
Шлицалық қосылыстардың тозуы нәтижесінде келесі жарамсыздықтар болуы мүмкін: 1) Шлицалардың майысуы немесе қиылуы; 2) Материалдың шаршау себебінен шлицалардың сынуы.
Өндірістегі тәжірибе көрсетіп отырғандай, яғни статистикалық мәліметтерге анализ жасайтын болсақ, онда шлицалық қосылыстардың бірте-бірте тозатындығына көз жеткізуге болады. Ең жоғарғы күш әсерінің моментінде шлицалар қиылуға ұшырайды (алдын ала тозудың нәтижесінде әлсіреген).
Шлицалардың тозуы жұмыс істейтін түйінде жарамсыздықтар тудырады. Мұндай жарамсыздықтардың негізгі түрлері, бұл;
- Жетектің айналу бағытын ауыстырған кездегі соққылар. Бүйірлік саңылаулық шамасы, шлицаның қалыңдығымен (енімен) барабарлығымен түсіндіреді.
- Отырғызылған бөлшектердің қиғаштығы және осы қиғаштықтың салдары (шестерня тістерінің сынуы, біліктің фланецтік және басқа да ұшпаұш қосылыстарының қирауы).
- Керітпештің кескін бетінің тозу салдарынан болатын білікке отырғызылған бөлшектердің өс бойындағы ығысуы (жылжып кетуі).
Шлицаларды қалпына келтіру әдістері тозуының дәрежесіне байланысты. Біліктегі шлицалардың елеусіз тозуы кезінде олардың жұмсақ деформациялаумен жөндейді (бүкіл ұзындығы бойында жан-жаққа ығыстыруы). Шынықтырылған шлицаларды мұндай әдіспен жөндер алдын күйдіреді. Жөндеуден соң термиялық өңдеуге береді. Соңғы операция, бұл кезде, нақты өлшемге өңдеу (әдетте, ажарлауды қолданады).
Белбеулі және шынжырлы беріліс элеметтерін жөндеу
Белбеулі беріліс элементі бұл, иілгіш белбеумен қамтылған екі немесе бірнеше шкифтер. Технологиялық жабдықтарда кең таралған белбеулі беріліс түрі бұл, сыналы белбеулі беріліс, сонымен қатар дөңгелек қимадағы белбеулер кездеседі. Сыналы белбеулер үшін жұмысшы беті болып шкифтің жақтауындағы сыналы оршықтардың бүйірлік жақтары қызмет етеді.
Шкифтерді СЧ 12, СЧ 15 шойынынан және де 25 маркалы құрыштан, алюминий қоспасынан, сирек құрыштық пісірілген және пластмассалық шкифтер кез-деседі. Шкифтің күйреуі түрлі себептермен жүреді. Белбеулі берілістің жұмысшы міндетті шарты, бұл, белбеу мен шкиф арасындағы қажетті үйкелісті қалыптастыру. Ал ол, өздігінде шкиф пен белбеудің қызуын және олардың тозуын тудырады.
Бұл құбылыс белбеудің тайғанауымен күрделенеді, әдетте оларға артық күш түскен жағдайда немесе әлсіз керілуі кезінде. Сондықтан да белбеудің уақыт бірлігіндегі майысуына тәуелді кедергі шаршауымен анықталады. Белбеудің ұзақ мерзімділігіне жоғарғы температура әсерін тигізеді. Өздігінде жоғары темпе-ратура әсерін тигізеді. Өздігінде жоғарғы температура, тек белбеудің шкифке үйкелісінің салдары ғана емес, сонымен қатар белбеудегі іштей үйкелісінің нәтижесі.
Шкифтерге біршама тән жарамсыздықтардың түрлері: жақтаудың сыналық оршығының тозуы, жақтаудың, спицтің және керітпештің жарылуы, шпонкалық паз бен шлицалардың отырғызылу саңылауының тозуы, шкифтің тепе-теңсіздігі. Сына белбеулі беріліс оршығын бүйіршік жақтауының тозуы кезінде үлкен өлшемге токарь станогында жонуға рұқсат етіледі, яғни белбеудің келесі үлкен қи-масында. Бұл кезде екінші шкифте қабылданған белбеудің жаңа қимасының өлшеміне өңделеді.
Шкифте жарғыншақтың пайда болуы рұқсат етілмейтін жағдай. Жақтаудағы немесе спицадағы орын алған жарғыншақтарды жөндеу барысында алдын ала олардың қырларын өңдеп сонан соң оны қолмен атқарылатын доғалы немесе газды пісірумен пісіреді.
Шынжырлы берілістер өнеркәсіпте қоректендіргіштердегі, ленталы және сыдырмақтағы (скребковых) тасмалдағыштарда және т.б. жабдықтардағы жетектен орындаушы механизмге айналдыру моментін беру үшін кезеңінен қолданылым тауып отыр. Мұндай беріліс жетекші және жетектелуші жұлдызшаларды иіле қамтитын шынжырдан тұрады. Біршама кең таралғаны, бұл, бірқатарлық роликті ПР типтегі қалыпты сериялы және ПРА типті жеңіл сериялы шынжырлар.Жауапкершіліксіз берілістерде төлкелі шынжырлар қолданады.
Шынжыр пластиналары көміртекті және қоспалы құрыштардан ( маркалары 45, 50, 40Х, 60Г) дайындалады. Шынжыр өсі, төлкесі, роликті-цементацияланған (15, 20, 15Х, 20Х, және т.б.) HRC 40-65 қаттылыққа дейін шынықтырылған құрыштан жасалады. Беріліс жұлдызшалары сұр шойыннан ( СЧ-18, СЧ-30 және т.б.) және шынықтырылған ( 45, 40Х, 45Г және т.б.) маркалы құрыштардан жаса-лады.
Жұмыстық пайдалану процесінде абразивті заттар, өңделінетін өнім құра мындағы, шынжыр топсаларына келіп түсіп үйкелісуші беттер арасында ұзақ уақыт ұсталына отырып абразивті салмақ түзеді.
Үйкелісудің нәтижесінде шынжыр бөлшегінің тиісті беттері мен жұлдызша тістері тозады. Атап өткен жөн, яғни төлкелі тісті берілістің тозуы роликтіге қарағанда жоғары. Бұл жағдайдың орын алуы, роликтің сырғанау үйкелісін тербелу үйкелісімен ауыстыратындығынан, және де меншікті қысымды азайтатындығымен түсіндіріледі.
Топсалардың тозуы өздігінде шынжыр адымының өсуіне және оның ұзындығының ұзаруына әкеліп соғады. Және де мұның салдарынан жұмыс барысындағы шудың басым болуы, шынжырдың жұлдызшадан сырғып кету қауіпті орын алады, сонымен қатар түбінде шынжырдың үзілуі заңды.
Берілістің жұмыстық пайдаланылуы процесінде шынжыр ролик пен төлке секілді күйреуге ұшырайды. Тозу, шынжыр қысқа болған сайын және жұлдызшаның айналу жүйілігі үлкен болған сайын күшейеді.
Шынжырдың тозуы жөндеуге берілмейді, себебі, әдетте шынжырдың тозуы ұзындығы бойынша бірқалыпты жүретін болғандықтан. Сондықтан да оны жаңа шынжырмен ауыстырады.
Жұмыстық қолдану процесінде орнатылғандай, роликті шынжырлардың топсасының тозуында тозуға ішкі мүшелерге қарағанда сыртқы мүшелері көбірек ұшырайды. Аталған жағдайды ескере отырып, шынжырды бөлшектеусіз жөндеу тәсілі жасалып дайындалған. Тәсілдің мазмұны, көрші ішкі мүшелер төлкелерінің азайтумен түсіндіреді. Бұл үшін жоғары жиілік тоғымен сыртқы мүше пластинасының ортаңғы бөлігін жұмсақтық күйге дейін қыздырамыз сонан соң шынжырды сығады.
Бұл тәсілді 45% үлкен болмайтындай шамаға ұзарған шынжыр үшін қолдануға болады. Уақытша шара ретінде біршама тозған валиктерді жөнделінген валиктермен ауыстыру тәжрибеленеді.
Жөндеуден соң шынжырлы графитті жақпада немесе 50-80С температурада 7-10% графит ұнтағы араластырылған маркалы солидолында мұқият пісіру қажет.
Бір шама тозуға көбірек берілетін шынжырлы беріліс элементінің келесі бірі, бұл жұлдызша, атап айтқанда жетекші. Мұның тозуы тістерінің қалыңдығының жұқаруымен байқалады, сондай-ақ қажалуға жұлдызшаның жұмысшы қырлары көбірек беріледі.
Тозуға ұшыраған тістерді қалпына келтіру тым күрделі мәселе. Сол себепті, әдетте тозған жұлдызша орнына жаңасын орнатады. Жөндеудің перспективті әдісі, бұл, жұлдызшаның ауыспалы күмбез орнату болып табылады. Кейбір жағдайларда тозған тістерді балқыма қабат төсеп, соңынан оны механикалық өңдейді (ажарлайды). Балқыма қабат төсеумен қалпына келтірілген жұлдызшаның сапасы жоғары емес. Жөндеуге кеткен шығындардың орасан мөлшері мен қалпына келтірілген жұлдызша жұмысының қысқа мерзімділігіне байланысты, жұл-дызшаны қалпына келтірудің бұл әдісі сирек қолданылады. Тістері симметриялы орналасқан жұлдызшалар үшін келесі айла тәжрибеленеді, мұнда жөндеу жұл-дызшаны 180º-қа бұру жолымен жүзеге асырылады. Бұл кезде, алдын жұмысқа қолданылған беттер, жұмысшы бет есебінде қолданылады. Бұл тәсіл, жұлдызша жұмысының ресурсын шамамен екі есеге ұлғайтуға мүмкіндік береді.
Шынжыр беріліс жұмысының шусыздығы мен бірқалыптылығы бос жүріс тәртібінде 15-20 минут аралығында жұмыстық үйреністіру барысында т ексеріледі. Сонан соң шынжырды роликтің көмегімен береді, ал жүктемені бірте-бірте жұмысшы мәнге дейін жоғарылатады. Дұрыс беріліс бір қалыпты, соққысыз және шусыз жұмыс істеуі тиіс. Шынжыр жұмыс барысында жұлдызшадан сырғып кетпеуі немесе тіске соғылуы тиіс емес.
Тісті берілісті жөндеу
Химиялық және тамақ өнеркәсібінде, жетістікті түрде цилиндрлік немесе конустық тісті доңғалағы бар тісті берілістер қолданылады. Беріліс типі негізінен жабық. Бірақ сонымен қатар жетістікті түрде ашық типті берілістер кеңінен қолданады.
Тісті берілістерді жұмыстық қолдану тәжрибесі көрсеткендей, жұмыс істеу процесінде тісті доңғалаққа тістің иілу кернеуі, контакталы-шаршау тозуы және тістердің қажалуы әсер етеді. Әсер етуші күштердің аталған сипатына байланысты, тісті доңғалақтың тозуы тістердің қалыңдығының жұқаруымен, жұмысшы беттердің пішінінің бұрмалануымен, тіс түбіндегі шаршау жарғыншағының пайда болуы мен және тіс бетінің қабыршақталуымен жүреді.
Шаршау жарғыншағы иілу салдарынан ең үлкен созылу кернеулер пайда болған орындарда қалыптасады. Қысқа тік пішінді тістер толығымен сынады, ал ұзын, аса гипоидты немесе қиғаш тістер қима бойынша сынады.
Тістердің активті беттерінің қирауы контактылық кернеулер мен үйкелісу күшінің әсерімен шатталады және де шаршаушы күйреу, механикалық тозу және қашау түрінде болады.
Тістің шаршаушы қирау үздіксіз және малынбалы майлану жағдайында жұмыс істейтін, тісті беріліс доңғалағының жиі істен шығу себебі болып табылады (мысалы үшін, май ваннасына батыру жолымен және т.б.).
Көп жылғы тісті берілістерді жұмысқа пайдалану тәжрибесінің нәтижесінде орнатылғандай, тісті берілістерді түрлі жұмыс жағдайында қолдану кезеңдерінде түрлі механикалық тозулар түрлері анықталып отыр. Осыған орай, тозу дәрежесін бағалаудың түрлі тәсілдерін қолдану қажет.
Әдетте, тістердің ұшының толық ұшталып қалуы кезінде, тісті доңғалақты тозған деп санайды да, мұндай доңғалақтар жарамсыз деп танылады. Тістің қалыңдығы бойынша тозуын тіс қалыңдығының алғашқы және нақты мәнінің айырмасы бойынша анықталады, және де мұны штанген тіс өлшегіштің тұрақты хордасы бойынша өлшейді. Тұрақты хорда-деп, алғашқы контур мен тіс өсіне перпендикуляр қимадағы тіс профилімен жанасар нүктелер аралығындағы түзу сызықты айтады.
Бұл хорданың өлшемі тұрақты модульдегі түрлі тіс саны бар доңғалақтар үшін бірдей.
Өнеркәсіптік технологиялық жабдықтарда, тозу нәтижесінде тістердің қалыңдығының жұқаруы келесі аралықтарда рұқсат етіледі:
- 2 м/с шеңберлік жылдамдық кезіндегі ашық тісті беріліс үшін-30%; немесе 0,5m, (мұндағы m-тіс модулі, мм).
- 5 м/с дейінгі шеңберлік жылдамдықта жұмыс істейтін редукторлық және басқа да берілістер үшін – 20% дейін.
- 5-10 м/с шеңберлік жылдамдықта жұмыс істейтін беріліс үшін- алғашқы тіс қалыңдығының 15% дейін.
Тістің кескін бетінің тозу шамасы тіс ұзындығының 10-15% аспауы тиіс. Химика-термиялық өңделген беті бар тісті доңғалақтарда беріктетілген қабаттың тозу шамасы осы қабаттың алғаш қалыңдығының 80%-нен аспауы керек. Үлкен тозу шамасында доңғалақтарды ауыстыру керек.
Тістерді дер кезінде ауыстырмау тістің сынуын тудыруы және де берілістің басқа да тісті доңғалақтарын істен шығаруы мүмкін.
Цилиндрлік тісті доңғалақтың реверсивсіз жұмысы мен симметриялық конструкциясы кезінде, біліктегі доңғалақты тістің тозбаған бетін қолдану үшін ауыстыруға болады. Бұл айла берілістің тісті доңғалағының ұзақ мерзімділігін шамамен 2-ге арттыруға мүмкіндік береді.
Қазіргі уақытта, тісті тәждің тозған тісін толық жойғанға дейін жонып, зауытта дайындалған жаңа тәжді престеп отырғызумен жүретін жөндеу әдісі қол-данылады. Престеп отырғызу жөнделінген тәжді алдын-ала май ваннасында қыздырумен жүреді. Сонымен қатар, тәжді кертпешке тойтарып шегелеп біріктіген конструкцияларда кездеседі. Бұл кезде шегелеп тойтаруды суық күйде жүргізген жөн. Енді тәждер үшін тойтарып шегелеуді қыздырған шегемен жүргізген тиімді.
Аталған тозу түрлерінен басқа, тісті доңғалақтарда келесі тозу түрлері кездеседі: 1) Шлицалар мен шпонкалық паздардың тозуы. 2) Спицалардағы, жақтаушадағы және кертпештердегі жарғыншақтардың орын алуы. Бұл кездегі жөндеу әдісі жарақаттану сипаты мен доңғалақтың конструктивті ерекшелігіне байланысты болады. Мұндай бөлшектерді қалпына келтірудің негізгі әдісі жоғарыда қарастырылған.
Бағаналы аппараттарды жөндеу
Өнеркәсіптерде бағаналы аппараттарды негізінен, басты мақсатта жылу алмасу процестерін (экстракция, абсорбция, қайта қолданылу суын өңдеу) жүргізу үшін қолданылады.
Жөндеу бойынша қарастырылған операциялар мазмұны мен оларды реттілігі бағана өлщемі мен конструкциясына байланысты 800 мм диаметрдегі бағаналар фланецтер көмегімен жиналған царгалы етіп жасалады. Ал 800 мм жоғары диаметрдегі аппараттар пісіріліп дайындалады.
Бағаналы аппараттардың негізгі түрлері, бұл, ішкі құрылғыларының коррозиялық және эрозиялық тозуы, сондай-ақ тоғыстырғыш элементтері мен ішкі құрылғыларының қатты шөгінділермен бітеліп қалуы.
Бағаналы аппараттарды жөндеу барысында, бағаналарды босатып алу біршама еңбексыйымдылықты талап етеді. Бүтіндей пісірілген бағаналар, әдетте, жөндеу барысында демонтаждалмайды (бөлектенбейді). Бұл кезде тек ішкі құрылғылары бөліктенеді. Царгалы етіп дайындалған бағаналар толығымен бөлшектелінеді. Царгаларды бөлшектеу кезінде жүккөтергіш механизм бағаналардан жоғары орнатылады және де бұл царгаларды кезектестіре бөліп алуға мүмкіндік береді. Жүк көтергіш механизмді бағанадан жоғары орналастыру мүмкіндігі болмаған жағдайда, бағаналарды бөліктеуді төменнен бастайды. Бұл кезде алдын ала жоғарыда орналасқан царганы уақытша тіректерге бекітеміз. Тірек конструкциясы бағананың қалған бөлігінің тұрақтылығын және де кезектестіріле царгалардың бөлшектелуін қамтамасыз етуі қажет.
Дайындау операциялары ішкі құрылғыларын жуу мен бумен өңдеу жұмыстарын қарастырады. Бағананы бумен өңдеу жұмыстарын қарастырады. Бағананы бумен өңдеп болған соң, сумен жуып, желмен кептіреді. Соңында бағананың түрлі деңгейінен алынған ауаны, улы заттардың концентрациясының шамасының болуына анализ жасайды. Ішкі құрылғыларын бөлектеуді аппарат ішіндегі газды ортаны тексерген соң бастайды. Бұл үшін аппараттағы барлық люктер кезектестіріле төменнен жоғары қарай ашылады. Табақшалар немесе басқа да контакталық құрылғылар бағана ішінде бөлшектелінеді де, люктер арқылы қызмет көрсету алаңдарына шығарылады және де, шөгінділерден тазарту және жөндеу үшін механикалық шеберханаларға жөнелтіледі.
Үлкен өлшемдегі бағаналы аппараттар жүккөтеру жұмыстары кезінде қолданылатын, таль орнатылған балкамен жабдықталады. Табақшаларды тасымалдау монтаждық арбалардың, автокаралардың және де басқа тасымалдау жабдықтарының көмегімен жүзеге асырылады.
Саптамалы бағанаға қызмет көрсету және оларды жөндеу кезінде басты мақсат ішкі құрылғыларын, аппарат қаңқасын тазалау мен саптама денелерін ауыстыруға назар аударылады.
Бағана қаңқасының тозуының негізгі түрі, бұл саңылаулар мен жарғыншақтардың пайда болуымен жүретін коррозия, сондай-ақ қаңқадағы майысулар.
Саңылаулар мен жарғыншақтар пісіріп бітеудің және де алдын ала жарақаттанған участкелерді ойып жамақ жамау көмегімен орнына келтіреді. Бұл үшін алдын ала жарықтық ақау көшіру көмегімен жарғыншақтардың ұзындығымен олардың ұштарының жағдайы анықталады. Жарғыншақтар ұшы диаметрі 3-4 мм-лік бұрғы көмегімен бұрғыланады да, ал оның қырлары пісіруге жасақталып дайындалады. Өн бойына өтпеген қабырға қалыңдығының 0,4 үлкен болмайтындай тереңдіктегі жарғыншақтар қырдың қиғаштылығын 50-60 бұрышта ала отырып жарғыншақтардың максимал тереңдігінде пісіруге бір жақты шауып жасақтайды.
Тереңдегі қабырға қалыңдығының 0,4 асып кететін өн бойына өткен және өн бойына өтпеген жарғыншақтардың қашаумен немесе көзкескішпен жасақталады.
Ұяшықты жарғыншақтар қалыптасқан жағдайда жарақаттанған жерлер ойылып алынып дөңгелетілген қырлы жамақпен жамалады. Жамақтар негізгі материалмен біркелкі пісіріледі. Жамақ ауданы аппарат табағының ауданының 1/3 аспауы тиіс.
Жиі коррозияның салдарынан түптер істен шығады. Қаңқа мен түптің ақау учаскелерін ауыстыруды, қажет болған жағдайды бағананы бөлектеп алуысыз жүргізеді. Бұл жағдайда бағананың жоғарғы бөлігіне тіректік алаң бекітіледі де, тірек домкраттарға тіреледі. Бағаналы аппараттардың төменгі бөлігі кесіліп тасталады да бағананың жоғарғы бөлігі 100 - 150 мм көтерілгеннен соң әкетіледі. Жаңа түп орнатылғаннан соң, жоғарғы бөлік төмен түсіріледі де пісіріледі.
Аппарат қаңқасын жергілікті ауыстыру кезінде келесі бір қатар талаптарды орындау қажет:
1. Жапсырма материалы механикалық және химиялық қасиеті бойынша қаңқа материалымен бірдей болуы тиіс;
2. Қаңқаның ауыстырылушы бөлігінің қалыңдығы жобаланған қабырға қалыңдығынан аз болмауы тиіс;
3. Пісірілу барысындағы қолданылуышы электродтар пісірілуші материал маркасына сәйкес болуы тиіс;
4. Түйістірілуші қабықтар ені 400 мм-ден кем болмауы тиіс;
5. Қабық пен негізгі материал қырлары 10 мм енде пісіру алдын таза болатқа дейін тазалануы тиіс;
6. Цилндрлік қабықтың жеке бөліктеріндегі ұзына бойғы жіктер, сондай-ақ қабыққа жалғасып жатқан түптің меридиналды және хордалық жіктері бір-біріне қарасты 100 мм ығыстырылуы тиіс;
7. Кейбір қабықтардағы ұзына бойғы жіктер арасындағы ара-қашықтық мм-ден кем болмауы тиіс;
8. Түйісу жерлерді пісіру кезінде бір элементтен екінші элементке бір келкі өтуді қамтамасыз ету қажет.
Контакталық құрылғыларын жөндеу табақша немесе саптама типіне, бағананың өлшемдеріне және т.б. байланысты. Бір қатар жалпылама жағдайларда жөндеу, өздігінде, шөгінділерден тазарту, ақаулыққа тексеру және тозған элементтерді ауыстыру операцияларын қарастырады.
Орнықтырылғаннан соң табақшалы аппараттарды сынау кезінде табақшалардың горизонталдығына үлкен көңіл бөлінеді, өйткені қиғаш орналасудың болуы жұмыс тиімділігін елеулі төмендетеді. Табақшалардың горизонталдылығы деңгейдің көмегімен тексеріледі.
Бағаналарды жөндеудің аяқтаушы кезеңі, бұл, оның сыналуы. Гидравликалық сынауды жүргізу үшін бағана сумен толтырылады. Бағана сумен толтырылғаннан соң, қысымды бақылаушы шамаға дейін баяу көтереді де бұл қысымда аппаратты 5 минут уақыт ұстайды, сонан соң қысым жұмысшы қысымға дейін баяу түсіріледі. Жұмысшы қысымда пісіру жігін балғамен соғып тексеру және бағана қаңқасын тексеру жұмыстары орындалады. Пневматикалық сынау барысында пісіру жігін балғамен соғып тексеруге қатаң тиым салынады. Сынаудан ойдағыдай өткен аппарат акт бойынша жұмыстық пайдалануға беріледі.
Жылуалмастырғыш аппараттарды жөндеу
Мұнай өңдеу зауыттары мен негізгі химия салаларының кәсіпорындарының техникалық паркіндегі жылуаламастырғыш аппараттардың үлесі 40 % жуық.
Ұзақмерзімді пайдалану барысында бұл аппараттарды жұмысшы беттері ластану мен тозуға ұшырайды. Жылуыалмастыру беттерінде қақ, лай, тұз, тұз қабаттары түзіледі, тотық плежкалары пайда болады.
Бұл шөгінді қабат өсіуінен бөліп тұрушы қабырғаның термиялық кедергісі өсіп, жылу алмасу нашарлайды. Әсіресе беттік жылуалмастырғыштар үшін.
Жылуалмасу аппараттарында келесі тозулар орын алуы мүмкін:
1) аппарат қаңқасының, түбінің және құбырларының қалыңдығының жұқаруы;
2) қаңқа мен түптердегі ісінулер мен майысулар;
3) құбырлардағы, қаңқалардағы және орланеубердегі саңылаулар, жарғыншақтар және күйінділер;
4) құбырлар үшін құбырлы тордағы саңылаулардың диаметрінің ұлғаюы;
5) құбырлы тордың иілуі мен құбырдың деформациялануы;
6) толқымалы бүршіктің сыналасуы мен олардың струбциналарының жарақаттануы; 7) компенсациялаушы құрылғының жарақаттануы;
8) сырғанау және серіппелі тілемдердің жарақаттануы;
9) гидро және термоизоляцияның бұзылуы.
Жөндеуге дайындау кезеңі келесі іс-шараларды қарастырады:
1) аппараттағы қысым атмосфералық қысымға дейін түсіріліп аппарат өніммен босатылады; 2) арматуралар ажыратылып, барлық әкелуші және әкетуші құбырөткізгіштерде тығын орнатылады; 3) аппарат қуысын азотпен немесе бумен өңдеп, соңында сумен шаю, ауамен үрлеп кептіру жұмыстары орындалады; 4) улы және жарылыс қаупіпті заттардың болуын тексереді; 5) жөндеу процесінде қажет жағдайда от жалынды жұмыстарға жоспар түзіліп, орындауға рұқмат алады; 6) жөндеуге тапсыру акті түзіледі.
Әрі қарай келесі жұмыстар орындалады: 1) аппаратт қақпағын, люктерді ашу, құбырлар мен арматураларды демоетаждау; 2) жұмысшы қысымда гидравликалық немесе пневматикалық сынауменен құбырдың вальцовкалануындағы, пісіруіндегі және тұтастылығын тексеру жұмыстары орындалады; 3) ақау болған құбырларда жергілікті ауыстыру немесе пісіріп бітеу, құбырды вальцовкалаумен немесе пісірумен бекіту; 4) бөлшектердің коррозияға қарсы қабаттары мен футеровкаларын жөндеу немесе ауыстыру; 5) тозығы жеткен арматуралар мен құбырларды жөндеу немесе ауыстыру, сақтандыру клапанын реттеу; 6) бұрандалы қосылыс тығыздағыштарын ауыстыру; 7) құбырлоы шоғырды шығару, аппарат қаңқасының және құбырлардың ішкі беттерін тазалау, құбырлы тордағы саңылауды тазалау, құбыр ұштарын өңдеу; 8) қаңқаның, түптің (қақпақтың) бөліктерін және тозған бөлшектерді ауыстыру; 9) жаңа құбырларды дайындау; 10) құбырлы шоғырды құрастыру және монтаждау; 11) толқымалы бүршікті жөндеу; 12) бұрандалы қосылыстарды монтаждау; 13) байқау қысымында аппараттың құбырлы және құбыраралық кеңістіктерін гидравликалық сынау; 14) аппаратты пневмосынау.
Жылуалмасу аппараттарын жөндеу барысындағы едәуір еңбексыйымды болып табылатын операциялар: 1) бұрандалы қосылыстарды монтаждау және демонтаждау, аппаратты тазалау; 2) құбырлы шығырды шығарып алу, дайындау және оны орнату; 3) жылуалмастырғышты сынау.
Бұрандалы қосылыстарды монтаждау және демонтаждау пневматикалық және гидравликалық гайка бұрағышпен орындалады. Қақпақты шешіп алу жеңілдігі бұрылмалы кронштейнді қолдана отырып жүреді. Құбырлы шығырды шығарып алу жұмыстарын толқымалы бүршікті және U - тәріздес жылуалмастырғыштарды жөндеу барысында орындайды. Құбырлы шығырды экстракторларды, домкрат пен лебедканың көмегімен, автомобиль кранымен, тальдың көмегімен жылжытқыш монорельсті немесе тележканы қолдана отырып орындауға болады.
Құбырлы шоғырды тракторлық лебедка мен автомобильдік кранның көмегімен демонтаждау келесі реттілікте орындалады: 1) аппарат қақпағы шешіліп, балқымалы бүршік бөлшектері демонтаждалады; 2) құбыр шоғырын алдын ала қозғалту орындалады; 3) тракторлық лебедкамен құбырлы шоғыр аппараттан тыс шығарылады; 4)хомұттар мен стропатрдың көмегімеенен құбырлы шоғыр автомобиль кранынның ілгегіне ілінеді; 5) шоғып толықтай тыс шығарылғаннан соң, тазалау және жөндеу орнына жеткізу үшін прицепке тиеледі.
Құбырларды шөгіндіден тазалау үшін тазалаудың химиялық, абразивті және арнаулы әдістерін қолданады. Бұл әдістерменен құбырдың сіртқі және сыртқы, сондай-ақ қамқолының ішкі қуыстарын тазалауға болады.
Тазартудың жимиялық тәсілін аппаратты ашу және бөлшектеусіз қолдануға болады. Шөгіндінің табиғатына қарай шөгіндегідей еріткіштерді қолданады: 1) қақтан тазалауда – 5÷10 % тұз қышқылын ингибиторды араластыра отырып; 2) органикалық шөгінділер үшін – көмірсутекті еріткіштерді; 3) қатты шөгінділер үшін – сұйық шыны араласқан 5 % тұз қышқылын толтырып қойып тазалайды, бұл кезде борсытылған тұнба сумен шайылып тасталады.
Жылуалмасу бетін қатты шөгінділерден тазалау үшін жөндеу шаруашылығында механикалық, гидромеханикалық, гилропневматикалық, пневмомеханикалық, құматқылау және арнаулы тәсілдерді қолданады.
Тазалаудың пневмомеханикалық тәсілі кезінде тісті механикалық шомпол-төлкені қолданады. Шомпол құбыр қуысында 0,5÷0,6 мПа муя қысымының әсеріменен қозғала отырып, шөгіндіні қырады. Бұл кезде шомполдың қозғалу бағытын ауаны таратқыштың көмегіменен реттейді.
Тазартудың гидропневматикалық тәсілінде бетті шөгіндіден су, ауаның, кислородтың көмегімен тазартады. Пистолетке бір мезетте шланганың көмегімен 1:1 қатынаста ауа 0,7 ÷0,8 МПа және су 0,5÷0,6 МПа қысыммен беріледі. Бұл тәсіл механикалық тазарту тәсілемен салыстырғанда тазалау уақытын шамамен 8-10 есеге қысқартуға мүмкіндік береді.
Гидромеханикалық тазалау тәсілінде жылуалмасу беті шөгіндіден соплодан үлкен қысымда шығатын су толысымен тазалайды. Мұнда басқа әдістерге қарағанда тазалау дәрежесі елеулі жоғары. Бір құбырды тазалау уақыты шамамен 10-15 сек. Қысымның өзгеру диапазоны 15 МПа – дан 70 МПа – ға дейін жетеді. Кез-келген қаттылықтағы шөгіндіден тазалау мүмкіндігі бар, сонымен қатар жөндеу шаруашылығында шөгіндіден бетті тазартудың құматқынды және арнаулы тәсілдерін қолданады.
Құбырлы шоғырды жөндеу барысында, жарақаттанған құбырлар саны 1 ағындағы жалпы құбыр санының 15 % аспаса, онда жөндеуді құбырды бітеп тастауменен орындайды. Егер де бұл шама 15 % асып кетсе, жарақаттанған құбырлар жаңасымен ауыстырылады. Жарақаттанған құбырларды ауыстырғанда келесі талаптар орындалуы тиіс: 1) құбыр материалы ортаның сипаттамаларын, оның параметрлерін ескере отырып, қолданыстағы коллективтерге сай қабылдананды; 2) орнатылушы құбыр ұзындығы әрбір тұсқа 8-10 мм ортақ етіп қабылдананды; 3) құбыр ұштары металдың тазалыққа дейін, 10 мм әдіппен құбырлы тор ұзындығында өңделеді; 4) құбырлы тордағы саңылауды вальцовкалауға дайындау барысында, адырлық 7 кластан төмен болмауы тиіс, және де бетте жоңқалар, шірінділер, қатар мен ұзына бойғы сызаттар болмауы тиіс; 5) құбырдың сыртқы беті мен саңылаудың ішкі беттері арасындағы саңылаулық 1,5/d болуы керек.
Құбыр құбырлы торда пісірумен немесе вальцовкалаумен бекітіледі. Развальцовкалауда өзектегі төрт құбыр айқастырылып развальцовкаланады да, сонан соң периметрі бойынша барлық құбырлар соңында қалғаны бекітіледі. Бұл кезде құбыр деформацияға ұшырамауы үшін ең алдымен бір тақтадағы бүкіл құбыр, сонан соң екінші тақтадағы құбырлар развальцовкаланады.
Развальцовкалауда келесі ақаулардың орын алуынан сақтануы керек:
1) құбырдың развальцовкаланған және развальцовкаланбаған бөліктерінде елеулі пішім өзгеруі болмауы тиіс; 2) тым ұзын колоколчиктің немесе құбырдың құбырлы тордан шығарудағы бөлігінің ісініп кетуінен; 3) құбырдың тор саңылауынан шығардағы бірырғақты ісінуі; 4) құбырдың құбырлы тор саңылауы бойында қиылуынан; 5) құбырдың вальцовкаланған бөлігіндегі немесе колкольчигіндегі жарғыншақ пен қысқарудың болуынан.
Аппарат қаңқасындағы ісінулер мен майысулар мыс төсемде кувалда соққысымен немесе қабырға қалыңдығы 3-4 мм үлкен болмаған жағдайда термиялық әдіспен түзетіліп, қалыпқа келтіріледі. Егерде жоғарыда айтылған ақауды механикалық немесе термиялық тәсілдермен түзетуге болмайтындай болса, онда ақау жолақ жалаумен немесе жапсарлауменен қалыпқа келтіріледі.
Тесіктер мен жарғыншақтар жолақ жамаумен пісіріп бітеумен қалпына келтіріледі.
Аппарат қаңқасын жергілікті ауыстыру кезінде келесі талаптар орындалуы тиіс: 1) қаңқаның жаңа бөліктерін дайындауға қажет материал механикалық және химиялық қасиеттері бойынша жөнделуші қаңқа материалына сай келуі қажет; 2) ауыстырылушы бөлігінің қалыңдығы жобалық қалыңдықтан кем болмауы тиіс; 3) электродтар пісірілуші материалға сай келуі тиіс; 4) түйістіруші қабық ені 400 мм кем болмауы тиіс; 5) горизонтал аппаратта ұзына бойығы жіктер төленінде орналаспауы тиіс; 6) қаңқа мен негізгі метал қырлары 10 мм енде пісірер алдын таза металға дейін тазаланады; 7) аппаратттың цилиндрлік бөлігіндегі жеке қабақтарда ұзына бойғы жіктер, сондай-ақ қабыққа түйісер жердегі түптің меридианал және хордалық жіктері бір біріне қатысты 100 мм кем болмайтындай қашықтыққа ығысуы тиіс; 8) жеке қабықтарда ұзына бойғы жіктер арасындағы қашықтық 200 мм-ден кем болмауы тиіс; 9) түйісу жердерді пісіру барысында бір элементтен екінші элементке біркелкі өту қарастырылуы тиіс.
Жылуалмастырғыш жабдықтарды жөндеу опресовкалаумен аяқталады. Гидравликалық сынау барысында су құбырларынынң кеңістігіне беріледі. Судың кезкелген құбырда пайда болуы жөндеу барысында ақаудың орын алғандығын көрсетеді.
Ыдыстық аппараттарды жөндеу.
Ыдыстық аппараттар негізінен сұйық өнімдерді сақтауға арналған.
Ұзақ мерзімді пайдалану нәтижесінде ыдыстық аппараттар денесінде келесі жарамсыздықтар мен жарақаттар орын алады: 1) өнбойына өткен немесе өтпеген жарқыншақтар түріндегі тұтастықтың бұзылуы; 2) қақпағы мен қақпағында іліктер, және де қабырғаның деформациясы түріндегі пішіннің бұрмалануы; 3) аппараттың қабырғасының коррозиясы.
Жөндеу жұмыстары басталар алдын жобалық құжаттарды, аппараттарды жөндеуге дайындау: конструкцияның ауыстыруға тиісті конструктивті элементтері, жөндеу және такеллаждық жұмыстарға қажетті арнайы және бейстандартты жасақтар мен аспаптарды дайындау жұмыстары орындалады.
Жөндеу жұмыстарын жүргізуге жобалық құжаттар ақаулық ведомостіні, жұмыстарды жүргізу жобасы, жөндеу-монтаждық жұмыстарды орындау кестесін қарастырады.
Аппараттарды жөндеуге дайындау, оны жалпы зауыттық тораптан ажырату, өнімнен босату, қуысын тазалау, булау және жөндеу, қалған ластардан (құмдардан, қаттардан және т.б.) тазарту жұмыстарын орындауменен жүреді. Аппаратта толықтай дегазациялаудан соң ақауларды қалпына келтірумен байланысты жұмыстар сипаты мен көлемін пысықтау үшін бақылау-тексеру жұмыстары орындалады.
Керосиндік тәсіл көлемінен пісіру жіктерін, жарғыншақ өлшемі мен контурын тексерулер орындалады.
Қабырға қалыңдығының жарғысына жетпеген жарғыншақтар зубиланың көмегімен таза металлға дейін шабылып пісіріп бітеу арқылы қалпына келтіріледі. Жіңішке өнбойына өткен жарғыншақтар мен қабырға қалыңдығының жарғысынан асқан жарғыншақтар металдың бүкіл қалыңдығына зубиламен шауып немесе газды кескішпенен кесіп өңделеді.
Енді өн бойына өткен шіріктер мен енді жарғыншақтарды металды ойып алып жалаң жамаумен жөндейді. Мұнда қабырға қалыңдығы 6 мм аз ыдыс қабырғасы үшін жақ жапсарланып пісіріледі. Жапсарланған металл 30-40 мм болуы тиіс, және де қабат пен металл арасындағы саңылаулық 1,5 мм-ден аспауы тиіс. S≥ 6 мм болғанда жалаң қабырғаға түйістіріліп пісіріледі. Пісіру қыраралық саңылау 2-4 мм, қырлардың қиғаштылығы 30-35 º жағдайда керіситалы жікпен екі жақты орындалады. Жақ өлшемі 200х150 мм кем емес және жөндеуші қабырға табақшалы ауданының 1/3 бөлігінен аспауы тиіс өлшемде болуы тиіс.
Үлкен емес майысулар мен ісінулер ойылып алынып жамақ жамаумен қалпына келтіріледі. Қарқынды коррозияға ұшыраған резервуар қақпақтары жарақат көлеміне қарай жергілікті немесе бүкіл қақпақты ауыстырумен жөндейді. Бүкіл қақпақты ауыстыру барысында не жапсырмалы ауыстырылады не жапсырма каркасымен бірге ауыстырылады.
Аппарат қаңқасы белдемшемелеріндегі жарақаттар жергілікті жарақатта табақшалы ауыстыруменен, немесе ауқымды жарамсыздықта бүкіл белдемшені ауыстыруменен жөнделеді. Соңғы жөндеу тәсілін рулонды ауыстырумен жөндеу деп атайды.
Аппарат қаңқасындағы белдемше жарақаттарын рулонды дайындама көмегімен ауыстыру оқшаулы кран көмегімен жүреді.
Рулонның жайылу шамасына қарай оқшаулы-кран сипаратты айналады, бұл кезде дайындама жолағы сыналы аспап көмегімен тағылады.
Ұзындығы 6 м-ден аспайтын жолақ орнатылып болғаннан соң, оны пісіру жұмыстары орындалады. Пісіру жұмыстары толық аяқталғаннан соң жікті тығыздыққа керосинмен сынау орындалады. Соңынан бүкіл резервуарды гидравликалық сынау орындалады. Ойылып алынған ескі белдемешелер, оларға пісірілген скобаларға ілініп алынып тасталады.
Ұзақ мерзімді пайдалану барысында аппаратта сақталатын сұйықтың гидростатикалық қысымы әсерінен резервуар түбі жергілікті ойыстылып алып майысу мүмкін. Сонымен қатар түп коррозиялық тозуға ұшырауы мүмкін.
Түптің жарақатының көлемі мен сипатына қарай, жөндеу түнгі толық ауыстырумен немесе табақшалы ауыстырылуы мүмкін. Жарғыншақ немесе ісіну түріндегі жергілікті жарақаттар жамақтаумен қалпына келтіруі мүмкін.
Түптің коррозияға ұшырауын алдын алу үшін оған торкрет-төсем немесе бөлу қабатын береді.
Цементтік торкрет-төсем 400÷500 маркалы цементтен және ұсақ майдаланған өзен құмынан тұрады. Қоспаның массаның қатынасы 1:2. Қоспа ретінде сонымен қатар диабазалық уы немесе майдаланған кварц құмы қолданылады.
Цементтік төсем төсеу процесі келесі операцияларды қарастырады:
Қорғалуға тиісті бет қаттардан, шіріндіден тазартылады. Төсемге тиісті беріктік беру үшін серпімді тор керіледі. Тор диаметрі 3-5 мм болат сымынан көздерінің өлшемдері 60х60 мм немесе 100х100 мм болатындай етіп таңылады. Орнатылар алдын болат торы ластан тазартылып монтаждық ілгектерге ілінеді.
Торкрет-төсемінің құрғақ қоспасы араластырғышта дайындалады. Торкрет-төсемді төсеу процесі цемент-пушкасын, ауа тазартқышты, су багын және 0,5 Мпа кем болмайтындай қысымда қамтамасыз ететін компрессорды қолданумен жүреді. Цементтік төсем 2-3 кезеңде төселеді. Торкрет-төсемнің жалпы қалыңдығы 70 мм болуы тиіс. Төсемнің 1-ші және 2-ші төсемі арасында серпілту торы төселеді. Цементтік төсем қатуын су қабатын беріп, 15-20 тәулік бойы су астында ұстаумен орындайды.
Деформацияға ұшыраған бақшаны ауыстырусыз ісікті қалпына келтіруді ісік биіктігі 200 мм-ден үлкен болмағанда қолданады. Мұндай ісінуді жөндеу процесінде, ісінді ұшында диаметрі 200-250 мм-лік саңылау ойылады.
Ісік асты қуысқа гидрофопты қоспа толтырылады. Қоспа құмнан және байланыстырғыш заттан тұрады.
Байланыстырғыш зат ретінде әлсін күкіртті мазут немесе мұнайды қолданады. Байланыстыру заты 8-10 % салмақ көлемінен алғандағы мөлшерде араластырылады. Қоспаның алғауылығы 5 % (шым) аспауы тиіс. Осылай дайындалған гидрофабты қоспа алдын төселген қабатты діпіді құрал көлеміменен тығыздалғаннан соң мезгілді төсеумен төселеді. Қуыс гидрофопты қоспамен толтырылғаннан соң ойылған саңылауға диаметрі 30-35 см-лік жамақ пісіріледі. Ауаның қуыстан толық ығысуынан немесе толтырылу дәрежесін қадағалау үшін ойылған (ісік маңында) диаметрі 8-10 мм саңылаулар пісіріп бітеумен қалпына келтіріледі.
Биіктігі 200 мм үлкен ісіктер, орын алған табақшалы ауыстырумен қалыпқа келтіріледі.
Сорапты-компрессорлы жабдықты жөндеу. Поршенді компрессорларды жөндеу
«Поршенді компрессорлардың жауапты бөлшектері жұмыс істеу процесінде айналу немесе салыстырмалы ілгерлі қозғалыс жасайды, сондықтан да олар интенсивті тозуға ұшырайды. Тозуға ұшыраған негізгі бөлшектер қатарына жататындар: иінді білік; іргелі подшипниктер; шатун; крейпкоф; шток; поршень; цилиндр; клапандар.
Қызмет ету мерзімі бойынша компрессор бөлшектерін келесі үш топқа бөлуге болады:
1) Жылдам тозатын – поршендік сақина, салниктік тығын, клапандық пластиналар мен серіппелер;
2) Орташа қызмет ету мерзімі бар — іргелі подшипник (вкладышы) сынасы мен шатундар; шатун мен крейцкоф саусақшасы;
3)Ұзақ қызмет ету мерзіміндегі — иінді білік, шатун, крейцкоф, цилиндрлер мен поршендер.
Поршенді компрессордың бөлшектері мен түйіндеріне тән тозу түрлері:
1. Иінді білік-біліктің негізгі және иінді нобайының өлшемі мен пішінінің өзгеруі, мойынның жактауалауға ауысар жеріндегі жарғыншақтар, және де иілулер;
2. Іргелі подшипниктер-баббитті кұймалардың тозуы, сыналардың майысқақталуы;
3. Шатун-майысу, сыналардың тозуы, шатундық болттардың созылуы;
4. Крейцкоф-бағыттауыш пен саусақшаның тозуы;
5. Шток - салник арқылы өтер орнындағы тозулар, иілулер. бұранданың қиылуы;
6. Поршень-поршенді сақина орналастыруға арналған саңылаулардың тозуы, сақинаның тозуы:
7. Цилиндр-цилиндр пішінінің өзгеруі (овалдылык, конустылық, бөшкетәрізділік );
8. Клапандар-серіппепің және клапанның жұмысшы беті мен егарының тозуы.
Жөндеуге дайындау процесі электртізбегінен ажырату, өнімнен босатып алу, тазалау, үрлеу, жөндеу үшін құрал мен аспаптар таңдап қабылдаудан тұрады.
Бөлшектеу кезінде келесі кезектілікті ұстайды:
-сырткы құбырларды, вентильдерді, приборлық шитті, май сүзгісін, су құбырын ажырату және бөлшектеу;
-цилиндр қақпағын, айдау клапанын және клапандық тоспаны бөлшектеу;
-компрессордың бүйірлік қақпақтарын ашу және иінді біліктің бөліп алуға қолайлы жағдайын орната отырып сору клапаннын бөлшектеу;
-шатундық подшппникті және шатун мен маховикті қоса поршенді бөлшектеу;
Цилиндрлік диаметрін өлшеуді массаның көмегімен биіктігі бойынша
3 - 5 қимада және білік өсі бойынша кривошипті механизмнің қозғалу жазықтығында екі жағдайда жүргізіледі.
Поршеннің жағдайын тексеру жасау жұмыстық жанасулардағы саңылаулықты тексерумен жүреді. Цилиндр мен поршен арасындағы радиустық саңылаулық поршен диаметрінің 1/1000-1/600 аралығында жатуы тиіс.
Поршенді сақинаны ақаулыққа тексеру поршендегі артық пен сақина арасындағы саңылаулықты өлшеу болып табылады, және де бұл саңылаулық шамасы 0,05 – 0,08 мм құрауы тиіс. Сонымен қатар 0,4 – 0,5 мм аралығында жатуға тиісті радиусты саңылаулық бақылау қарастырады. Саңылаулық қуыс құлақ көмегімен өлшенеді.
Әсіресе, иінді білік пен іргелік подшипниктер мұқият ақаулыққа тексеру жүргізеді.
Иінді білік жағдайын тексеру біліктің іргелік подшипникпен қосылған жеріндегі, шатундық нобайының шатунмен байланысу жеріндегі саңылаулықты және же мойындардың алшақтауы бойынша білік өсінің жағдайын тексеруден басталады.
Білік мойнын пішінінің ауытқу жәрежесін тексеру индикатор бар микрометрлік скобаның көмегімен жүзеге асырылады. ( микрометрдің өлшеу бірлігі 0,01 мм )
Өлшеу үш қимада жүреді, мұның біреуі мойынның ортасында, ал қалған екеуі галтеде 5 – 10 мм қашықтықта жатады. Әрбір белдеуде өлшеу екі жазықтықта жүреді – тік және горизонталь. Егерде білік мойынның ауытқуы мұмкін шектен асып кетсе, мойынды ажарлайды. Ажарлаудан кейінгі білік мойынның диаметрінің мүмкін кішіреюі диаметрінің бастапқы шамасының
3 % аспауы тиіс. Мойынның елеулі тозуы барысында қосымша бөлшек орнатуға рұқсат етіледі – қаптама ( өзара және білік мойынмен пісіру арқылы қосылысатын екі жарты бөліктен тұратын ).
Иінді біліктің мойыны мен галтелдегі анықталған сызаттар мен жоншақтар орындар ажарлаумен немесе кейін ажарлап отырып жонады. Жөнделінген білік мойнының диаметрінің ауытқу шамасы шектен аспауы тиіс.
Білік мойнының артықша диамтерін қалпына келтіруді балқыма қабат төсеудің көмегімен жүреді. Жарғыншақтар пісіріп бітеумен, ал иілуді механикалық термиялық және термомеханикалық тәсілдермен қалыпқа келтіреді.
Іргелік подшипникті ақаулыққа тексеру келесі операцияларды қарастырады: иінді біліктің мойнының алшақтауын екі жағдайда тексеру; тік клмпрессорлар үшін жоғарғы сынадағы саңылаулықты және горизонталды компрессор үшін бүйірлік сыналарды тексеру; подшипниктің баббиттік құймасының жағдайын тексеру; сындар жатысуын тексеру. Бүйірлік саңылаулықтар қуыс құл қорғасын сымының жаншылу шамасын тексереді.
Сырғанау подшипнигінің тозуының негізгі түрі бұл, фрикцияға қарсы құйманың өлшемі мен пішінінің өзгеруі. Жөндеудің негізгі әдісі ( подшипниктердің екі жартысы арасындағы төсемнің қалыңдығын өзгерту жолымен саңылаулықты реттеу мүмкіндігін болмаған жағдайда ), бұл антифрикциялық қоспаны қайта құйып, сонан соң қашау, шаберлеу және білік мойны бойынша өңдеп келтіру.
Шатун жарғынгшақ пен деформацияның болмауына тексереді. Жарғыншақтарды, алдын қарастырылған жарықтық тәсілмен анықтайды. Жарғыншақ анықталған жағдайда шатунды ауыстырған жөн. Шатун стерженінің майысуын суық күйде түзетумен жояды. Кривошипті және крейскопты шатун бүршігінің саңылауларының өсінің параллельдігін арнайы аправкаларды қолданумен тексереді. Парол болмауы бұралғандығын білдіреді. Бүршігі бұралған шатунды ауыстырады.
Шатун бүршігінің сыналары, елеулі қажалған кезде ауыстырылады. Кривошипті бүршіктің алмалы болып келеді, және де сынаның елеусіз қажалуы төсемнің қалыңдығын азайтумен компенсациялауға болады. Сынаның елеулі қашалуы кезінде ауыстырылады. Мұндай талап шатунның крейцкофтық бүршігіне де қойылады.
Крейцкоф құрыштың қаңқадан, шойындық баббитті құймасы бар башмактардан, шатунды бекітуге арналған саусақшадан, штокты бекітуге арналған гайка мен муфтадан тұрады. Крейцкофты тексеру барысында тіректік беттердің тығыз жатысуы мен шаршау жарғыншақтарының болмауына үлкен көңіл бөлінеді. Қауіпті қималар жарықтық немесе ультрадыбысты ақау көшіру әдісімен тексеріледі.
Поршенді тексеру барысында алып жүруші беттердің жағдайын, оршықтарының желіну шамасын, поршендік сақиналардың үшін оршықтың тозу дәрежесін, поршендік сақиналардың тозу жәрежесі мен күйін тексереді.
Поршен, мүмкін шамадан асатын сынақтар, жарғыншақтар болған жағдайда және тозғанда, сондай-ақ поршендік сақиналарға арналған оршықтар желінгенде ауыстырылады.
Поршендік сақиналарды, жұмысшы беттерінің күйінің тексеруге басты көңіл бөлінеді, және де сақинаның тозу шамасы мен бүйірлік саңылаулықтар анықталады.
Штокты тексеру барысында бұранданың жағдайын, штоктың деформациялануының болмауын тексереді.
Шток, сальниктік тығынмен жанасар орындарында елеулі тозуға ұшырайды. Штоктың елеулі тозуы кезінде, оны балқыма қабат төсеумен немесе хромдаумен қалпына келтіруге болады. Бұл кезде қалпына келтірілген орын жону немесе ажарлау көмегімен өңделеді.
Цилиндрлер өзіндік техникалық күйі бойынша компрессор жұмысының көрсеткішіне елеулі әсер ететін бөлшектер қатарына жатады. Жұмыс істеу процесінде цилиндр диаметрі алғаш диаметрге қарағанда елеулі ұлғаяды және де дұрыс диаметриялық пішіні өзгереді. Цилиндрді ақаулық көшіру барысында оның бетінде сызаттар мен жарғыншақтардың және басқа да жарғыншақтардың болуын тексереді. Цилиндрдің тозу жәрежесін өлшеу үш қимада ( ортаңғы бөлігіндежәне перпендикулярмен артқы ұшынан 30 – 50 мм ара-қашықтықта ) және әрбір қима үшінішкі бетінде жарғыншағы бар цилиндрлер жарамсыз болып саналады, сондай-ақ өзіндік техникалық ресурсын атқарған және де үлкен диаметрге қашау мүмкін емес цилиндрлер ауыстырылады. Ал, басқа жағдайларда қалпына келтіру үшін жөнделген өлшемге өңдену әдісі қолданылады. Бұл кезде цилиндр үлкен диаметрге қашалады да, онда жөнделінген өлшемдегі поршень орнатылады.
Клапандардың тозуының негізгі түрлері, бұл егар саңылауында және табақшада шөгінділердің түзілуі, пластинаның, серіппесінің және пластинаның көтерілуінің шектегіштердің тозуы. Клапандар пластиналары жұмыстың пайдалану процесінде майысқақталады және де жарғыншақтардың қалыптасуы мүмкін. Пластиналар, клапандар көтерілуін шектегіштер және серіппелер көпшілік жағдайда жаңадан ауыстырады.
Пластинаның елеулі тозуы кезінде, оларды екі жақты ажарлау рұқсат етіледі. Беттердегі шөгінділер химиялық әдіспен тазартылады.
Станиналар мен қаңқалардың жөнделуі ондағы жарғыншақтарды пісіріп бітеумен және оның геометриялық жағдайын салыстырып дұрыстаумен (горизонталды және вертикалдағы) жүреді.
Компрессорды жөндеуден кейін жүргізіп, жаттықтыруды инструкцияға сай орындайды. Жүргізіп жаттықтыру барысында жарғыншақ температурасына цилиндрге және сальникке майлау майының берілуіне кривошипті-шатундық мезанизмдегі бөгде дыбыстардың болмауын және май тазартатын сүзгінің тазалығын бақылайды.
Қалыпты жұмыстың бұзылуы кезінде компрессорды жедел тоқтату қажет. Жүргізіп жаттықтырған соң, кривошипті-шатундық механизм бөлшектерінің жұмыстық үйренісу сапасын тексереді.
Центрден тепкіш сорабын жөндеу
Центрден тепкіш сорапты жалпы өнеркәсіптік жабдықтардың кең тарған түрі болып табылады. Көпшілік жағдайда конструкциясы бойынша күрделі машиналар мен аппараттардың жұмыс сенімділігі сораптың техникалық жағдайына байланысты болады. Жөндеу жұмысының мазмұны мен көлемі сораптардың конструктивті ерекшелігімен олардың типтік өлшемдеріне байланысты болады. Біршама, жалпылама жөндеу дұмыстары техникалық қызмет кқрсету кезінде – ротордың осьтік жүрісін тексеру; сальниктік тығын мен қоршаған қауызды тексеру; жартылай муфталардың күйін тексеру (ақаулық бөлшектерді ауыстырумен) мойын толтыру немесе ауыстыру.
Жеңіл-желпі жөндеу кезінде тезникалық қызмет көрсетуі кезінде орындалатын жұмыстардан басқа келесі жұмыстар жүреді – торап қаңқасындағы ротордың тығыздалу құрылғысындағы саңылауды тексерумен толық бөлшектеу; ротордың соғуын тексеру.
Күрделі жөндеу кезінде техникалық қызмет пен жеңіл-желпі жұмыстардың барлық түрі және қысқаша барлық жұмыстар орындалады. Барлық жинақ бөлшектердің тексеріледі. Біліктің жұмыс доңғалағын, нығыздағыш сақинаны, грунд буксаның қорғағыш төлкесін ауыстыру; қаңқаны жөндеу.
Ценрден тепкіш сорапты жөндеу барысында келесі тәртіп сақталады:
Сорапты бөлшектеу; жуу және бөлшектерді тазалау; түйіндер мен бөлшектерді тексеру; тозығы жеткен ақаулыққа бөлшекті жөндеу немесе жаңадан ауыстыру; сорапты құрастыру; жүргізіп жаттықтыру және сынау; жұмысты пайдалануға тапсыру.
Бөлшектерді ақаулыққа тексеру алдын ластардан тазалау, майсыздандыру, кептіру қажет.
Көптеген жағдайларда центрден тепкіш сораптары коррозиялық белсенді ортаны айдау үшін қолданылады. Сонымен қатар, тасымалданушы сұйық құрамында интенсивті абразивті тозуды тудыратын қатар немесе қоспалар болуы мүмкін. Сондықтан да, жұмыстық пайдалану процесінде қаңқа қабырғасының қалыңдығын өлшеу қажет. Сораптың қаңқасының минимал мүмкін қалыңдығының шамасын келесі өрнек бойынша анықтауға болады:
δ0 = 1,9 (Р.Д)/σφ
Мұндағы: δ0 – сорап қабырғасының жарамсыздық қалыңдығы, м;
Р – сораптағы жұмысшы қысым, мПа;
Д – сорап қаңқасының ішкі диаметрі, мм;
σφ – қаңқаның материалына және жұмысшы температураға байланысты болатын мүмкін шекті кернеу, мПа;
Келтірілген қатынастылық гер де қаңқаның қалыңдығының диаметріне қатынасы 10 үлкен болса, онда ақиқат. Бұл қатынастылықтың аз мәнінде есептеулерді келесі өрнек бойынша жүргіземіз:
Сораптың қаңқасын тексеру барысында келесі беттердің техникалық күйінің тозу дәрежесін анықтауға аса үлкен мән беру қажет: 1) подшипникпен грунд букса (сырғанау беттері); 2) сораптың ішкі құрастыру; 3) тығыздаушы беттердің жағдайы; 4) секциялар мен доңғалақтың нығыздаушы саңылаулары арасындағы саңылаулықтың шамасы.
Жөндеуден соң центрден тепкіш сорабын сынау келесі жұмыстарды қарастырады: 1) байқаушы іске қосу; 2) сорапты қыздыру; 3) жұмыс тәртібінде сынау.
Байқаушы іске қосулар кезінде қарқынды құбырдағы ысырма жабық болуы тиіс. Жетек іске қосылған соң біліктің айналу бағытын, амперметр бойына сораптың күш түйістіру шамасын орындайды, подшипниктің қызу дәрежесін, сондай-ақ жұмыс істеп тұрған сораптың шуының деңгейін бақылайды. Байқаушы іске қосу барысындағы жұмыс істеу уақыты 3 минутты құрайды.
Жұмысшы тәртіпте сынау кезінде іске қосу қарқынды құбырдағы ысырманы жабық тұрған жағдайда жүреді. Сорап білігінің айналу жиілігі қажет шамаға жеткеннен соң, ысырма 1/3 айналады. Сорапты жұмысшы тәртіпте жүргізіп жаттықтыру 2 сағат уақыт жүреді. Жұмысшы тәртіпте сынау процесінде байқаушы іске қосудағы сораптың жұмыс параметрлері бақыланады. Сынау аяқталған соң сорап окта бойынша жұмыстың пайдалануға тапсырылады.
Жарияланған-2015-10-16 20:13:40 Қаралды-23327
КЕМПРҚОСАҚ ДЕГЕНІМІЗ НЕ?
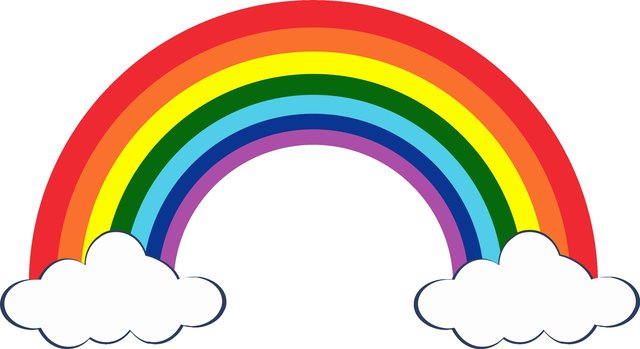
Адамдар бұл ең әдемі табиғат құбылысының табиғаты туралы бұрыннан қызықтырды.
- Информатика
- Қазақстан тарихы
- Математика, Геометрия
- Қазақ әдебиеті
- Қазақ тілі, әдебиет, іс қағаздарын жүргізу
- География, Экономикалық география, Геология, Геодезия
- Биология, Валеология, Зоология, Анатомия
- Әлеуметтану, Саясаттану
- Астрономия
- Ән, Мәдениет, Өнер
- Қаржы, салық және салық салу, банк ісі, ақша несие және қаржы
- Қоршаған ортаны қорғау, Экология
- Мәдениеттану
- ОБЖ
- Психология, Педагогика
- Тіл ғылымы, Филология
- Философия
- Физика, Химия
- Кітапханалық іс
- Спорт
- Автоматтандыру
- Аудит
- Ауыл шаруашылығы
- Биотехнология
- Бухгалтерлік есеп
- Журналистика
- Кедендік іс
- Құқық, Қоғам, Криминалистика
- Менеджмент, Маркетинг, Мемлекетті басқару, Метрология және стандарттау
- Өндіріс, Өнеркәсіп, Құрылыс, Мұнай-газ, Электротехника
- Туризм
- Халықаралық қатынастар
- Экономика, макроэкономика, микроэкономика
- Жаратылыстану
- Медицина